目次
概要
今や超小型の電子部品は、スマートフォン、自動車のナビゲーションや先進運転技術など、私たちの生活の根幹を支えるさまざまなアプリケーションに使用されています。当然、それらを検査する検査装置のソケット形状もさまざまです。スマートフォンなどの社会のインフラを支えるアプリケーションは、新しい商品のリリースサイクルも早いため、検査側のソケット形状もその度に変わっていきます。そのスピードに対応できる技術力はもちろんのこと、電子部品を検査する検査装置には、極小の電子部品の性能を正確にチェックできる高い測定精度や、高密度化が進む製品に対応するための狭ピッチが要求されます。
![[お客様最終製品]短期リリースサイクル:スマートフォンによってカメラの形状はさまざま。新商品が出てくるたびに毎回変わる。[検査装置]短期仕様変更[検査ソケット/ピン]短期形状変更:リリースサイクルに対応できる設計スピードで検査対象製品(DUT)に合った形状にカスタマイズ。=>スピード設計・高精度・狭ピッチ品が求められる](/sites/default/files/2023-03/efc-top_01_01.jpg)
オムロンの検査用ソケットは、独自*のEFC(Electro Formed Components)プロセス技術により製造したプローブピンを採用しています。金属の曲げ加工などでは製作困難な複雑な形状で、バネ性に優れた高耐久ピンを、ミクロンオーダーの精度で製作することが可能です。EFCプロセス技術と長年のノウハウにより、お客様の検査対象製品(DUT)に適した形状のソケットを、ポゴピン製の商品よりも優れた検査特性を実現し、かつポゴピン製と同等の設計スピードで提案します。高耐久性(長寿命)・高精度を誇るオムロンの検査用ソケットは、お客様のメンテナンス工数削減に大きく貢献します。また、高性能・高密度な製品の検査に対応した狭いピッチ間隔でのピン配置も、オムロンの板形状のプローブピンが得意とする領域です。
極小電子部品の検査に関するお悩み・ご相談は、オムロンにおまかせください。
*接点構造を形成する電鋳技術とその製造プロセスに関する2件の特許
(US8337261;US2013/0045617)を取得済み。
ポゴピンとオムロンのプローブピン(ブレードピン)
ポゴピンとは
一般的に、IC検査用ソケットには、検査装置側の回路基板と検査対象物(DUT)間を電気的に接続するための部品の一部として、ポゴピンと呼ばれる伸縮できる棒状のプローブピン(検査用ピン)が使用されています。ポゴピンは、主にプランジャ、バレル、バネの3点から構成されたピンのことを指します。ポゴピンは、プローブピンやスプリング(バネ付き)プローブ、コンタクトプローブとも呼ばれています。
しかし、機器の小型化や多機能化、高密度実装が加速していく中で、検査の高安定性・長寿命・狭ピッチ化・低接触抵抗など、ポゴピンでは対応が困難な検査ニーズが顕在化してきています。
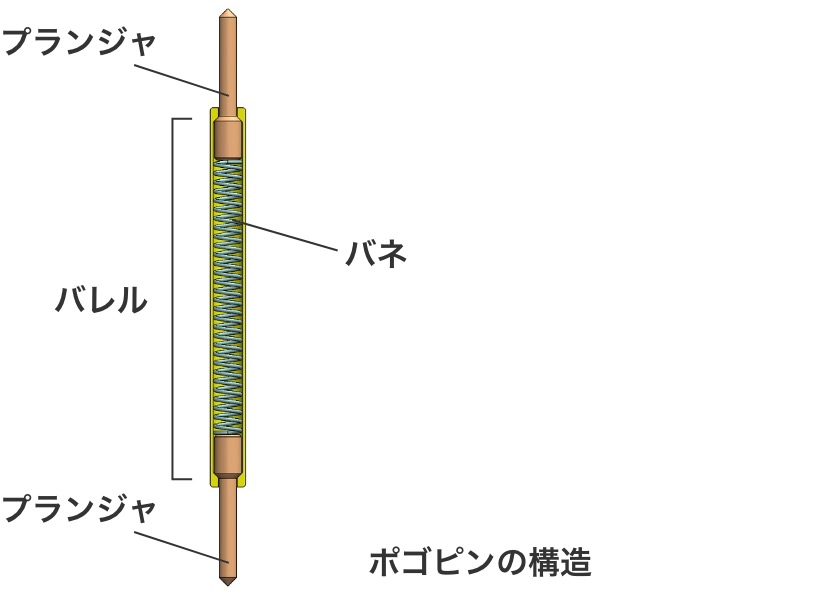
オムロンのプローブピン(ブレードピン)とは
オムロンの検査用ソケットは、オムロン独自*1 のEFCプロセス技術で製造したプローブピン(通称:ブレードピン)を採用しています。ブレードピンは、ポゴピンとは全く異なった構造を取っており、単一部品構成で複雑なピン形状を再現できるのが特長です。検査対象物(DUT)に適した接触部形状をカスタマイズ設計して提案します。また、オムロンのプローブピンは、優れた硬度とバネ性を備えたオリジナルの材料*2 を使用しています。
高耐久性・低接触抵抗・高い検査合格率・狭ピッチという4つの利点において、ポゴピンよりも優れたパフォーマンスを発揮します。
*1 接点構造を形成する電鋳技術とその製造プロセスに関する2件の特許
(US8337261;US2013/0045617)を取得済み。
*2 特許第5077479号(P5077479)
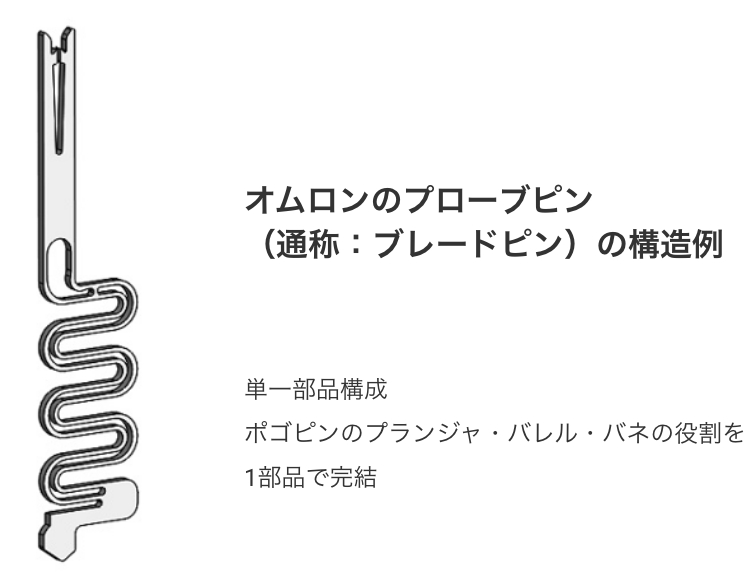
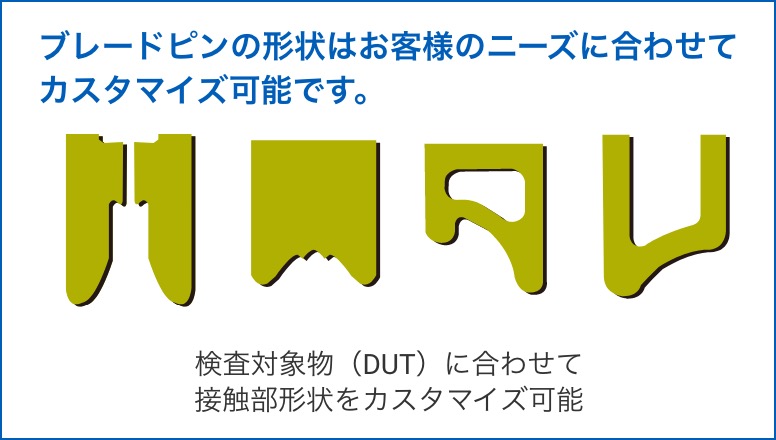
オムロンのプローブピン(ブレードピン)とポゴピンの比較
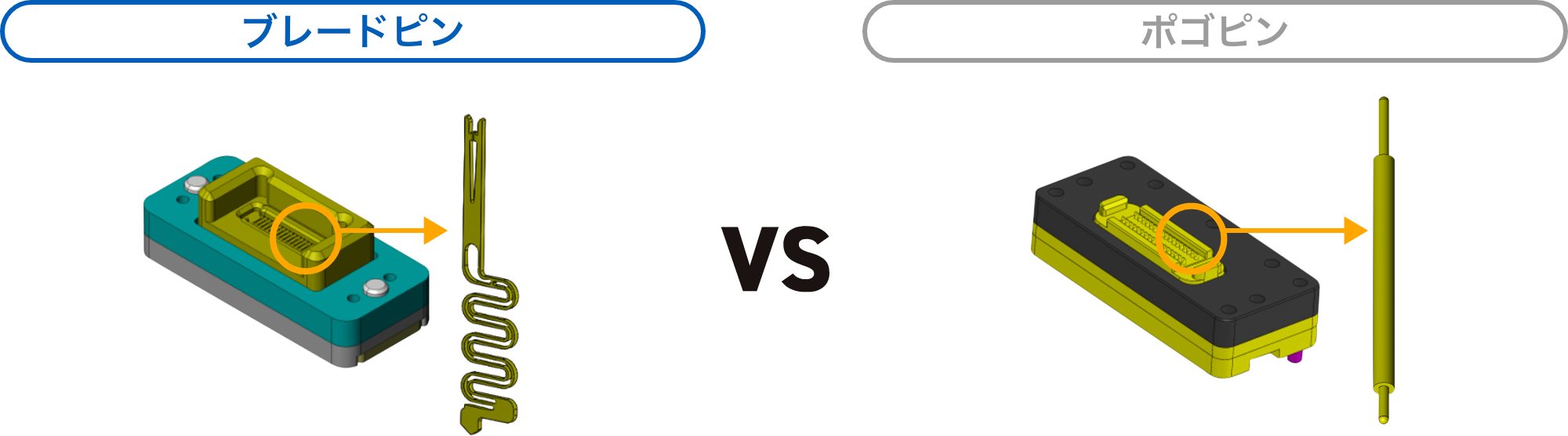
50万回以上 | ![]() |
10万回未満 |
30mΩ 低接触抵抗が求められる検査対象物に対しても高い検査精度を実現 |
![]() |
70mΩ 低接触抵抗が求められる検査対象物への使用が難しい |
99~100% | ![]() |
80~99% |
0.20mm以下 | ![]() |
0.35mm以上 |
*BtoBコネクタ検査の一例です。
ブレードピンが提供する4つの価値
半導体などの小さな部品の検査に用いられる検査用ピンは直径1mm以下と非常に細く、耐久性に課題を抱えています。私たちの生活に入り込んでいる半導体部品の検査回数は、一日あたり数万回から数十万回にもおよびます。そのためピンの耐久性が低いと、検査対象物(DUT)の検査要求によっては、検査機についている100から10,000本ものピンを毎日交換しなければなりません。オムロンの検査用ピンは、機械的耐久性が50万回以上(ポゴピンの約5倍以上)です。お客様のメンテナンス工数の削減と生産効率の向上に貢献します。
![]() |
![]() |
|
現場 | メンテナンスフリーで常時稼働 ![]() ピンが長寿命なため、生産効率がアップ |
定期メンテで稼働ストップ ![]() 検査対象によっては、 |
---|---|---|
機械的耐久性 | *50万回以上 | *10万回未満 |
*BtoBコネクタ検査の一例です。
長寿命を可能にするオムロンのEFCプロセス技術
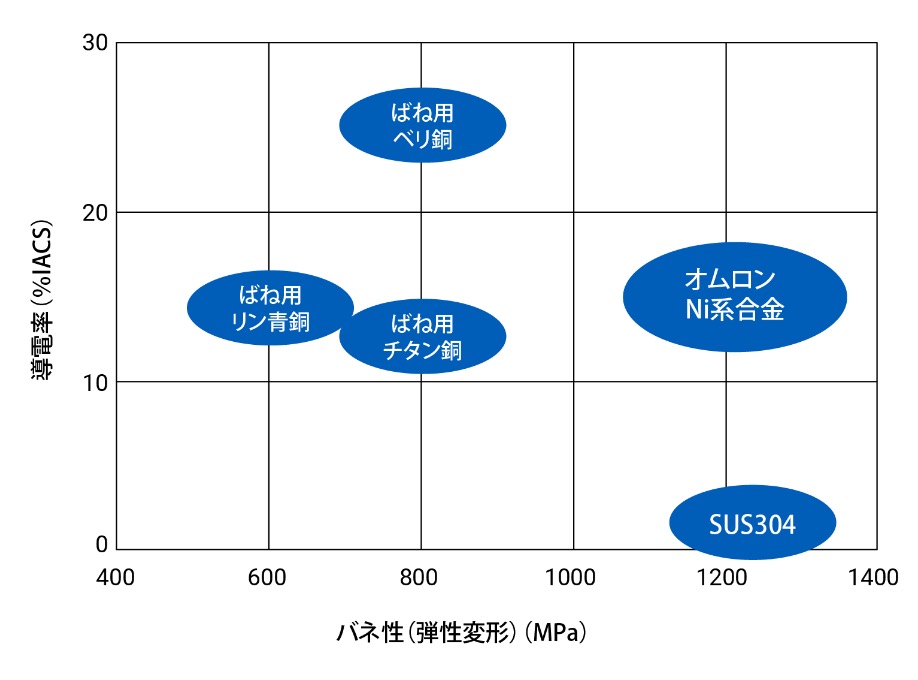
オムロンオリジナルの材料ブレンドで高いバネ性と導電率を実現
EFCプロセス技術だからこそ使用可能なオムロンオリジナルの材料を使用することで、機械的特性はSUS304と同等、電気的特性は銅合金と同等のスペックを有したピンの加工が可能です。
*特許第5077479号(P5077479)
コンピュータやテレビ、スマートフォンなどのディスプレイはどんどん進化を遂げています。より鮮明に、より操作感度のよい製品が出てくる中で、注目を集めているのがOLED(Organic Light Emitting Diode)です。従来のディスプレイとして使われることが多かった液晶は、自ら発光しないため、別に光源が必要となります。しかし発光材料に有機物質を使用したLEDであるOLEDは、電流を流すと自然発光するため、別光源が必要ありません。そのため、今のディスプレイのニーズに合った、非常に薄くて軽いディスプレイを構成することが可能です。
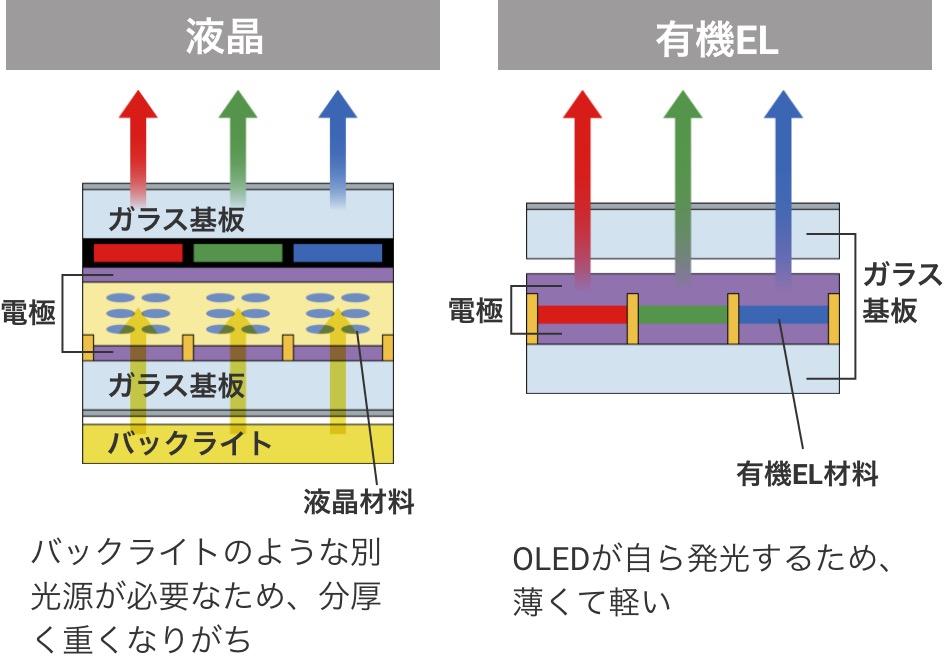
そのような、メリットの高いOLEDですが、電気的特性を検査することが難しいアプリケーションでもあります。OLEDは内部の抵抗が非常に低いため、検査ソケット側の抵抗が高い場合、OLEDを発光させるための十分な電流が確保できず、輝度の検査を行うことができません。検査機器側の抵抗は低いほど、アプリケーション側の正確な性能検査を実施することができるのです。
オムロンのプローブピン(ブレードピン)はポゴピンの半分以下の30mΩという低接触抵抗で、機器の検査を妨げません。高精度でスムーズな検査を可能にします。
![]() |
![]() |
|
現場 | 検査ができる ![]() 検査機器側の接触抵抗が低いため、内部抵抗の |
検査ができない ![]() 製品自体は試験に合格できる性能を有していても、検査機器側の接触抵抗が高いため、正しい検査が行えない |
---|---|---|
接触抵抗 | *30mΩ | *70mΩ |
*BtoBコネクタ検査の一例です。
低接触抵抗を可能にするオムロンのEFCプロセス技術
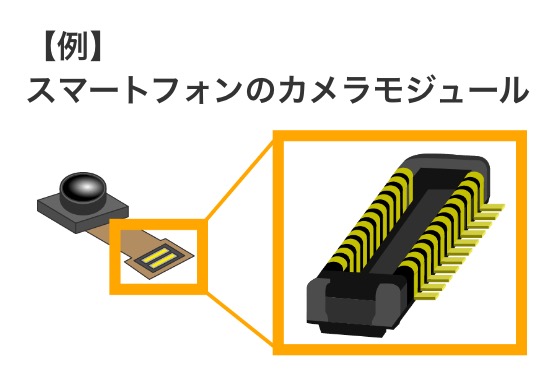
面で接触する設計デザインで抵抗値を大幅に低減
例えばカメラモジュールに使われるBtoBコネクタは、端子の導通部分が上に盛り上がった形状になっています。このような端子形状の製品に検査ピンを当てる場合、ポゴピンは「点接触」のため、安定した機械的接触を保つことが難しく、機械的にも電気的にも安定した検査をおこなうことが困難です。しかしオムロンのEFCプロセス技術であれば、お客様のアプリケーションに適した形状のブレードピンをカスタマイズすることが可能です。「面接触」の設計で、高い接触信頼性を実現します。
ブレードピン
ブレードピンとコネクタ導通部の接触面積が大きいため、
接触抵抗が低い
ポゴピン
ブレードピンとコネクタ導通部の接触面積が小さいため、
接触抵抗が高い
オムロンのブレードピンは99~100%という非常に高い検査合格率を誇ります。検査ピンの接触不具合による不合格品の発生は1%未満で、お客様の製品の廃棄ロス削減に貢献し、生産効率の良い検査を実施いただけます。
検査合格率の高さは、不良分析にもメリットをもたらします。製品の不良分析はより良い新商品を生み出すための重要な要素の1つです。しかし、検査機側事由での不合格品が多い場合、「何が不良の原因なのか」を正しく分析が行えません。オムロンのブレードピンであれば、検査ピンと検査対象物(DUT)の端子の接触不具合による不合格品はほぼ発生しません。検査機起因の不良要因を可能な限り減らし、より精度の高い製品不良分析結果を、製品に適切に反映いただけます。
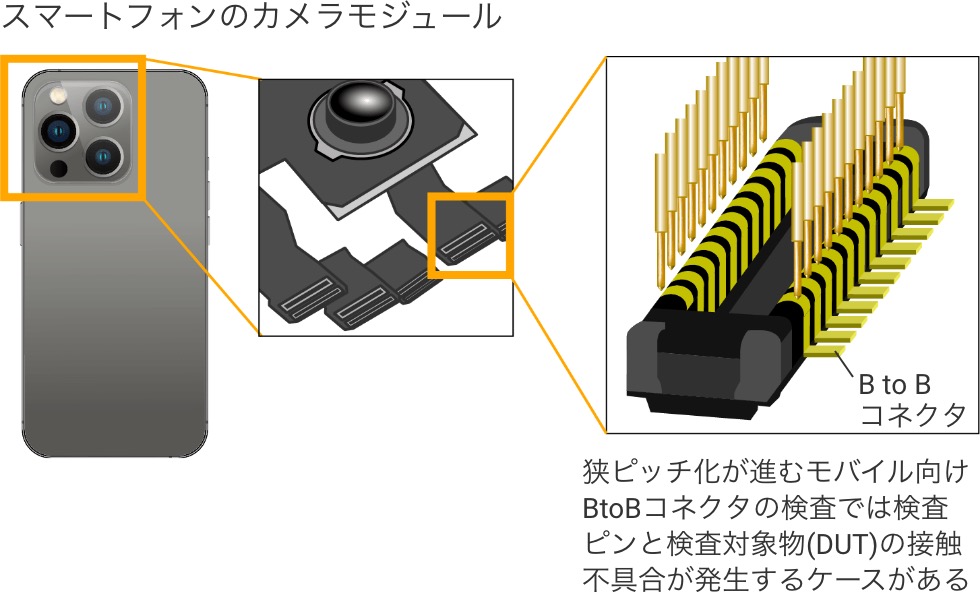
![]() |
![]() |
|
現場 | お客様の製品のスペックを正確に測定判断 ![]() 廃棄ロスを削減、 |
検査ピンの接触不具合により、スペックを満足している商品でも、検査で不良判定となってしまう ![]() 廃棄ロスが発生、 |
---|---|---|
検査合格率 | *99~100% | *80~99% |
*BtoBコネクタ検査の一例です。
高い検査合格率を可能にするオムロンのEFCプロセス技術
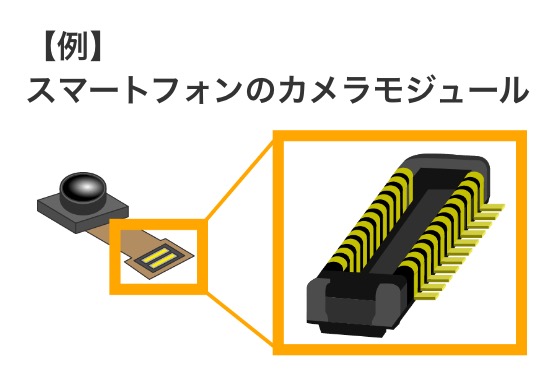
面で接触する設計デザインで接触不良を大幅に軽減
例えばカメラモジュールのBtoBコネクタは、端子の導通部分が上に盛り上がった形状になっています。このような端子形状の製品に検査ピンを当てる場合、ポゴピンは「点接触」のため、接触不良が発生しやすくなってしまいます。しかしオムロンのEFCプロセス技術であれば、お客様のアプリケーションに適した形状のブレードピンをカスタマイズすることが可能です。「面接触」の設計で、信頼性の高い接触を実現します。
ブレードピン
ブレードピンと導通部が面で接触するため、接触不良がほぼなく、安定した機械的・電気的接触を実現
ポゴピン
ポゴピンとコネクタ導通部が点での接触のため、機械的・電気的に安定した検査が困難
接触不良が発生しやすい
オムロンは、ポゴピンでは困難な0.35mm以下のピッチ幅に対応可能な検査用ピンの提供が可能です。最小0.175mmまでの狭ピッチに対応可能で、高密度実装による多機能化が進むカメラモジュールやディスプレイモジュールでも、精度の高い検査を実施いただけます。お気軽にご相談ください。
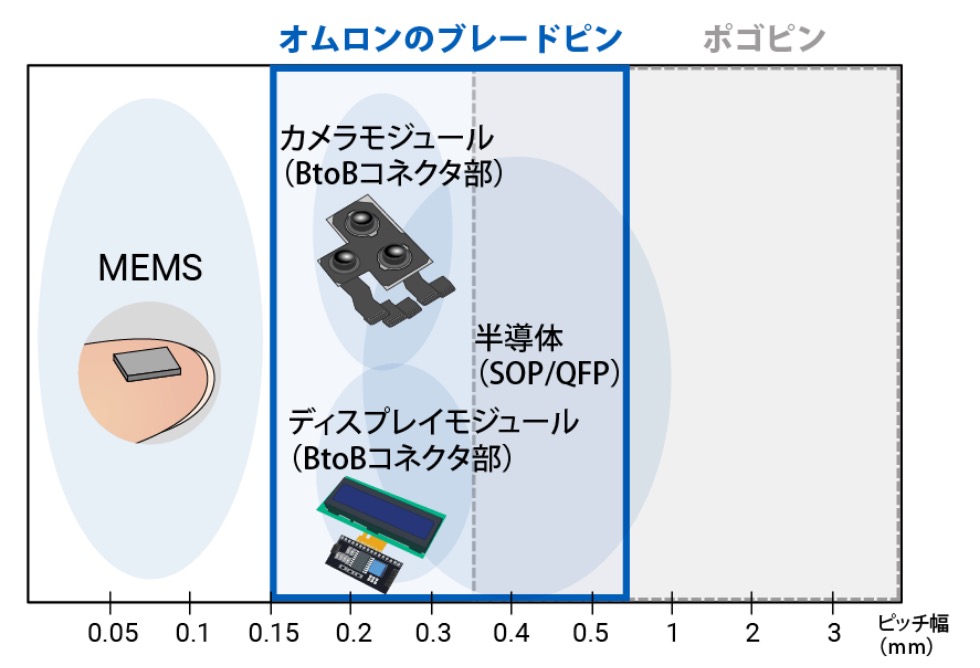
スマートフォンのカメラモジュール
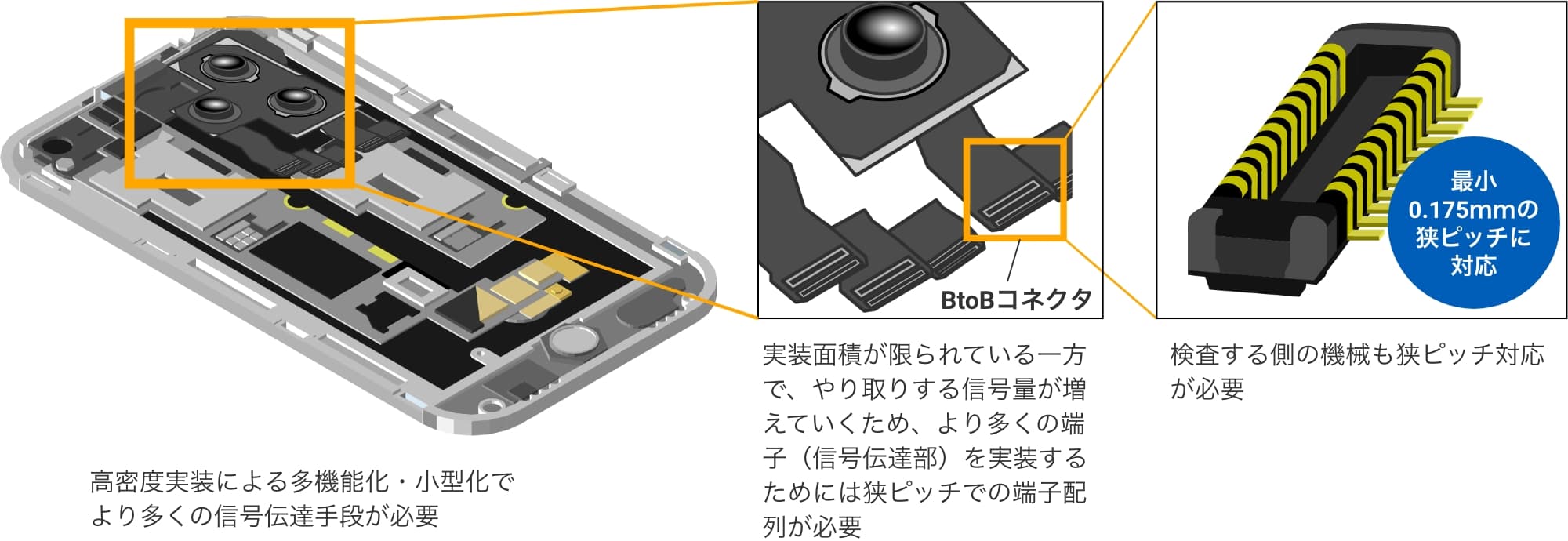
![]() |
![]() |
|
現場 | 高密度実装が進む検査対象物でも ![]()
|
極小電子部品の検査に対応できない ![]() 立方体で幅をとるピン形状。 |
---|---|---|
仕様 | *最小0.175mmピッチ | *最小0.35mmピッチ |
*BtoBコネクタ検査の一例です。
狭ピッチを可能にするオムロンのEFCプロセス技術
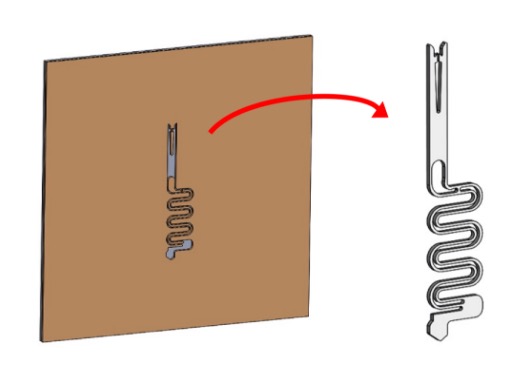
EFCプロセス技術
金属を型版に析出させる工法
金属を型板に析出させて形成されるオムロンのブレードピンは、板状のため、狭いピッチで並べて使用することが可能です。対して、ポゴピンは円柱状の形状をしており、板形状のブレードピンに比べ、実装スペースを占めるため、ブレードピンと同等のピッチ幅で使用することは困難です。
ブレードピン
板形状のため狭ピッチ化が可能
最小0.175mmのピッチ幅
ポゴピン
円柱状のため、板形状のブレードピンに比べると、
狭ピッチ化が難しい
最小0.35mmのピッチ幅
オムロンの検査ソケット
検査ソケットは、半導体製造工程の最終検査で使用されており、検査装置と検査対象物(DUT)を接続する重要な役割を担っています。
オムロンはお客様の要求に応じて、幅広いタイプのソケットを取り揃えております。お客様の検査対象物に適したタイプを最適な形状でカスタマイズし、短納期で提供します。
オムロンのEFCプロセス技術(電鋳微細加工技術)
オムロンの極小電子部品用の検査用ソケットとピンは、EFCプロセス技術と膨大な電子部品設計におけるノウハウの複合により生み出されています。
EFCプロセス技術は、電鋳微細加工技術の1種です。従来のプレス加工などでは困難だった高精度で複雑な形状加工を極小サイズで再現することが可能です。
EFCプロセス技術は、他の技術では実現困難な4つの価値をお客様に提供します。

EFCプロセス技術だからこそ実現できる4つの価値

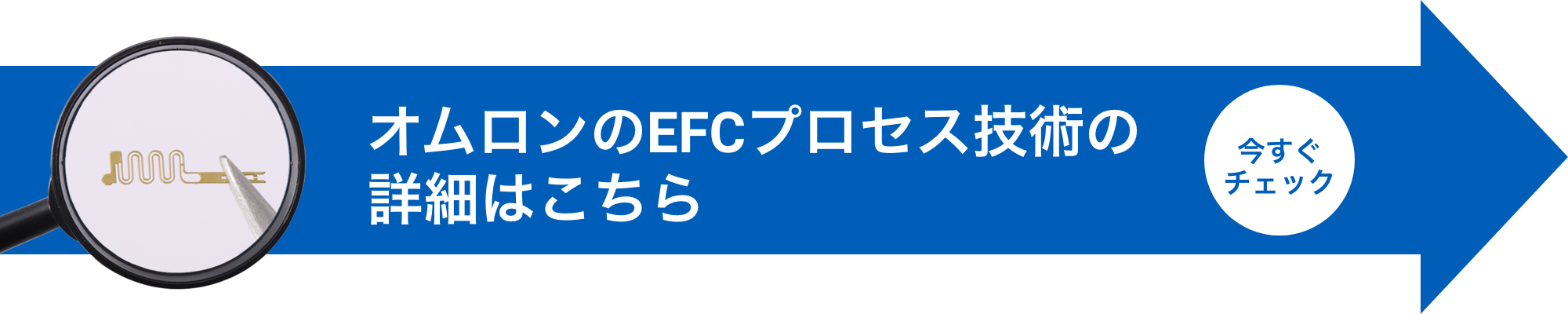