Automotive ECUs (Electronic Control Units) play a very important role in controlling various devices and complex systems built into automobiles. Each ECU is extremely complex and directly linked to vehicle safety, requiring many inspections, but posing challenges in terms of inspectability.
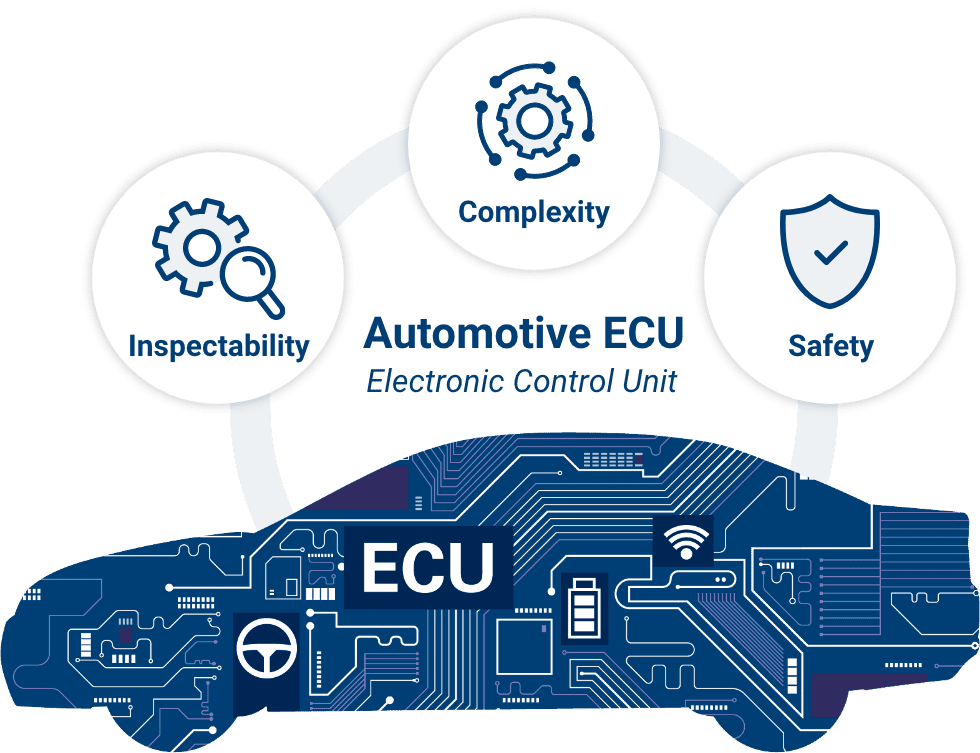
Conventionally, ECUs have been inspected for continuity by applying inspection probe pins directly to dummy patterns on the PCB. However, changes in standards have increased the difficulty of inspecting ECUs with high-speed transmission, requiring even stricter and more precise inspections. As a result, there is a growing need for inspection at the component level, including multipole connectors connected to the PCB, rather than conventional PCB-level inspections that rely on dummy patterns.
On the other hand, as ECUs become more sophisticated, the connector side to be inspected is also required to have advanced features such as multipole terminals, narrow pitch, and high-frequency characteristics.
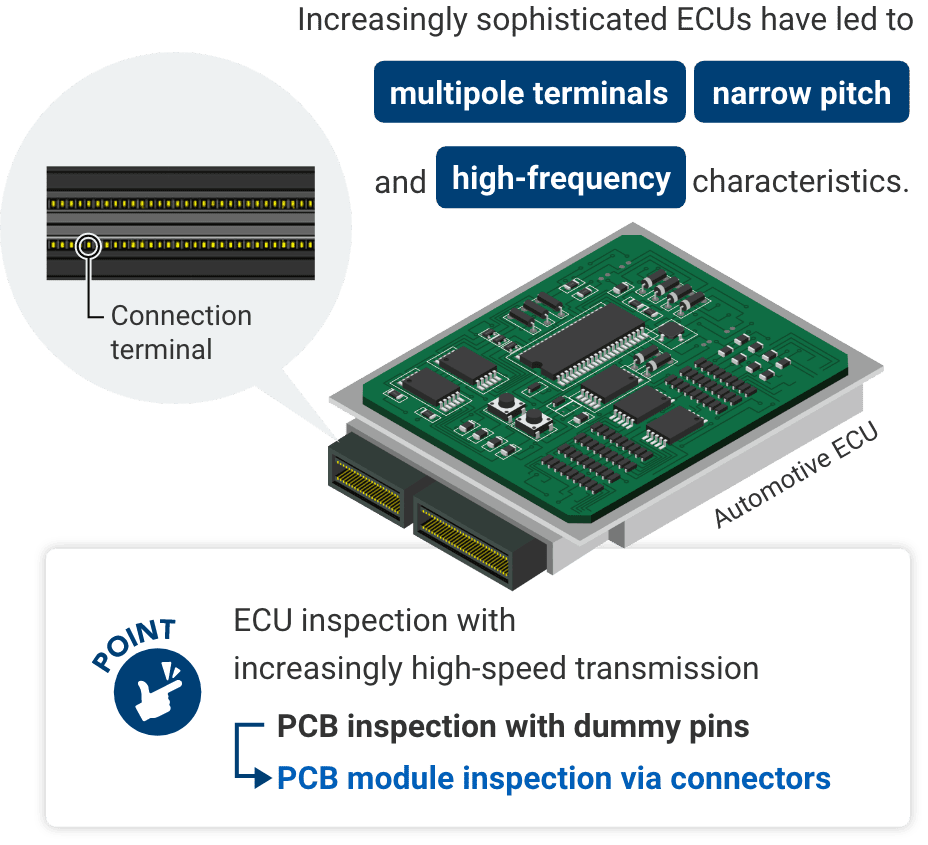
Connectors for ECUs are designed with vibration resistance in mind for automotive applications.
Therefore, the connection terminals are arranged on the sides to prevent connection failures due to vibration. The height is high enough to prevent disconnection in the event of vibration or shock, and as a result, the connection terminals are located in a secluded place.
Because of this special structure, problems such as the difficulty of applying pins to side connection terminals with rod-shaped inspection pins like pogo pins and the inability to prepare inspection sockets that can maintain stable contact reliability with multipole connection terminals arranged in a secluded place have become apparent.
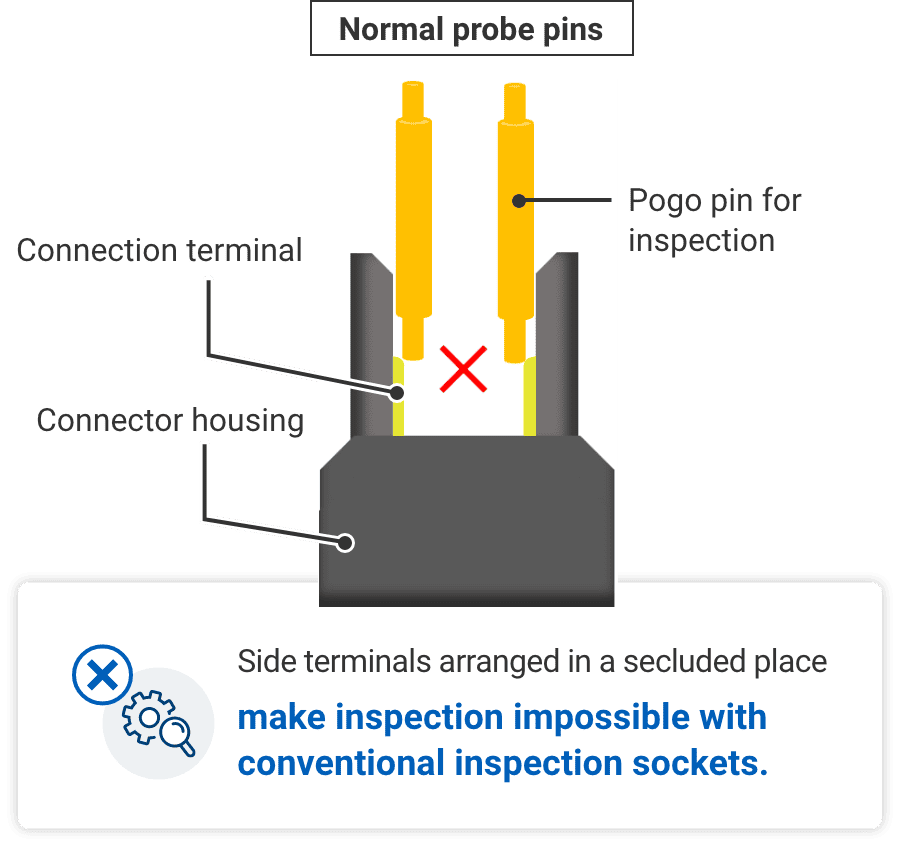
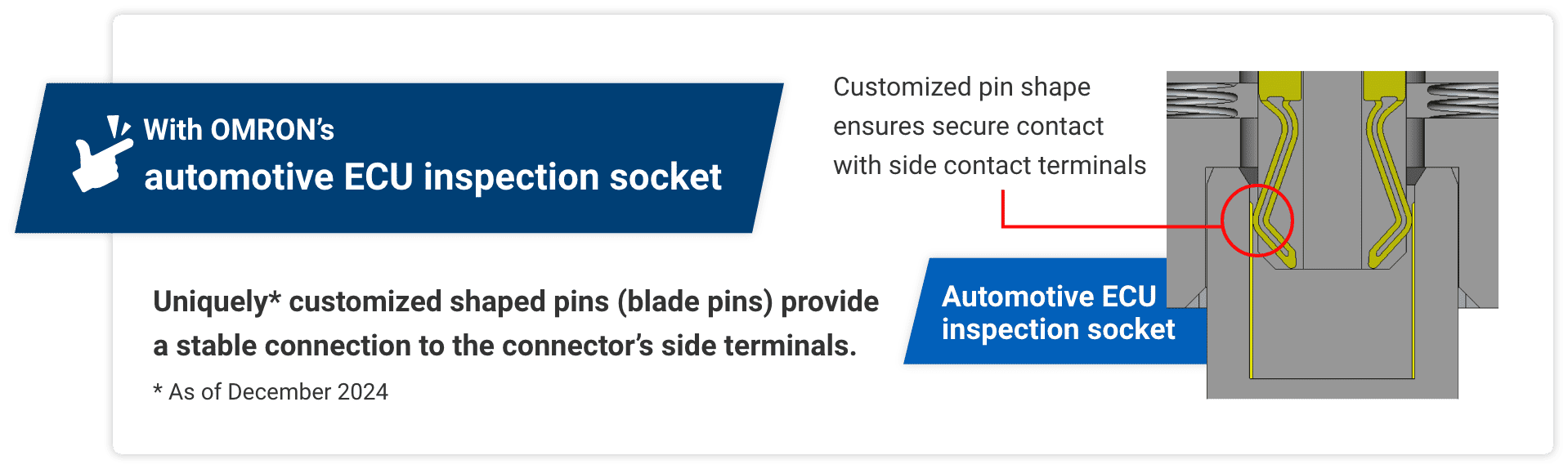
In addition to the above, the inspection of highly functional ECUs requires various additional factors, including:
High durability on the socket side to meet inspection efficiency
Narrow pitch to accommodate multipole terminals with the same connector size as before
High-frequency characteristics to meet the demand for high-speed transmission
Large current compatibility
OMRON’s inspection socket can meet all of these needs for automotive ECUs.
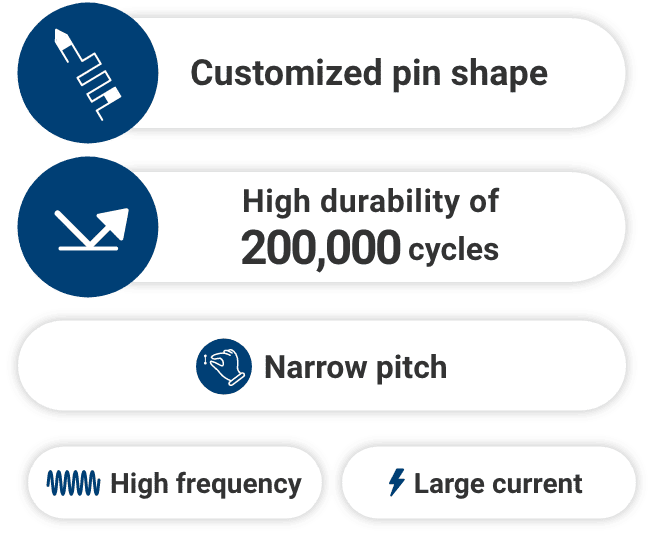

Product information
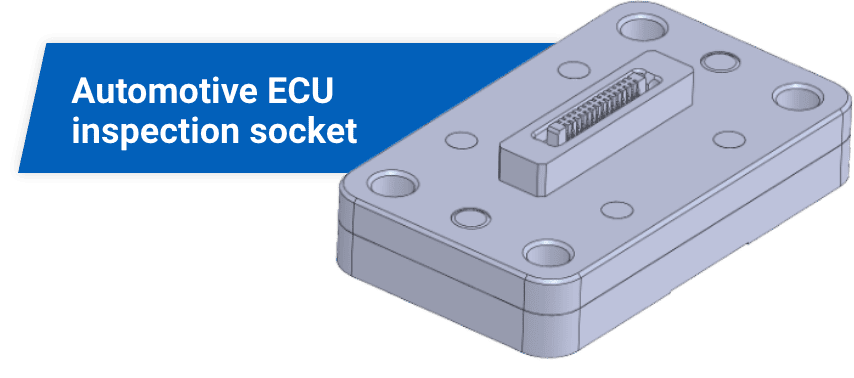
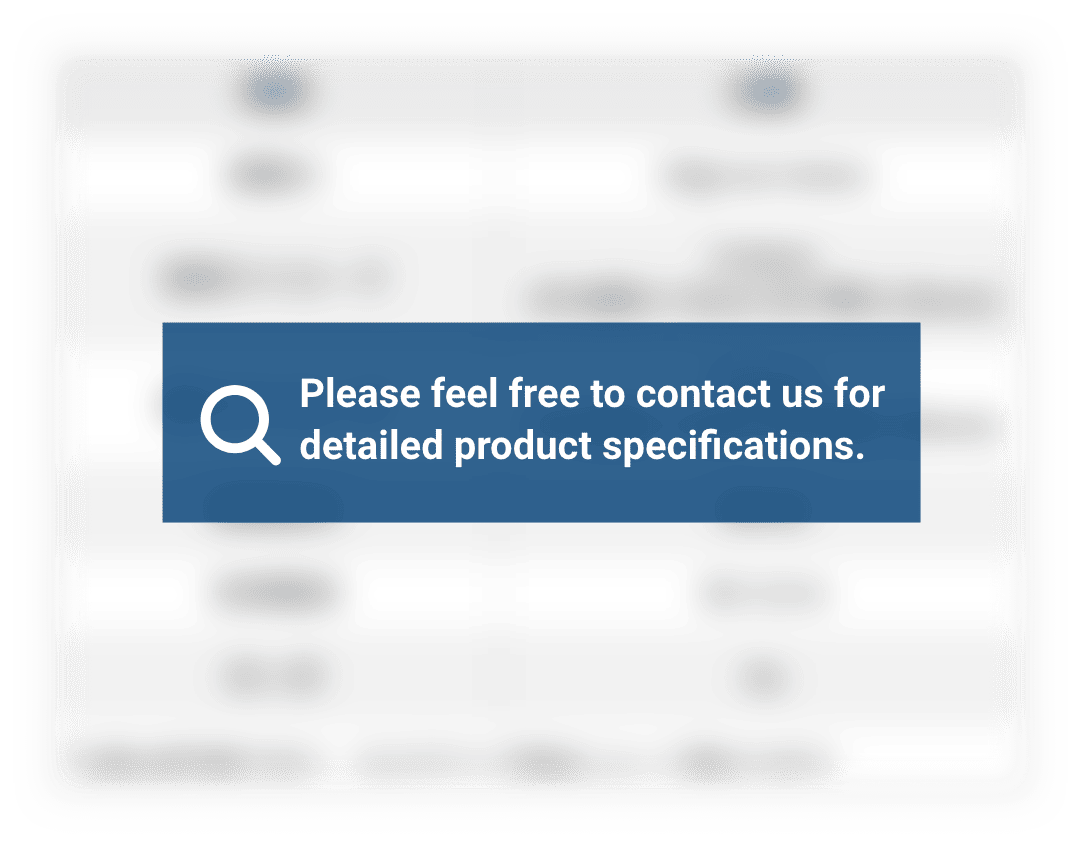
In the inspection of automotive ECUs, the connection terminals of the connector on the inspection side are arranged on the secluded side, making it difficult to connect with ordinary inspection sockets.
OMRON's EFC process technology is unique in its ability to realize complex pin shapes with a single component configuration. We propose a custom designed pin shape that enables a stable approach to the connection terminals arranged on the side.
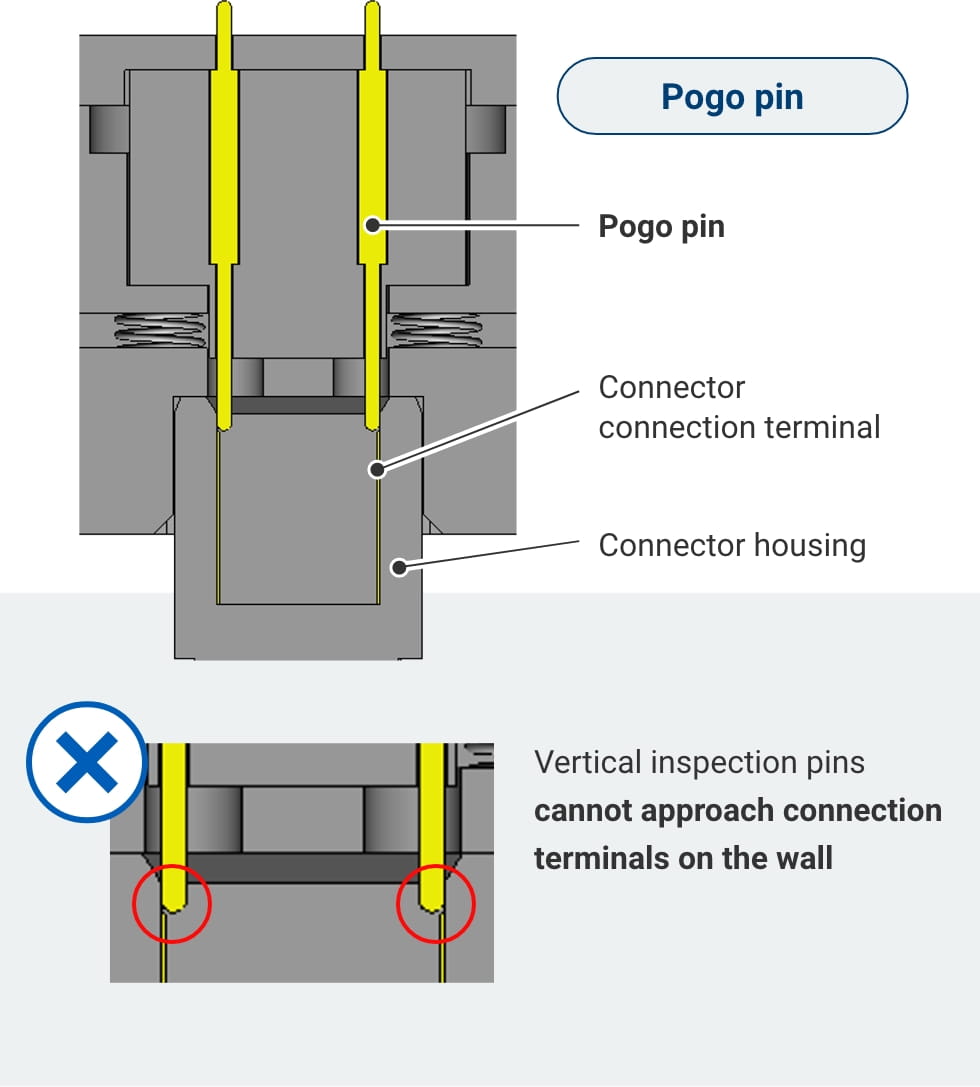
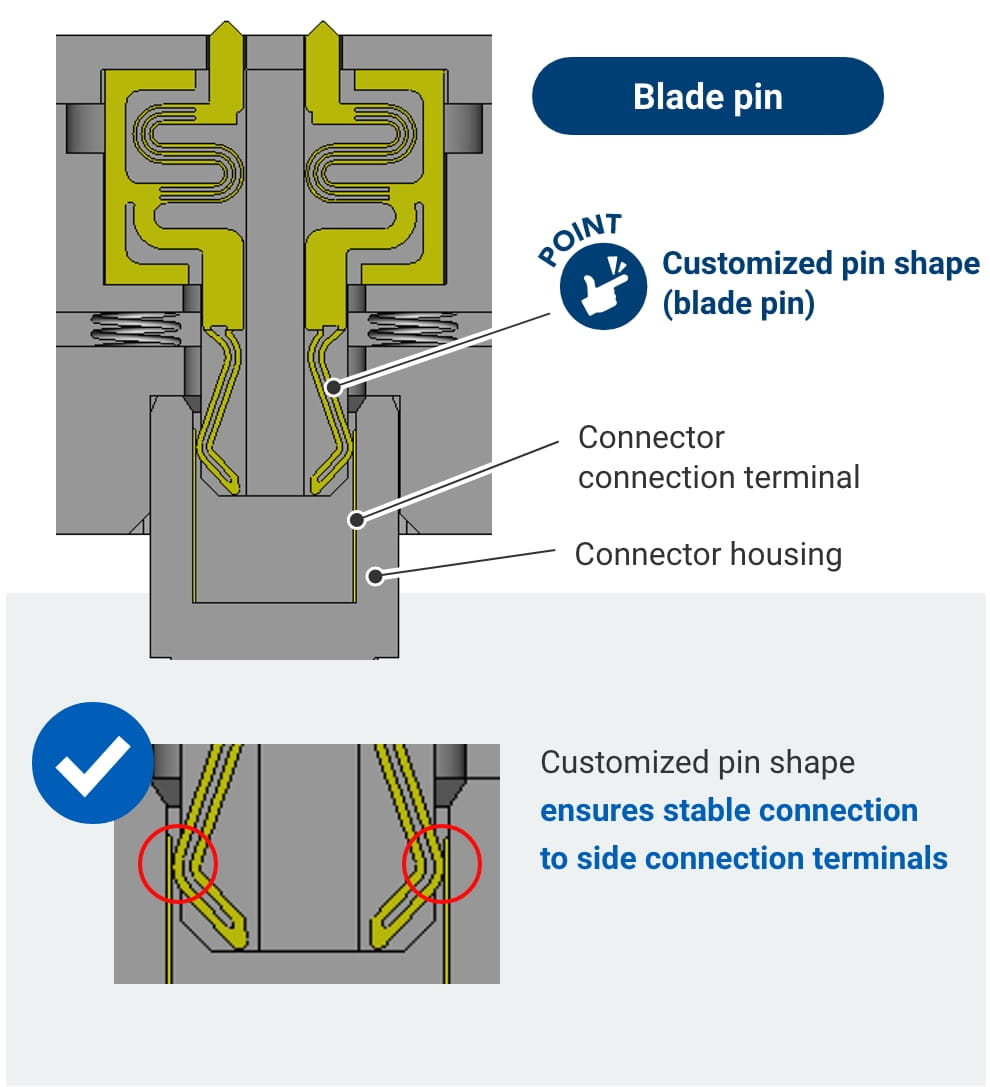
As mentioned above, it is difficult to perform continuity testing using an inspection socket for automotive ECUs. Therefore, it is common to perform continuity testing by mating a commercially available connector to the connector section.
However, commercially available connectors are not designed for testing and can quickly fail after dozens of consecutive insertion-extraction cycles. An automobile is equipped with approximately 100 or more ECUs. Therefore, in order to inspect them, the man-hours and costs involved in replacing the connectors used for the inspection would be enormous.
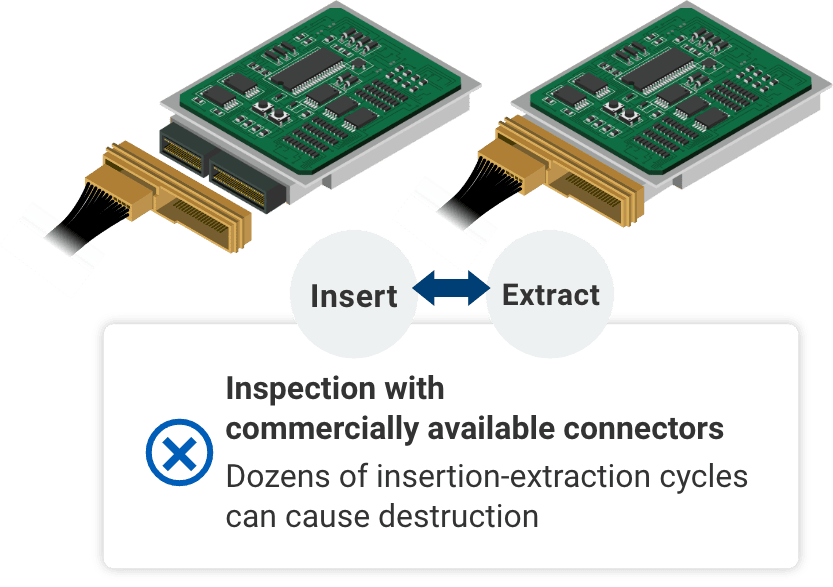
OMRON’s inspection socket, available in various customized configurations for use in the inspection of automotive ECUs, provides high durability of more than 200,000 cycles. By proposing custom designs best suited to your application and by using OMRON’s original material blend*1, we have achieved more than twice the high durability*2 compared to pogo-pin sockets. The socket greatly reduces the frequency of inspection socket replacement at inspection sites where connector inspection of automotive ECUs is difficult, thereby contributing to improved production efficiency.
*1 Patented
*2 An example of B-to-B connector inspection
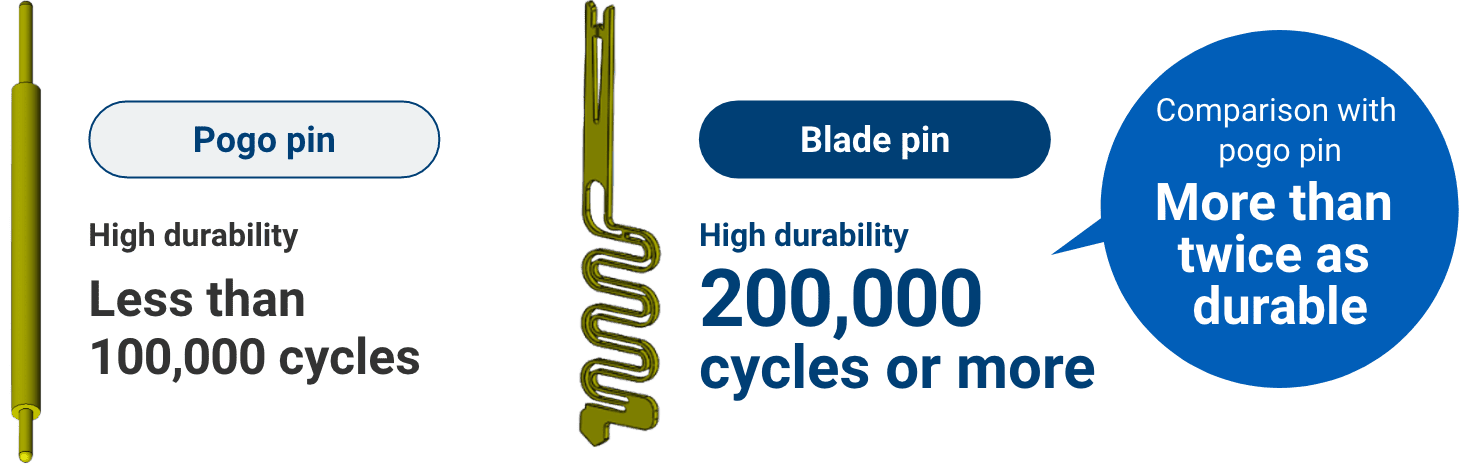
In addition, OMRON’s customized inspection socket can add various other performance features such as narrow pitch, high frequency, and large current, depending on your application.
Click on the link below for more information.