
Electronic devices such as MLCCs, crystal oscillators, and surface acoustic wave filters are very small, some about 1/10th the size of a grain of rice. When inspection pins were applied to these products, it was difficult to perform highly accurate continuity inspections because the tip of each testing pin was extremely thin, resulting in variations in measurement values. To make matters worse, the terminals of the device under test are often made of ceramic and are very hard, so the tips of the testing pins were scraped. This resulted in a short life span and increased maintenance frequency, thereby reducing production efficiency. There was also a problem that the broken pin could damage the device under test itself.
OMRON’s high hardness compatible sockets can be used safely for such extremely small package products.
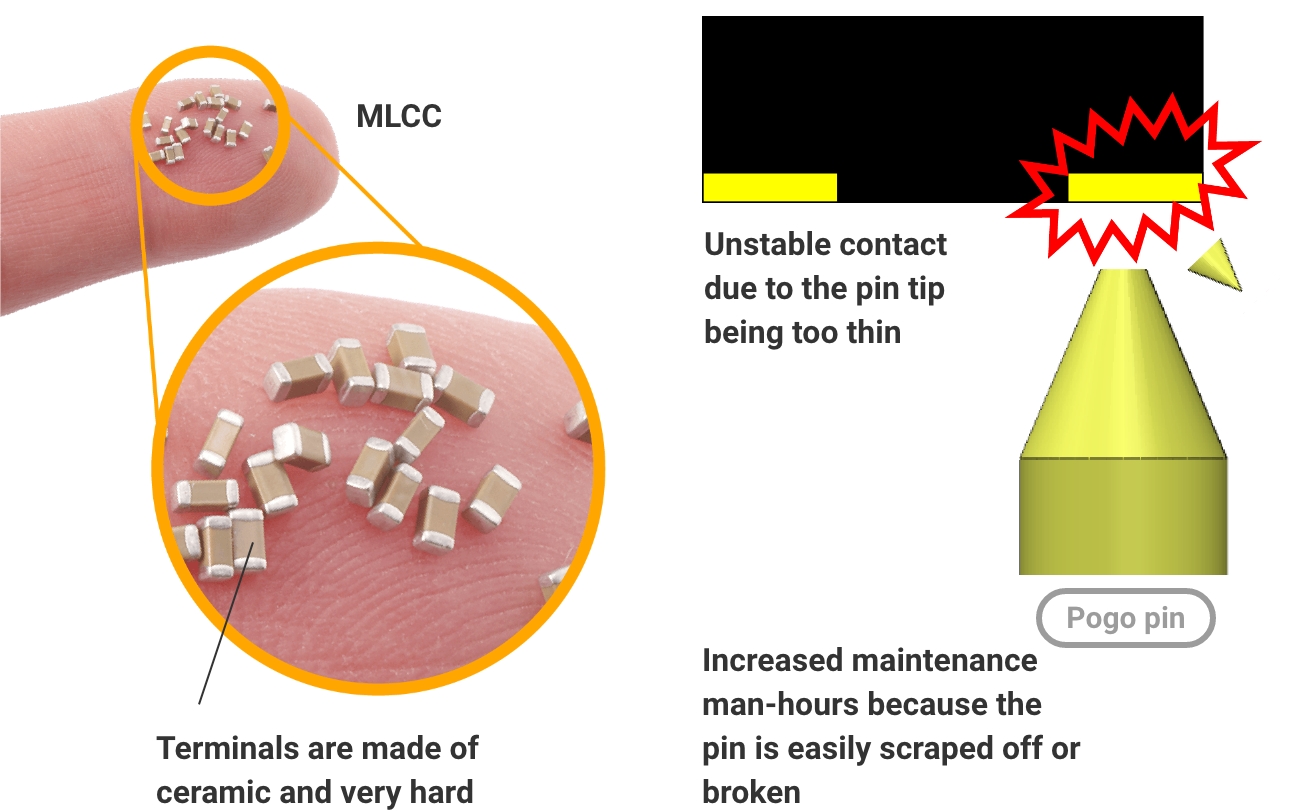
Item | Specification |
---|---|
Contact force | 20gf at 0.95mm |
Recommended stroke | 0.95mm (PCB side: 0.15mm, DUT side: 0.8mm) |
Maximum stroke | 1.35mm (PCB side: 0.15mm, DUT side: 1.2mm) |
Minimum stroke | 0.55mm (PCB side: 0.15mm, DUT side: 0.4mm) |
Contact resistance | 130mΩ |
Rated current | DC 1.0 A |
Plating | Au |
*Specifications are for reference only and may vary depending on the customized product.
We can custom design each pin and socket to suit the actual customer application. Please contact us for details.
Stable contact for accurate inspections
OMRON’s ultra-small package compatible sockets have a convex tip shape to ensure a sufficient contact area with the conduction pad. The strength of the EFC process technology is its ability to control the dimensional tolerances of this tip shape in micron order with extremely small pins and even in mass production.
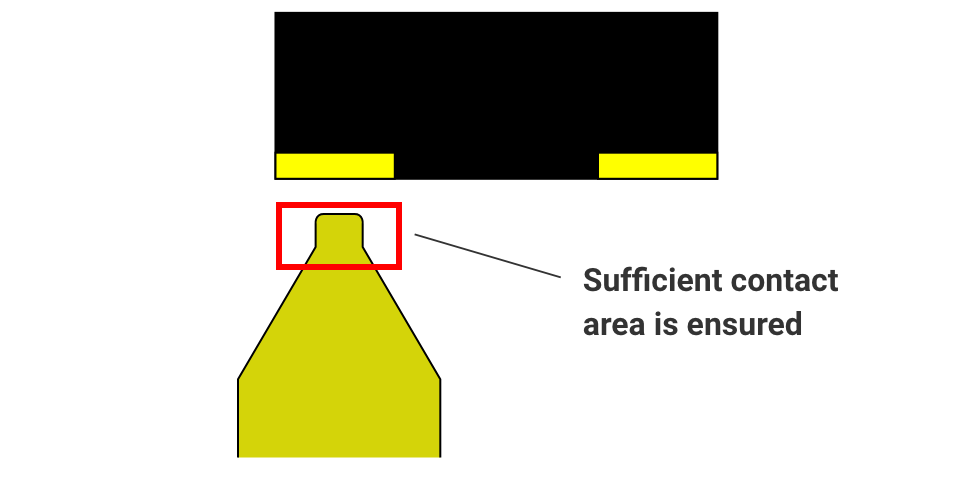
In addition, the material of the terminals (electrode pads) of small devices under test such as crystal oscillators is often ceramic, and the surface is uneven. Therefore, there are cases where it is difficult to accurately measure the movement of vertical pins such as pogo pins. However, due to the movement of the spring that is unique to the EFC process technology, OMRON’s blade pins make contact in such a way that the pin rubs the terminal surface rather than making contact in a vertical direction. This makes it possible to offer products with reliable contact and stable measurement accuracy.

Omron’s probe pin (blade pin) movement for reliable contact
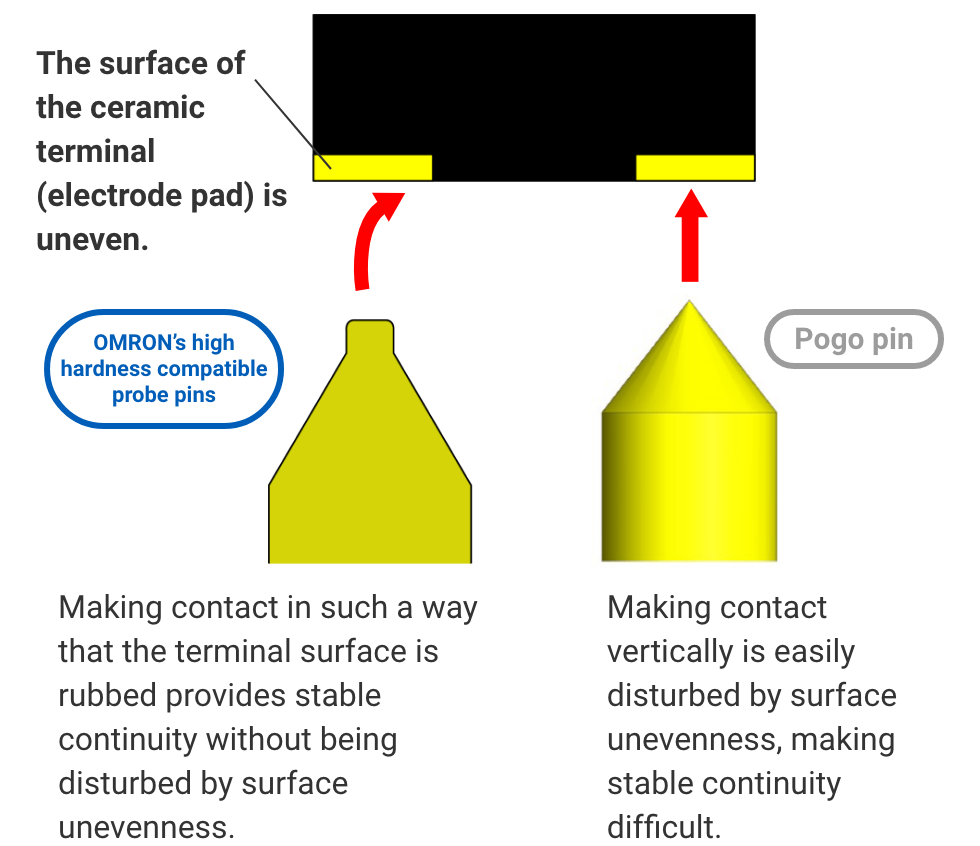
Long operating life and reduced maintenance
The convex tip shape greatly reduces damage to the pin tip. OMRON’s blade pins reduce maintenance man-hours in the mass production process and contribute to increased production efficiency.
Furthermore, the blade pins greatly reduce the risk of damaging the customer’s product due to breakage of the tip, enabling stress-free inspections.
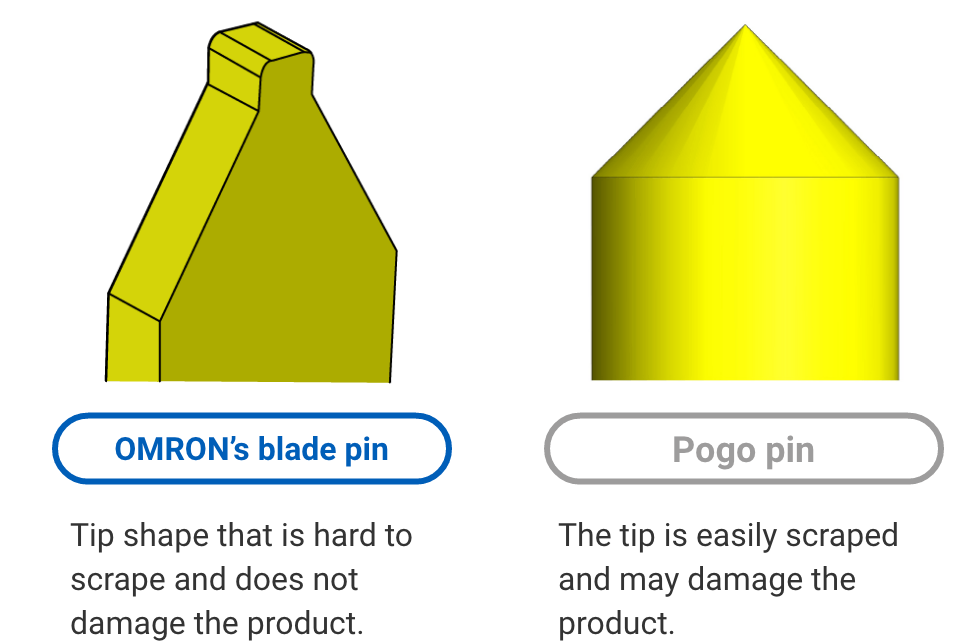
Custom design recommendations that best suit the customer’s application and OMRON’s original material blend* make our sockets more than five times more durable than pogo-pin sockets. This greatly reduces the frequency of testing socket replacement at the inspection site, contributing to improved production efficiency.
*Patent No. 5077479
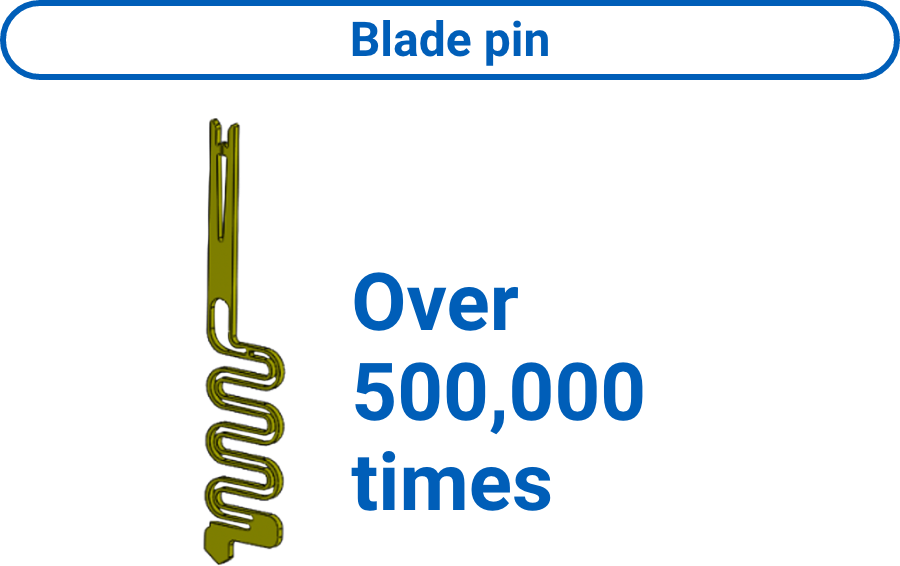
*An example of B-to-B connector inspection
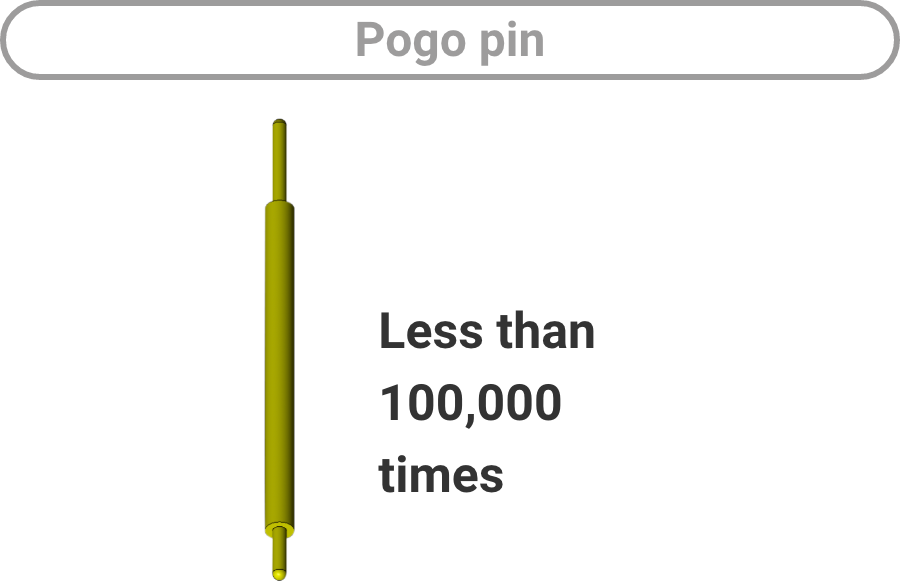
