このようなお悩みをお持ちではないですか?

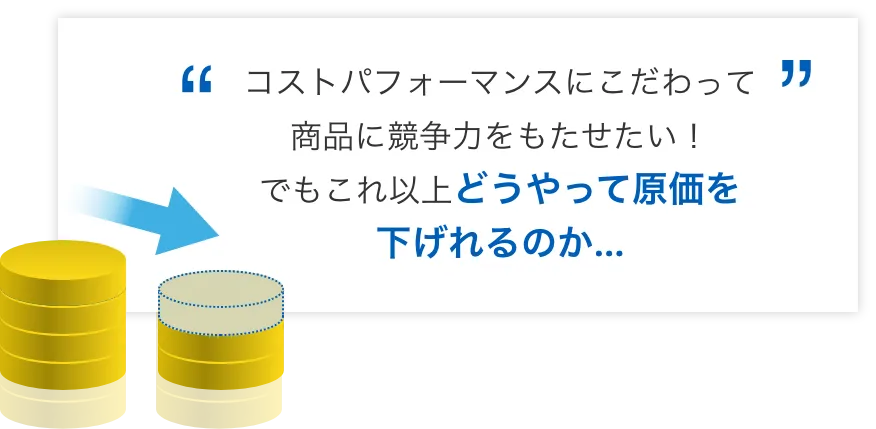
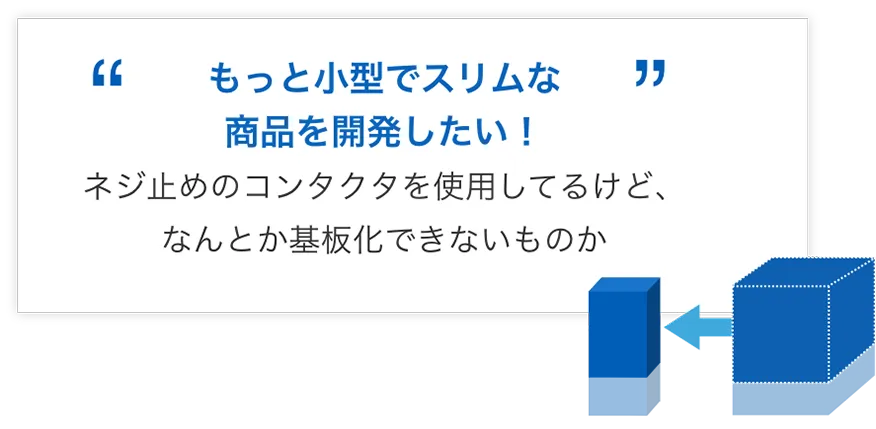

お客様製品の高容量化に伴い、大電流・高電圧を必要とする様々な電気機器の負荷開閉デバイスとして、大電力の制御に適しているコンタクタが活用されています。
しかし、機器の小型軽量化・薄型化のニーズの高まりから、実際にサイズの大きなコンタクタから、サイズが小さく大電流・高電圧の遮断が可能な高容量のプリント基板用リレー(PCBリレー)へ置き換えを検討する動きが増えてきています。
また、一部のお客様では、将来的な需要の急増や生産台数の拡大を見据え、生産時の工数削減の1つとして、PCBリレーを使用した負荷開閉デバイスの基板化による原価低減も進めています。
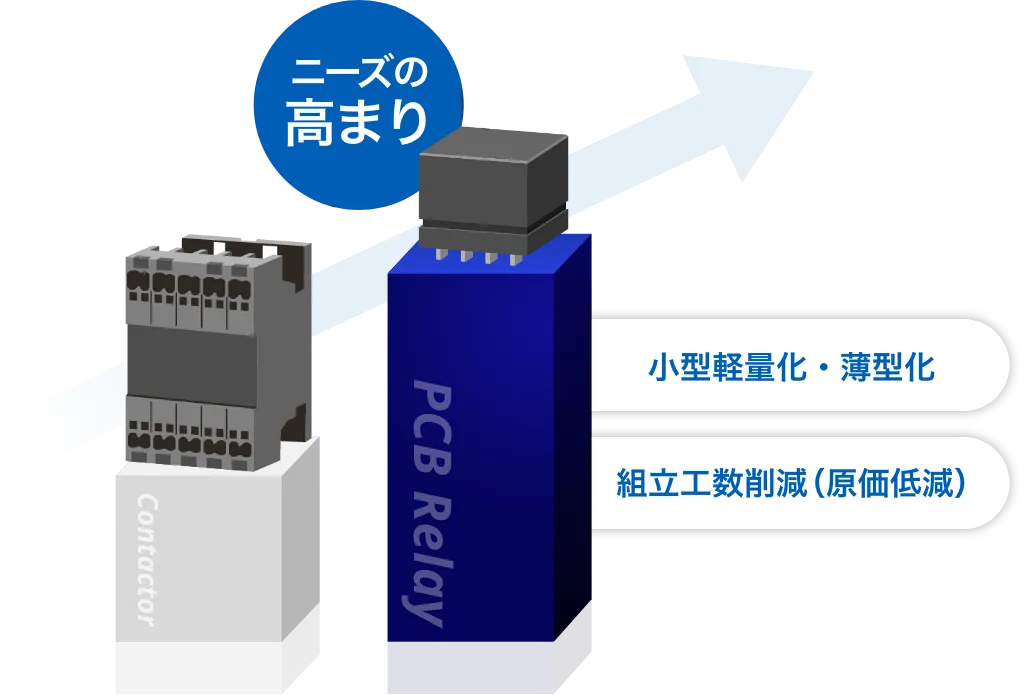
このように、コンタクタからPCBリレーへの置き換えが進んでいく中で、心理的な置き換えハードルとなりえるのはやはり、従来のケーブル配線から「基板化」することでの大幅な設計の変更ではないでしょうか。
この記事では、コンタクタも高容量のPCBリレーも保有するオムロンだからこそお伝えできる様々な置き換えメリットや注意すべきポイント、実際の置き換え事例、そしてPCBリレーの実装基板を設計するためのポイントについてご紹介します。
目次
- PCBリレーの進化と進む高容量化
- コンタクタから高容量のPCBリレーへの置き換え事例(Coming Soon)
- コンタクタとPCBリレーの違い
- コンタクタから高容量のPCBリレーへ置き換えるメリットは?
- コンタクタから高容量のPCBリレーへ置き換え時の注意点は?
- PCBリレーの実装基板を設計するためのポイントは?
- オムロンの高容量PCBパワーリレーラインアップ
PCBリレーの進化と進む高容量化
過去、コンタクタは30Aを超えるような大きい電流制御に、PCBリレーは30A以下の電流の制御に活用されてきました。しかし、技術の進歩に伴い、大電流に耐えられる厚銅基板や、大電流・高電圧を通電・遮断できる小型のプリント基板用リレ-(PCBリレー)が続々と登場してきています。
そのため、従来コンタクタでの制御が主流だった領域帯の一部がPCBリレーでも制御可能となってきています。
例えば、オムロンのPCBリレーの場合、~AC/DC1000V、~300Aまでの電流・電圧領域をカバーできるようになっています。
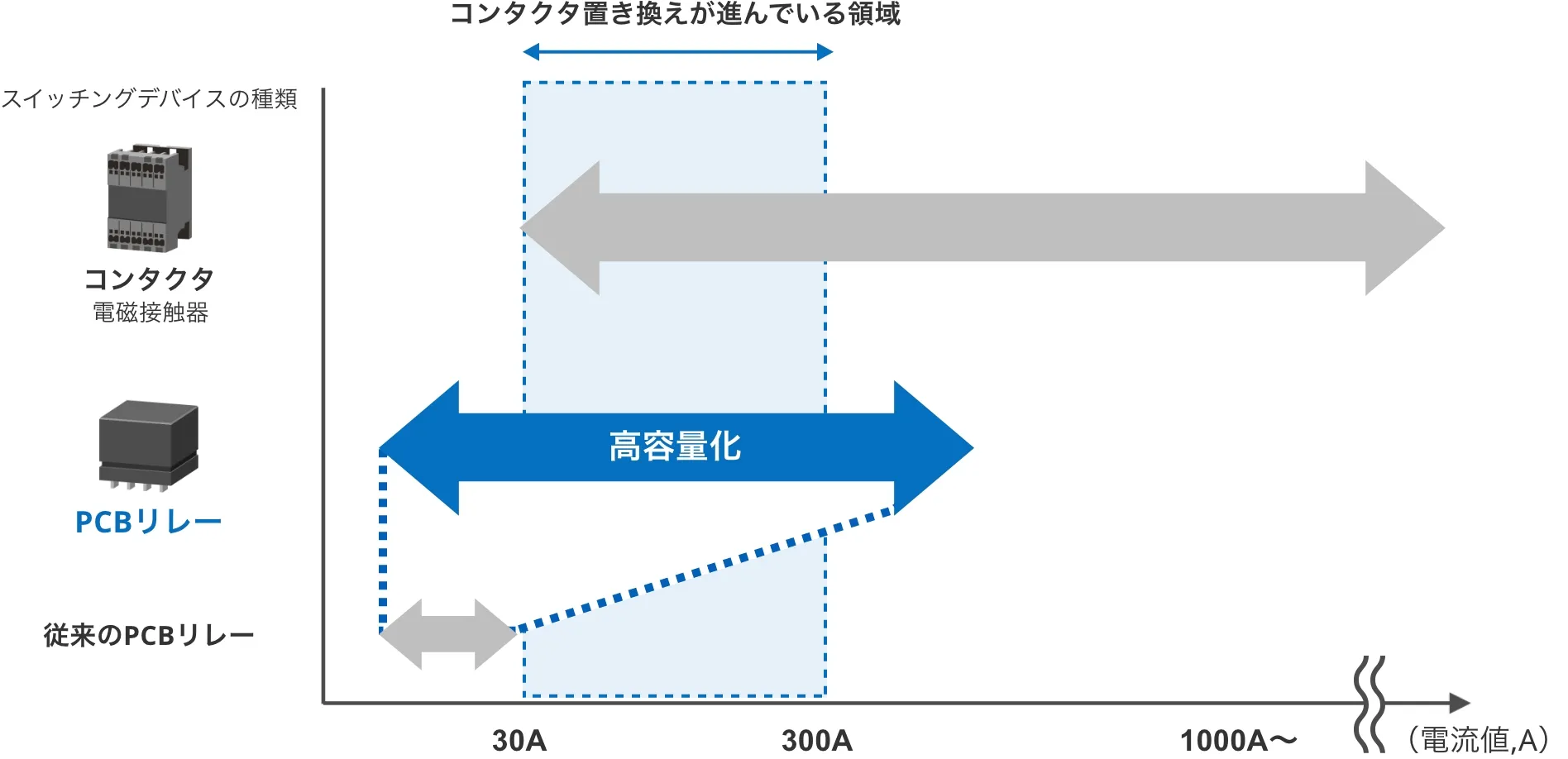
コンタクタとPCBリレーの違い
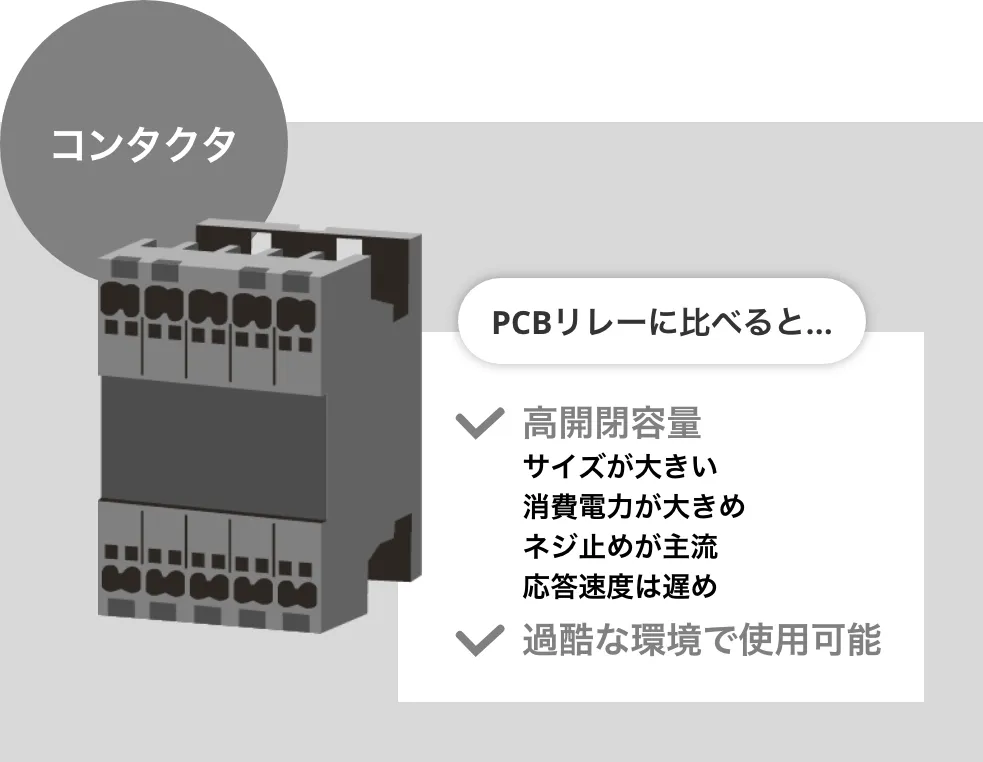
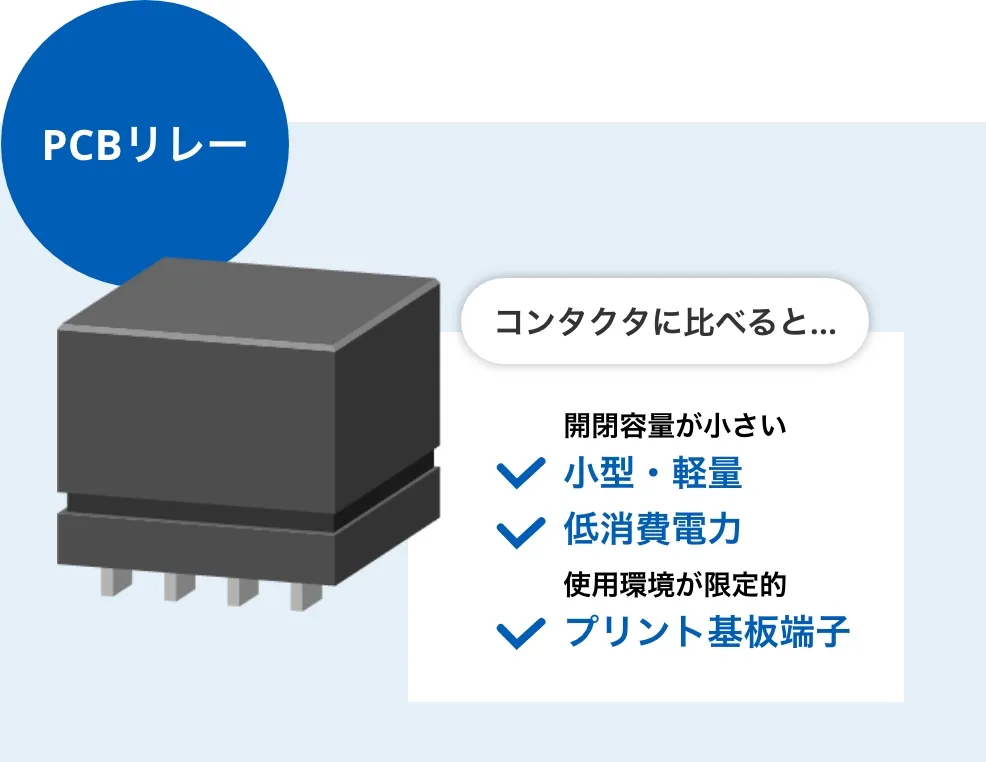
コンタクタとは
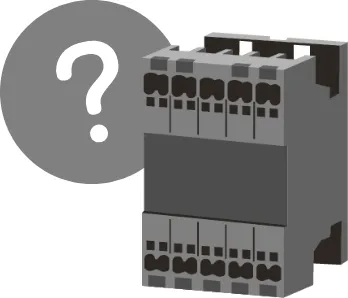
コンタクタは、大型の設備など(例:電気自動車のスターター、大型の照明制御システム)に適用されます。電磁接触器とも呼ばれます。リレーと比較して、大電流・高電圧を制御できるように設計されているため、堅牢性が高いです。その分、物理的なサイズや重量もリレーよりも大きく、スイッチング速度も比較的遅い傾向があります。また開閉容量に比例して電磁コイルが大きいため、消費電力も大きくなりがちです。取り付け方法としては、ネジ締め式が主流です。
PCBリレーとは
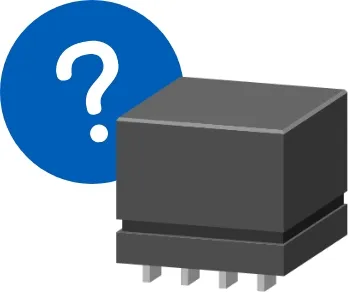
一般的に、PCBリレーはコンタクタと比較して、小容量の機器に適用されます。コンタクタと比較すると堅牢性は弱いものの、磁束設計、接点形状やアーク遮断経路の最適化、CAE解析の活用などで300Aという大きい負荷でも通電・開閉が可能になってきています。コンタクタと比べて、小型、かつ軽量で、低消費電力での駆動が可能です。端子形状はプリント基板端子(PCB端子)のため、基板や周辺部品(端子台など)と合わせて設計されます。
(当社商品例:G9KA、G9KB、G9KC)
省スペース設計の実現
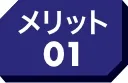
省スペース設計の実現
高容量のPCBリレーの大きなメリットは、プリント基板に直接実装するため、配線スペースを加味した場合、コンタクタに比べコンパクトにできる点です。例えば、エネルギー関連機器において、部品実装の省スペース化は機器全体のサイズダウンや配線の簡素化を可能にします。また、限られた設置スペースの有効活用にも貢献します。
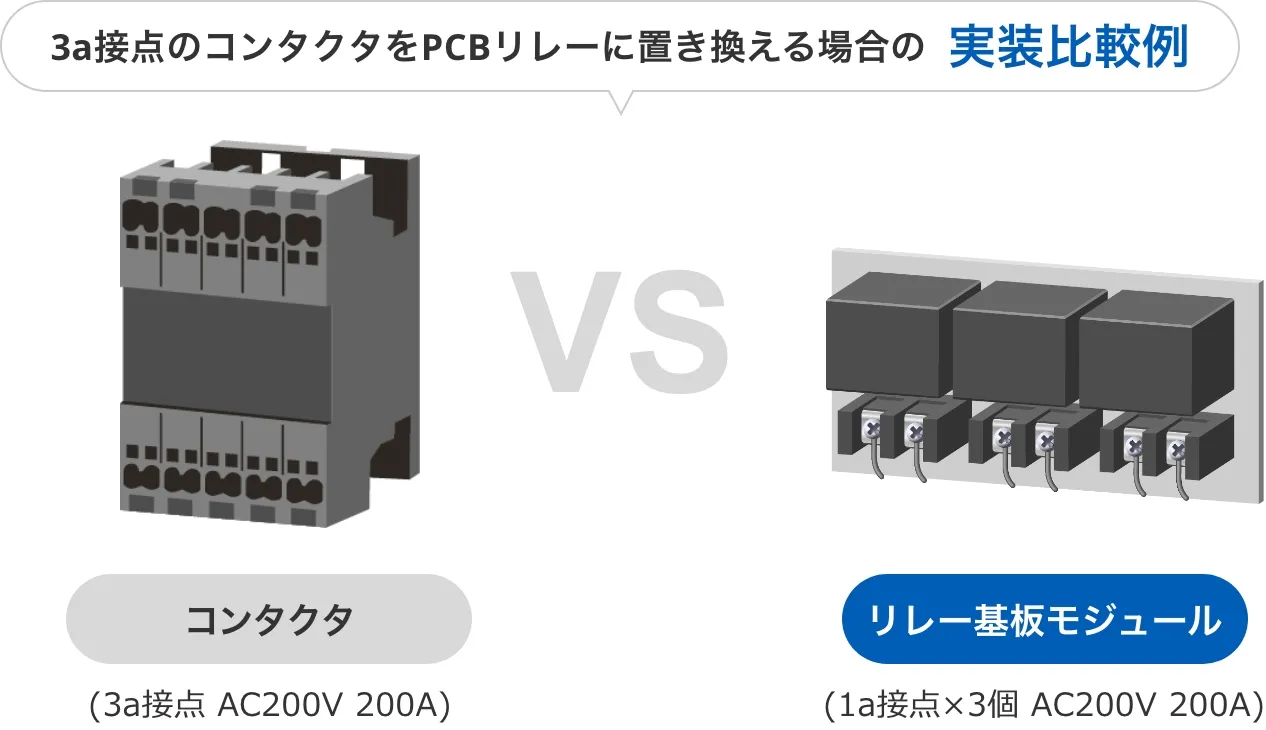
高さ | 約140mm |
55mm ![]() |
---|---|---|
体積 | 2,940,000mm3 |
425,000mm3 ![]() |
重量 | 約2.5kg/個 |
0.7kg/3個合計 ![]() |
注.200A帯の一般的なコンタクタと当社で想定するリレー基板モジュールの比較(2025年1月 当社調べ)
原価低減と量産の効率化
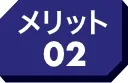
原価低減と量産の効率化
ネジ止めタイプが主流のコンタクタは、実装、配線の自動化が難しく、手作業による時間とコストがかかります。
対して、プリント基板用リレー(PCBリレー)は、ピックアンドプレースマシンやフローはんだ付け装置などの自動化装置で簡単に取り付けることができます。そのため、自動化製造プロセスに組み込みやすく、生産量が増えれば製造コストを大幅に削減できます。
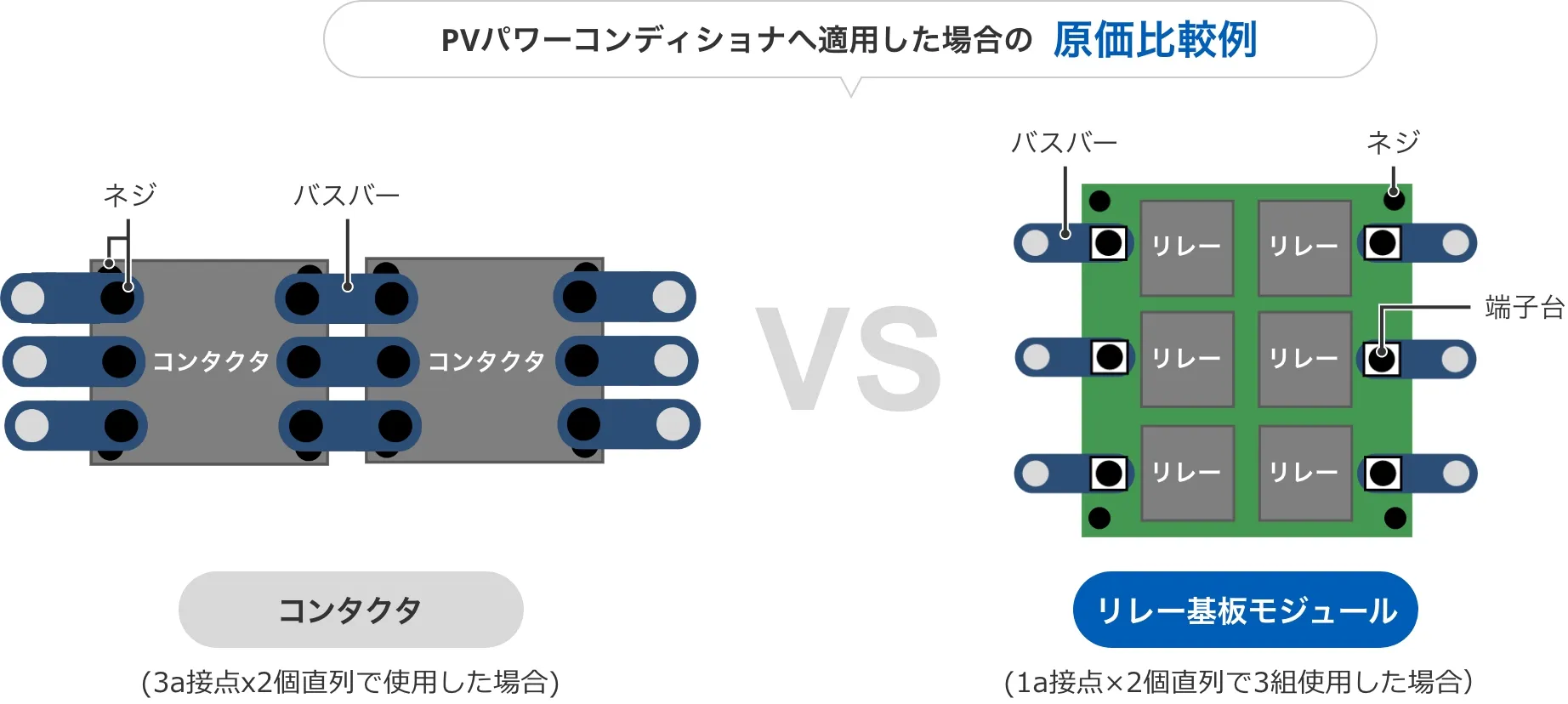
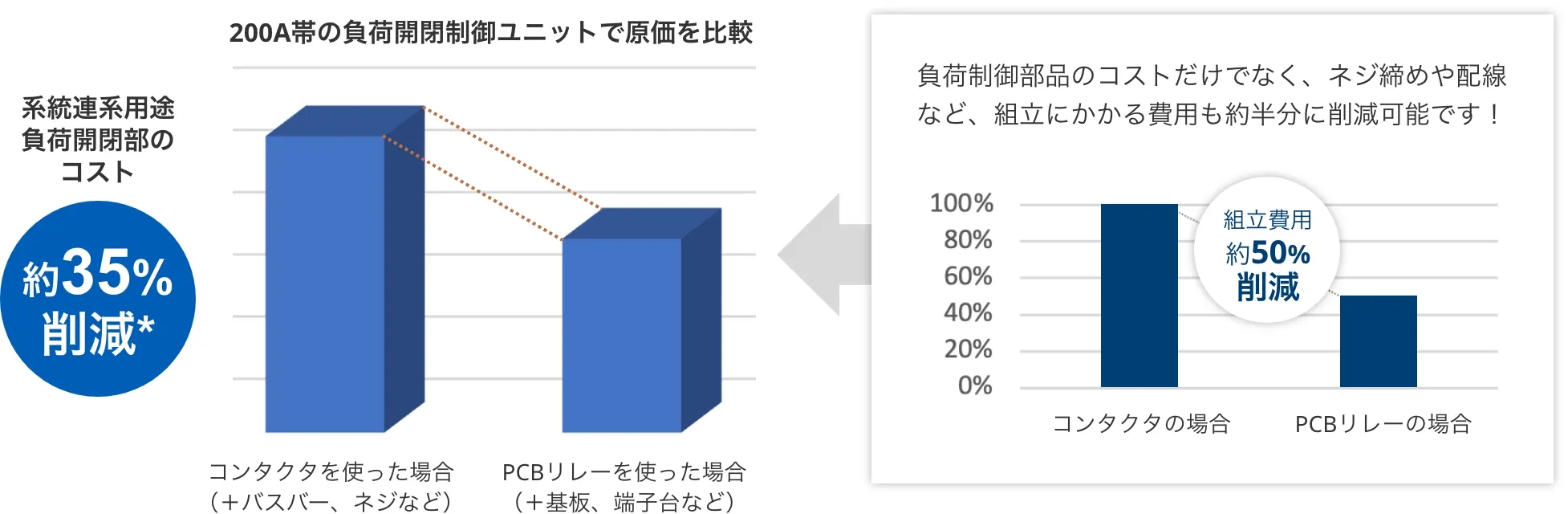
*コンタクタ(3a,200A)×2個をリレー(1a,200A)×6個に置き換える場合の制御ユニットのコスト比較。当社シミュレーション結果(2025年1月時点)
特定条件下でのシミュレーション結果であり、効果を保証するものではございません。
コンタクタと同等の安全機能
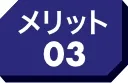
コンタクタと同等の安全機能
高容量PCBリレーには、コンタクタに要求される過負荷時の保護機能(溶着検知機能:IEC60947-4-1に適合したミラーコンタクト構造による補助接点オプション)や耐絶縁性が向上した製品も多く存在しています。コンタクタと同様に、高い安全性の確保に貢献します。
また、EV充電器の規格であるIEC62955に準拠した高い短絡電流耐量を有した機種や、太陽光発電規格であるVDE0126に準拠した接点ギャップ3.6mm以上の絶縁性能を担保した機種もあります。
このように、短絡や高電圧環境での信頼性も確保されている商品もございますので、エネルギー関連の機器においても安心して使用することができます。
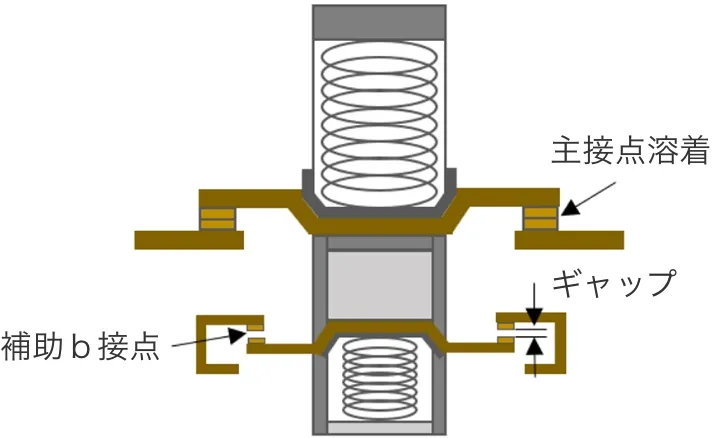
リレー本体と補助接点ブロックの組み合わせにおいて、リレー本体のa接点(主接点)が溶着した場合、コイルの励磁を解いても補助接点ブロックのすべてのb接点は、耐衝撃電圧2.5kV以上を満足、または接点間隔0.5mm以上を確保する構造
ミラーコンタクト構造 イメージ図
接続信頼性の向上
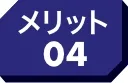
接続信頼性の向上
コンタクタのネジ締めは手作業で行われるため、ネジの締め方や締める強さなど、締結トルクは決められているものの、どうしても作業者による締結力のバラツキが生じるケースがあります。コンタクタの代わりにPCBリレーをご使用いただき基板化することで、ネジ点数を大きく削減することができ、接続信頼性の向上に貢献します。
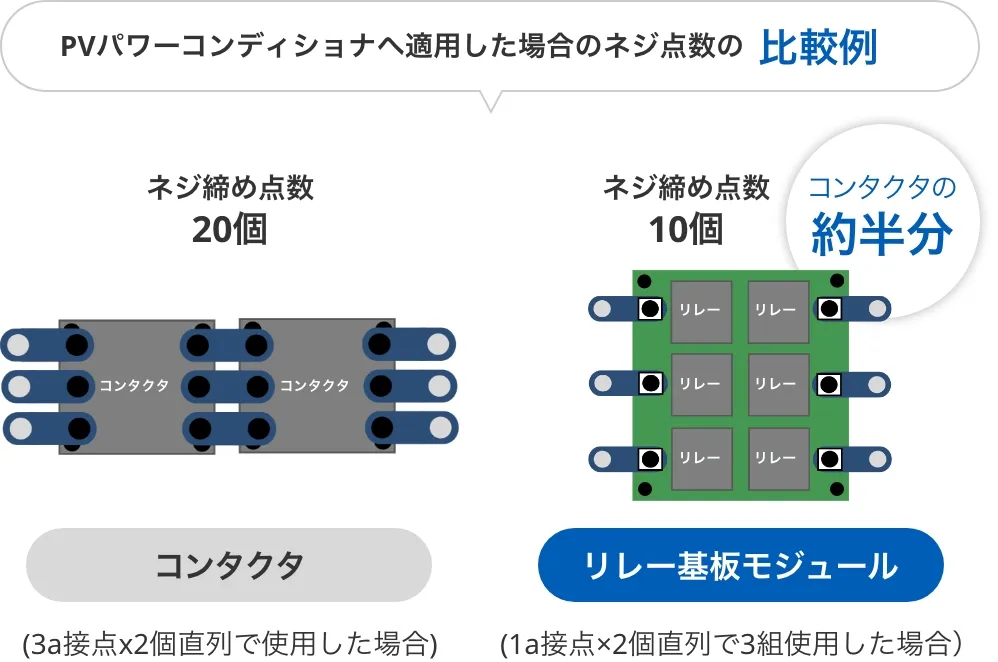
コンタクタから高容量のPCBリレーへの置き換え時の注意点は?
最大電流・電圧容量の限界
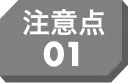
最大電流・電圧容量の限界
今や、PCBリレーの高容量化、コンタクタが主流の高出力領域での置き換えは目覚ましいスピードで進んでいます。しかし、基板の銅箔厚や基板に流せる電流値の限界から、PCBリレーが扱える最大電流は、高容量帯のコンタクタと比較すると低くなってしまいます。(当社リレーの場合、現時点では~AC/DC1000V、~300Aレベルの負荷に対応可能:2024年10月時点)。大規模な産業機器や三相モーターなど、非常に大きな電流を制御する用途では、コンタクタの方が適していることがあるため、負荷の要件に応じた選択が必要です。
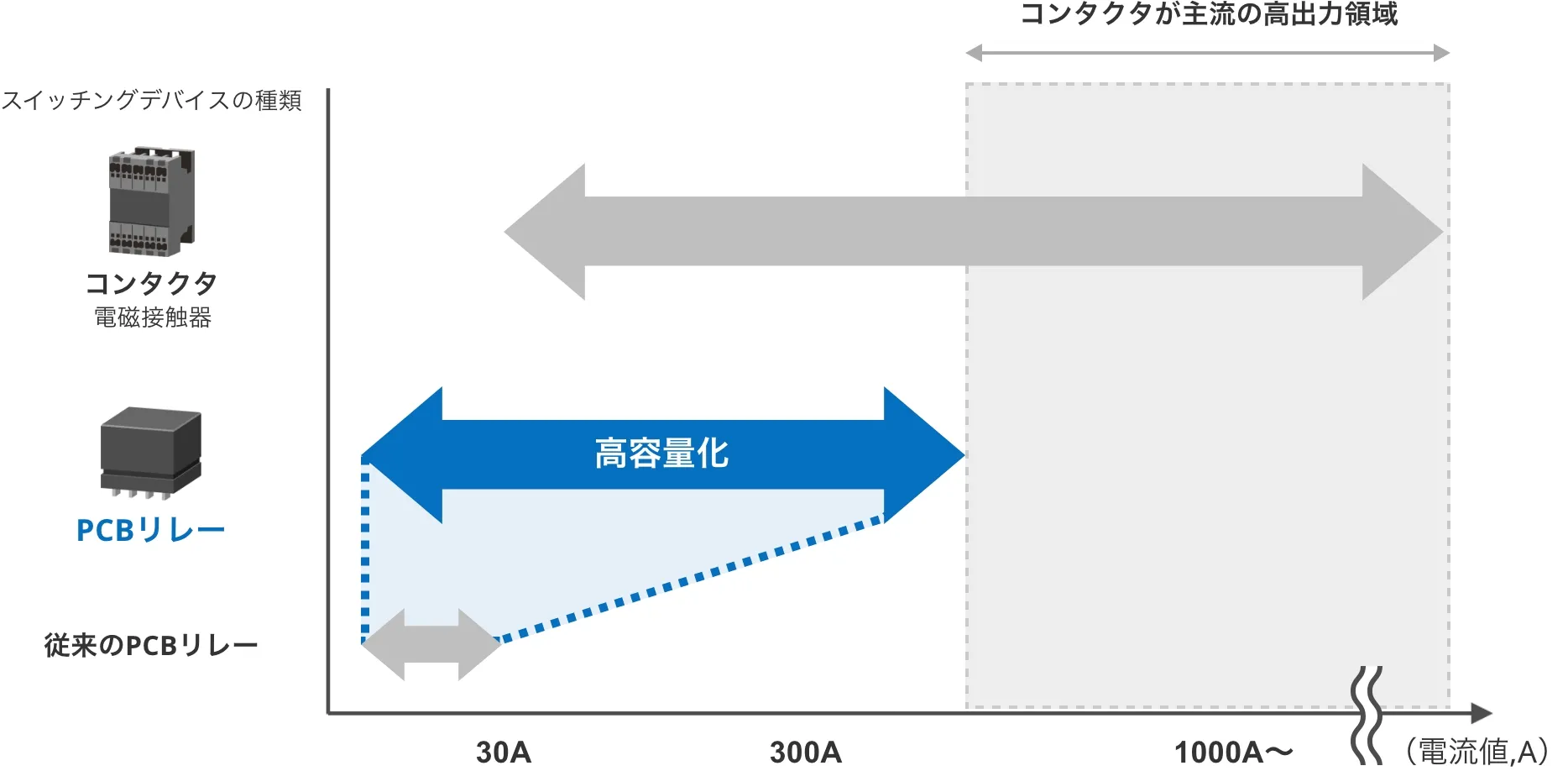
当社ではさらなる大電流、高電圧負荷が制御できるPCBリレーを順次ラインアップ追加しております。
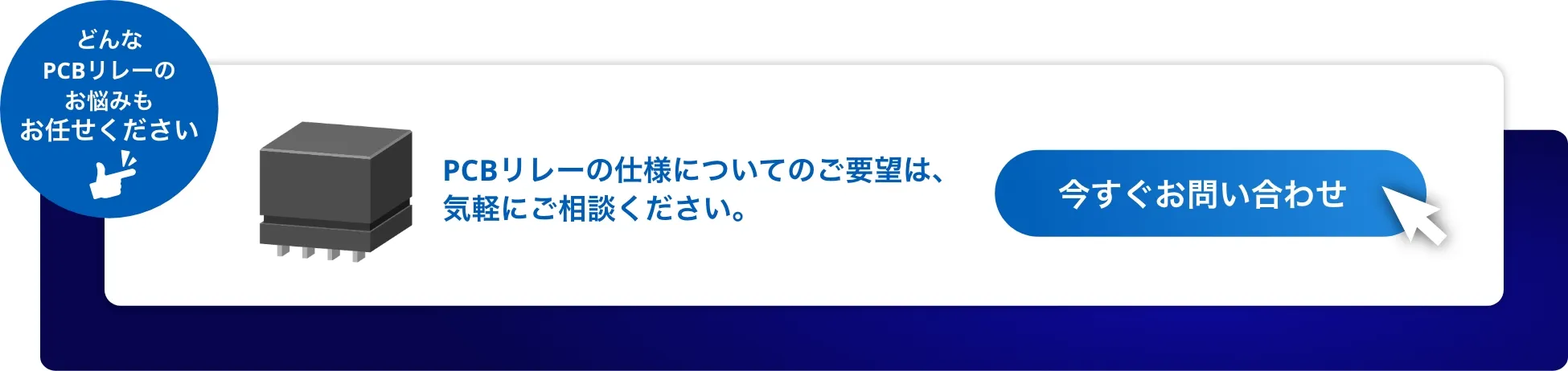
放熱構造の追加
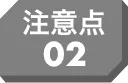
放熱構造の追加
小型化・高容量化の障壁は機器内の発熱です。例えば、PCBリレーの高容量化により、通電電流が2倍になると、発熱量は4倍になってしまいますが、あまりに高温になってしまうと基板が壊れてしまいます。そのため、200~300Aクラスの大電流を通電するPCBリレーでは、基板上にファンやヒートシンクなどの放熱構造が必要になるケースがあります。必要に応じて適切な冷却・放熱対策をご検討ください。
オムロンは、低接触抵抗な高容量PCBリレーもラインアップ(例:G9KA初期0.2mΩ以下)しており、機器内部の発熱低減と放熱機構削減による機器の小型化・薄型化に貢献しております。
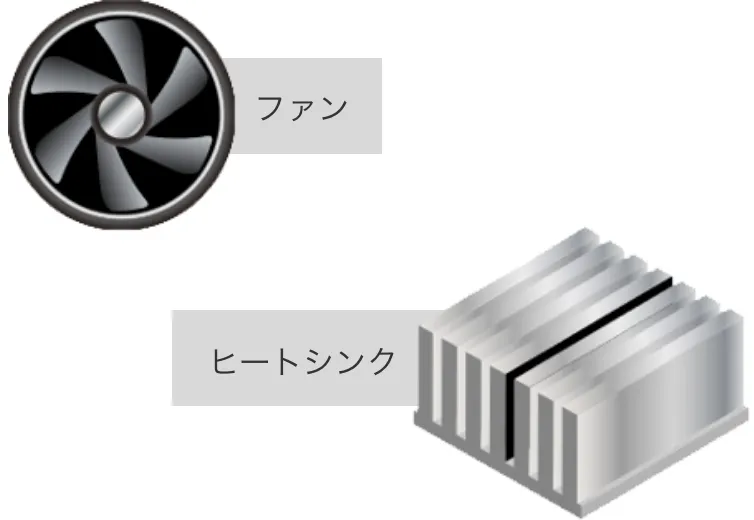
メンテナンス性
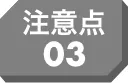
メンテナンス性
PCBリレーは基板上にはんだ付けで実装されるため、故障時にピンポイントでの部品交換が難しくなります。そのため、基板を丸ごと交換するケースが多いです。
基板を丸ごと交換と聞くと、故障部位のみを交換するよりも高コストになるイメージを持ってしまうかもしれません。しかし、基板全体を新しくするため、故障部位の特定のために作業者を現場に派遣する必要もなく、一度の交換で完結できます。交換作業にかかる時間の短縮が可能となり、結果、設備稼働時間の向上にもつながります。
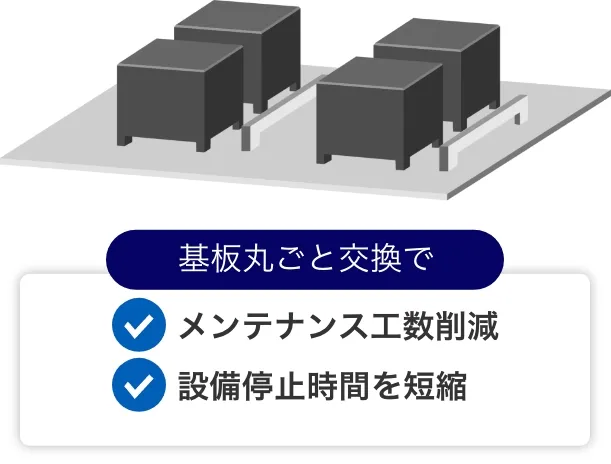
耐振動性
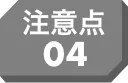
耐振動性
コンタクタは接圧を高める堅牢性の高い構造となっているため、振動に強いという特長があります。そのため、車載などのアプリケーションにおいてはコンタクタが採用されるケースが多く、その実績が評価され、振動性の高い他の用途でも活用されています。高容量PCBリレーも接点形状などの工夫により耐振動性を高くすることが可能です。ご要望などあれば、お気軽にご相談ください。
PCBリレーの実装基板を設計するためのポイントは?
「どんな部品が必要なのか?」「大電流を基板に通電しても大丈夫なのか?」など、基板化検討時のお困り事は多いのではないでしょうか。以下、設計時のヒントとしてご参照ください。
PCBリレーを活用した大電流制御システムに必要な周辺部品例
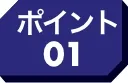
PCBリレーを活用した大電流制御システムに必要な周辺部品例
リレー基板モジュール(1a接点×2個直列で3組使用した場合)の必要部品例を紹介します。大電流を流せる厚銅基板などが必要となります。
部品名 | 員数(個) |
---|---|
リレー(1a) ※多極の場合は員数減 |
6 |
プリント基板(厚銅基板) | 1 |
バスバー | 6 |
端子台 | 6 |
ネジ | 4 |
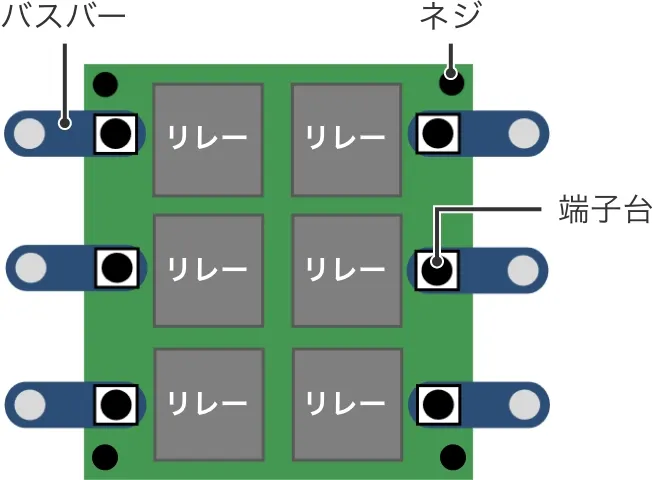
基板設計、実装条件
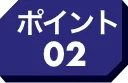
基板設計、実装条件
●発熱、放熱を考慮した基板設計条件
基板上で高密度実装に加え、大電流で通電したい場合は、部品配置や条件に合う基板の採用が重要です。一般的には、各リレーの定格電流に適した基板の厚みや銅箔断面積、
端子台のサイズ、主端子間の距離などを考慮して設計する必要があります。詳細の条件例は、右のリンクよりご参照ください。
●プリント基板用端子の実装条件
端子の温度上昇を抑え過熱しないように、高容量PCBリレーは表面積の大きな端子が必要となる場合があります。どのように基板にはんだ実装すればよいか、その考え方や推奨プロファイルを右のリンクよりご参照ください。
発熱対策
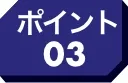
発熱対策
部品自体の発熱を抑制することで、ファンやヒートシンクなどの放熱機構を最小化させることも重要です。リレーは比較的発熱しやすい部品として見られることもありますが、接触抵抗値の低いリレーを選択することで発熱を抑制することが可能です。
当社のリレーは「低接触抵抗で低発熱である」ことを特長としています。コンタクタ同等の初期約0.2mΩ以下を実現しており、電気的耐久後0.3mΩ以下を維持できる実力を有する製品(形G9KA)も提供しています。従来の一般的な高容量リレーから当社リレーに置き換えることで、初期抵抗値を0.2mΩ軽減し、結果温度上昇値を約19.3℃低減(G9KA)、約67.7℃低減(G9KA-E)できたシミュレーション結果もございます。ご検討ください。(詳細はこちら)
保持電圧回路による低消費電力
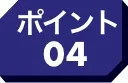
保持電圧回路による低消費電力
高容量PCBリレーは消費電力を最小限に抑えられるよう「保持電圧回路」や「PWM駆動回路」での制御を推奨しています。回路によっては理論上1/4に駆動電力を削減することも可能です。回路例は、右のリンクまたは各製品ページに掲載のホワイトペーパーをご参考ください。
オムロンの高容量メカニカルリレーラインアップ
オムロンの高容量PCBパワーリレーは、低電圧から高電圧まで幅広い用途に適した製品ラインアップを用意しております。お客様の設計に応じて、最適なリレーを選定ください。
選定にお困りの際はお気軽にご相談ください。
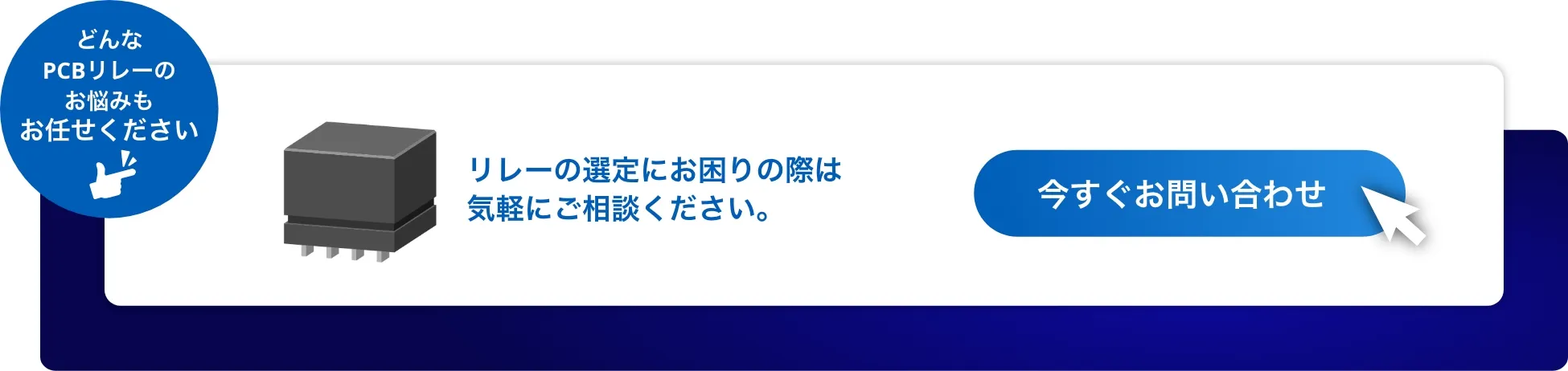
関連コンテンツ
高容量リレー 技術サポートページ
コイルの逆起電圧、保持電圧印加回路、大電流基板フローはんだの推奨条件、磁場の影響、直列・並列接続時の注意点など、大電流・高電圧のPCBパワーリレー使用時の「わからない」を詳しく解説した高容量リレーの技術サポートページです。
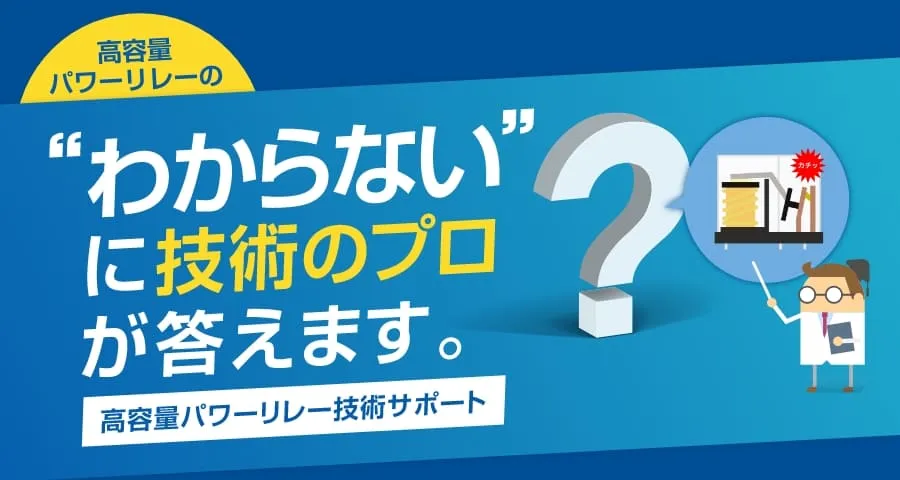
エネルギー市場向けソリューション
エネルギーの生成から利用までの関連機器に対し、オムロンがお客様に提供しているソリューションを、「業務用・産業用」と「家庭用」に分類し、ご紹介します。
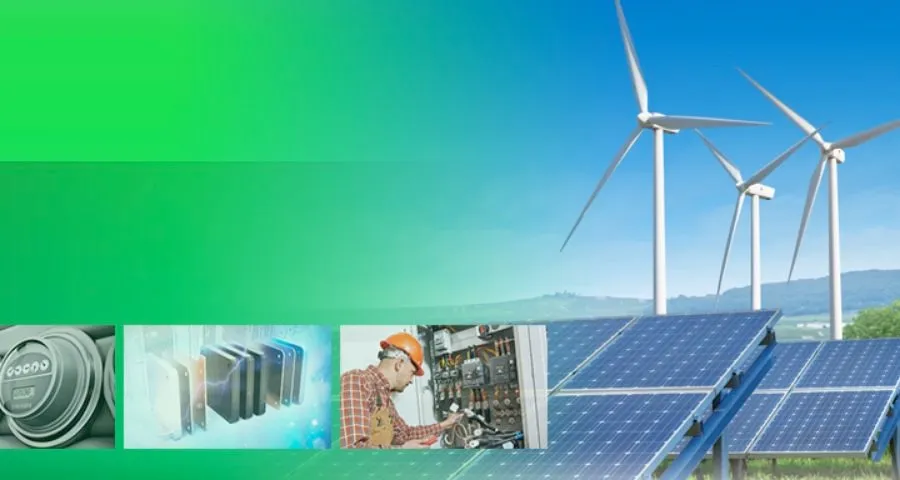