Table of Contents
- Difference between contactors and relays
- What is DC power relay?
- What is the DC power relay that is compact in size and achieves large current interruption in the contactor area?
- Gasless structure relay size for stable supply, realizing large current 500 A interruption equivalent to the contactor’s area
- Overwhelmingly compact compared to contactors with a 500 A-class interrupting capacity
- Excellent short-circuit performance capable of withstanding large currents of up to 5,000 A
- Ultra vibration & impact resistance to withstand severe impact like a car collision
- [Interview with developers] 500 A cutoff wall that could not be overcome only with conventional know-how relying on the power of gas
- [Interview with developers] OMRON's unique new DC power relay structure
- [Interview with developers] Ideal design vs. Mass-producible structure
- [Interview with developers] Electronic components can help address social issues
Environmental considerations such as decarbonization and soaring energy costs are accelerating the global shift from fossil fuels to renewable energy. Power generation using renewable energies such as solar and wind power is unstable because it depends on weather conditions. Batteries (energy storage) are essential to effectively use renewable energy. DC-driven (battery-driven) transportation means and transportation equipment using renewable energy are expected to be developed to supply electricity not only to homes and buildings, but also to the mobility sector represented by vehicles that use gasoline or diesel fuel. In order to meet the need to store and use a lot of electricity, DC power relays are required to have even higher capacity. Furthermore, as devices continue to incorporate more and more functions, the need for high density in a limited space is becoming increasingly important, and space efficiency is also an important consideration.
Difference between contactors and relays
Contactors are used in applications that require large currents of over 100 A to be carried. Both relays and contactors are used to switch various parts of a circuit. The main difference is that contactors are used with large currents, while relays are used with small currents. However, contactors used with large currents are more robust and larger than relays and tend to make a loud operating noise when opening and closing.
OMRON's DC power relays combine the advantages of both contactors and relays.
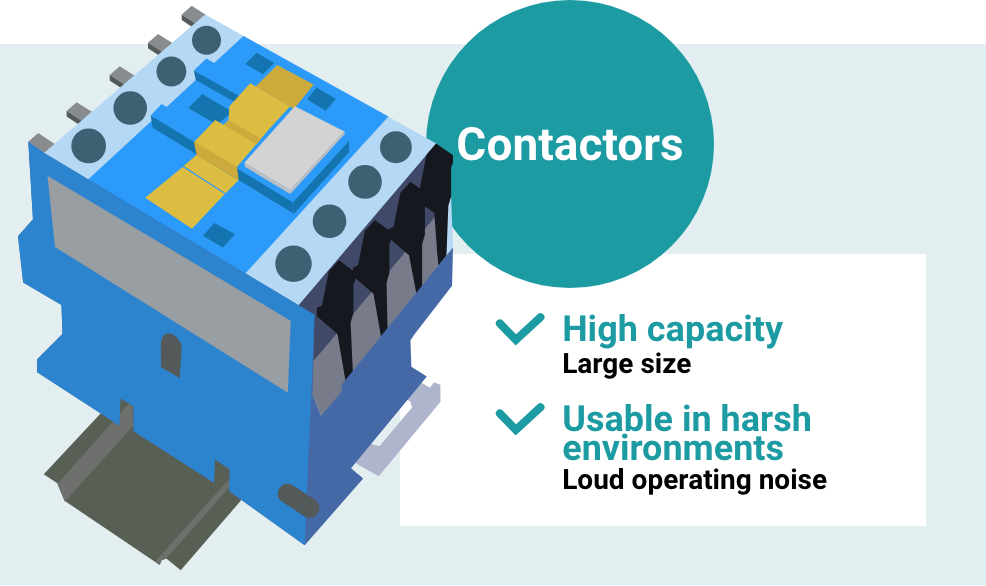
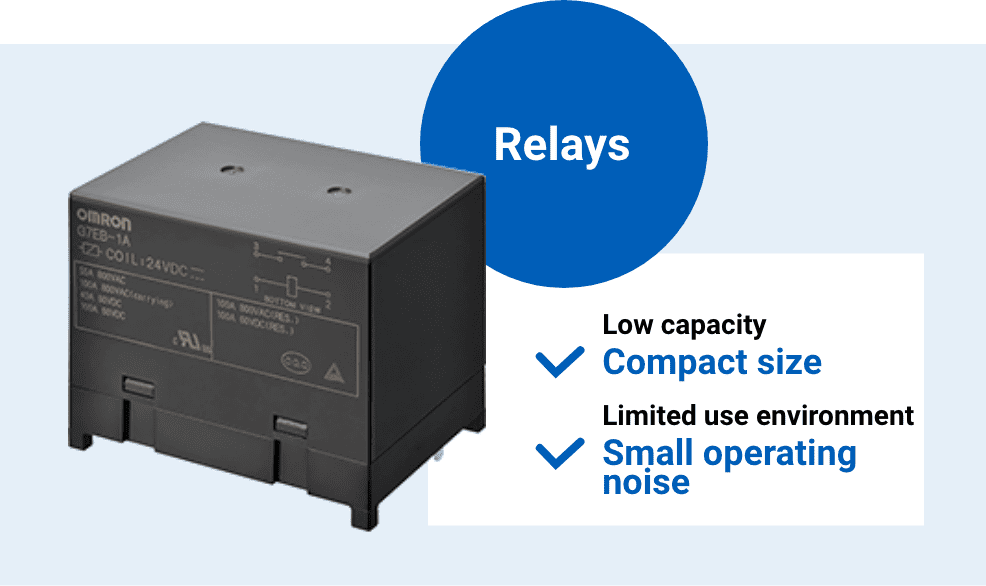
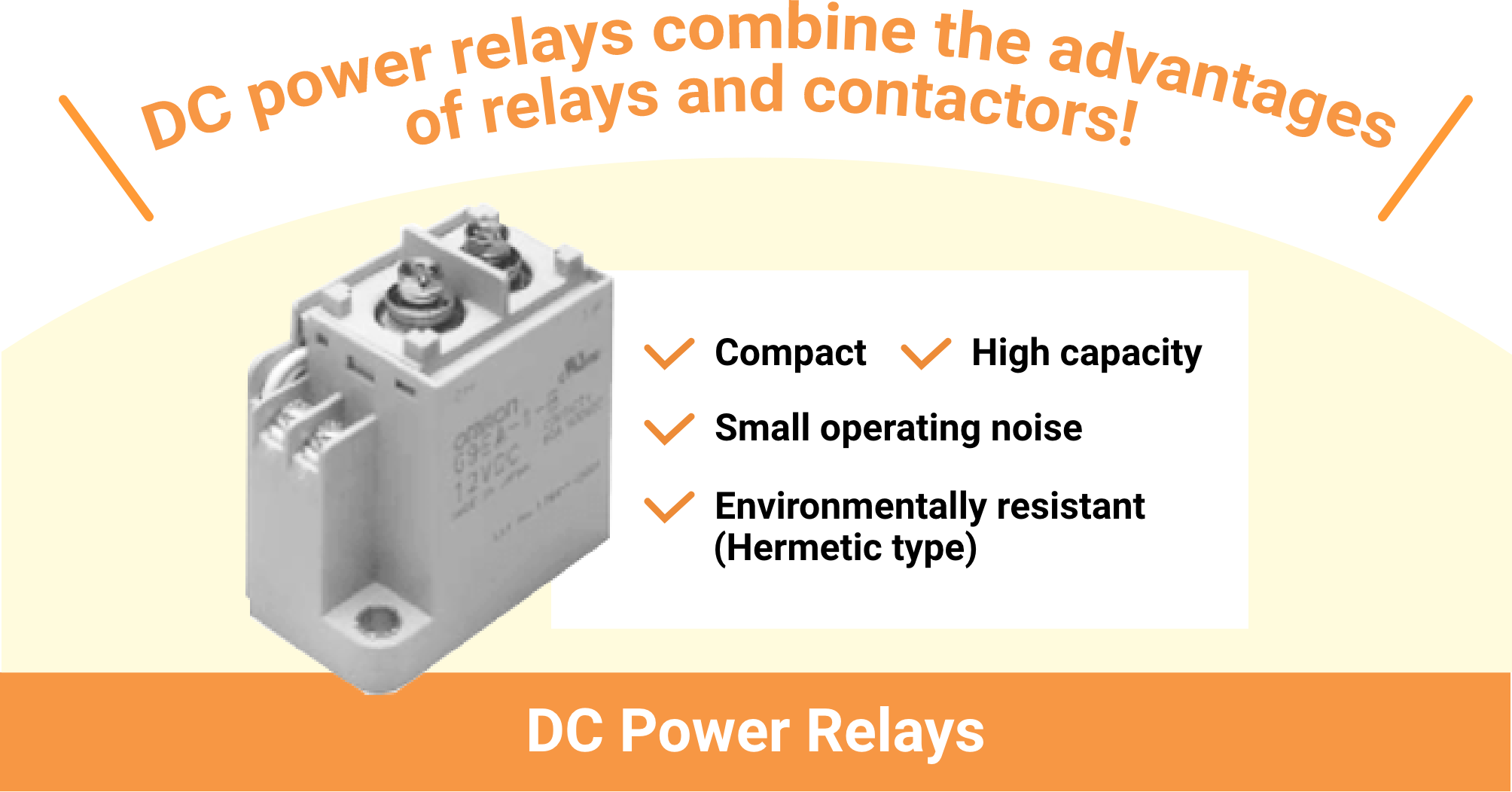
What is DC power relay?
While maintaining the compact size that is one of the advantages of relays, our DC power relays are capable of high-capacity energization and interruption which is in the switching area of contactors. Furthermore, hermetic type (gas-sealed type) relays have a robust sealed structure and have better environmental resistance to gases and dust than general relays. Hermetic type relays also suppress operating noise by downsizing the electromagnetic (drive part).
OMRON offers a lineup of DC power relays in a wide range of capacitance bands to meet your needs. We solve your problems with our DC power relays that combine the advantages of contactors and relays.
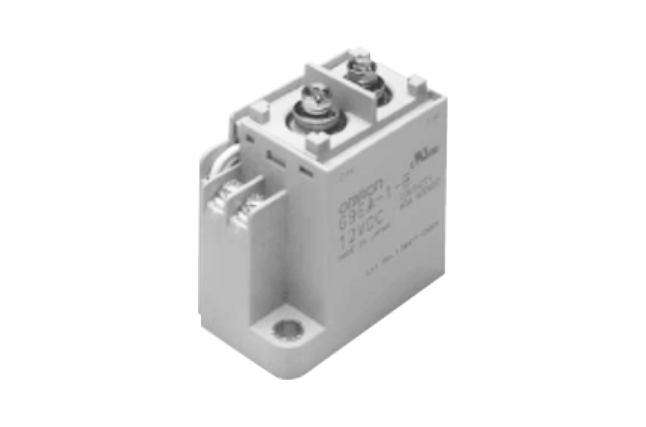
OMRON's power relay lineup

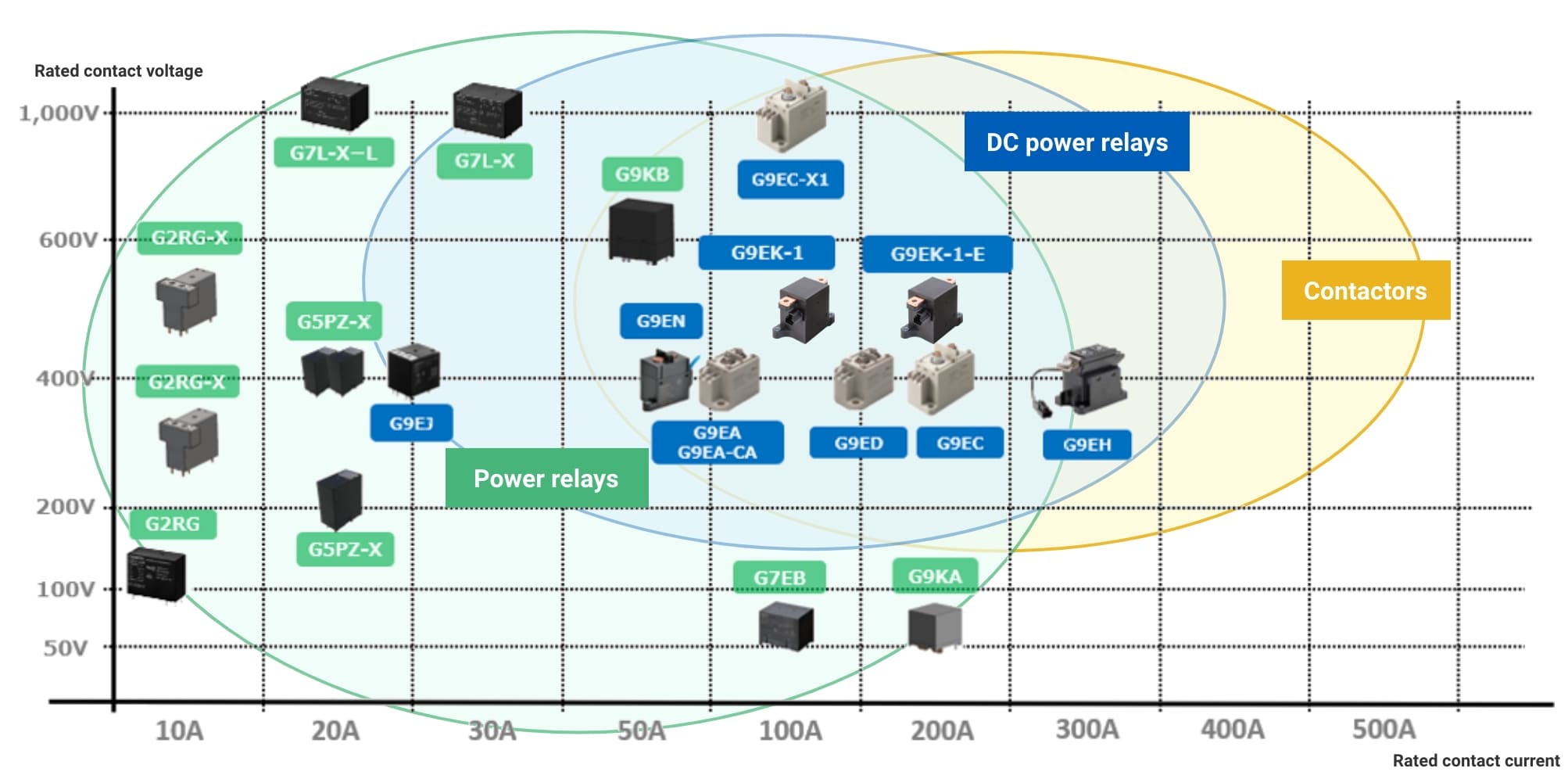
What is the DC power relay that is compact in size and achieves large current interruption in the contactor area?
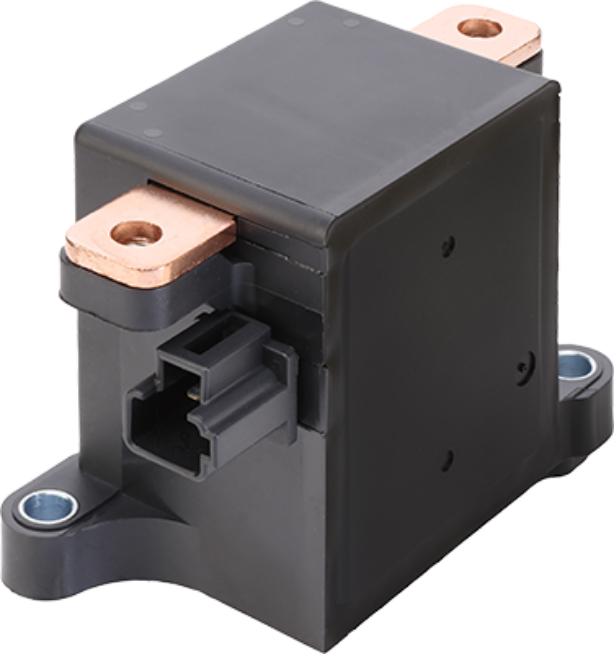
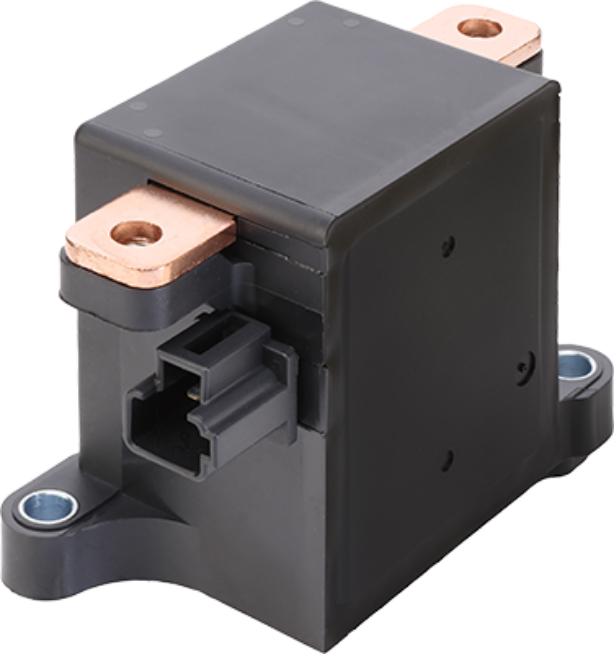
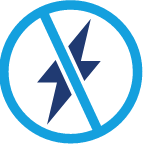
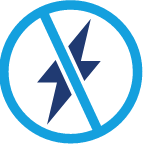
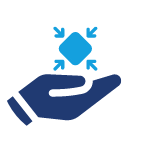
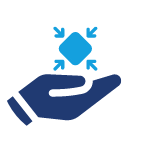
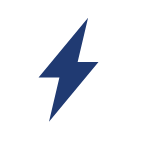
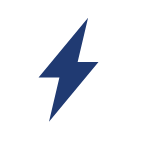
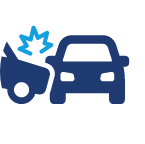
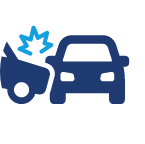
Expanding applications with G9EK

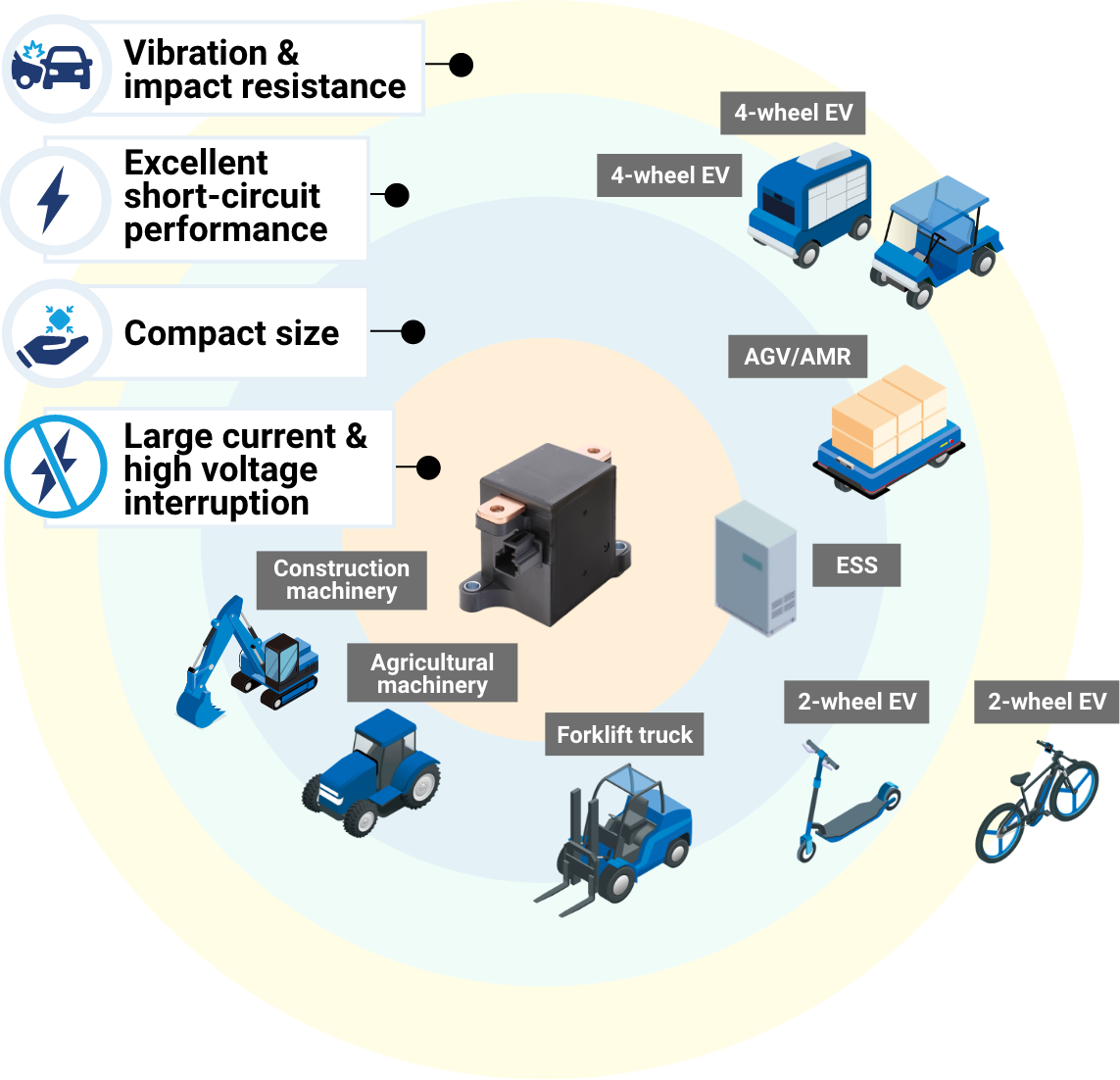
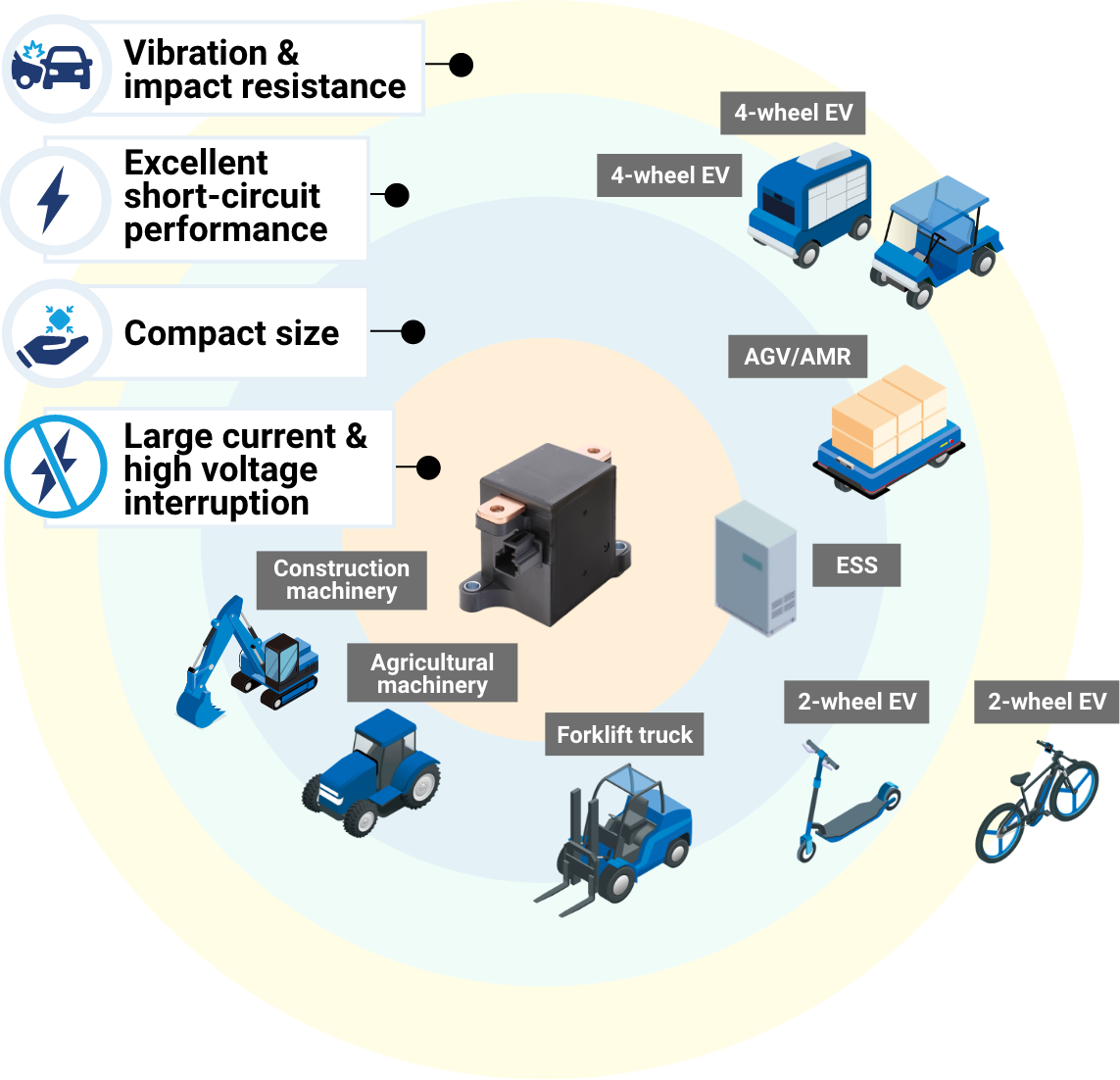
Please try the compact and high-performance G9EK! Click here for the G9EK product page
For automotive applications, please refer to webpages for In-vehicle Relays and In-vehicle Switches.
The G9EK is ideal for high-voltage and large-current interruption in these application circuits.
Large current 500 A interruption

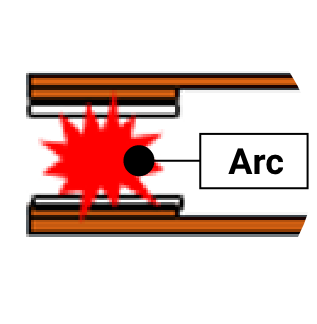
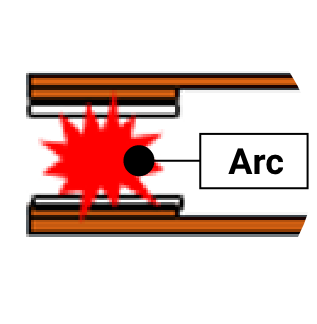
What is Arc?
An arc is a spark of several thousand degrees Celsius that is generated between the contacts of a relay when it turns off the circuit.
Conventional relay structure
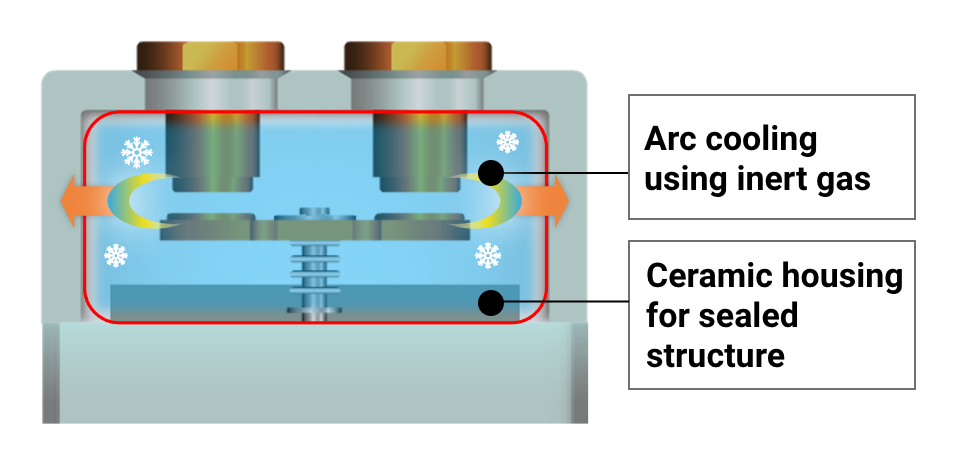
Arc cooling using inert gas
Pressurized gas with high thermal conductivity is filled in the contact area. The gas removes the heat from the arc, allowing for quick cooling and cutoff.
Ceramic housing for sealed structure
The need for a long-lasting gas leak-proof and deterioration-resistant structure covered with ceramics makes it visually robust and large in size. Relays tend to be expensive because they require special parts and manufacturing processes to prevent gas leakage, as well as special inspections to ensure hermetic sealing.
Up to 200 A can be carried by changing the cable
Up to 200 A can be carried
by changing the cable

by changing the cable
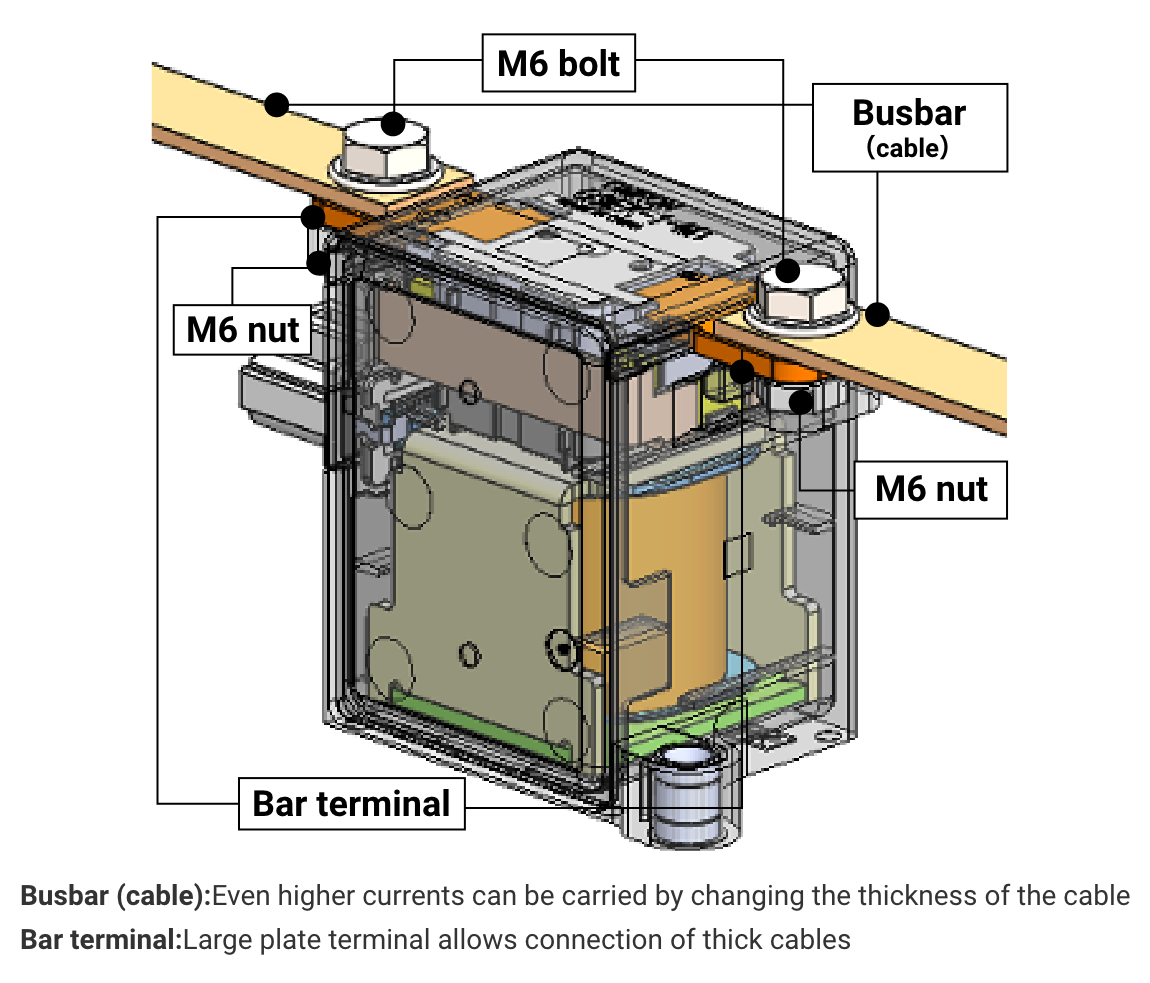
The G9EK is gasless and capable of high-capacity switching at a rated load of 500 VDC and 120 A. In order to stably energize the system with large currents of 100A or more, the terminal of the G9EK has a wide plate shape (bar terminal). By making the busbar (connector cable) thicker, heat dissipation is improved and even larger currents than the rated value of 120 A can be carried through it.
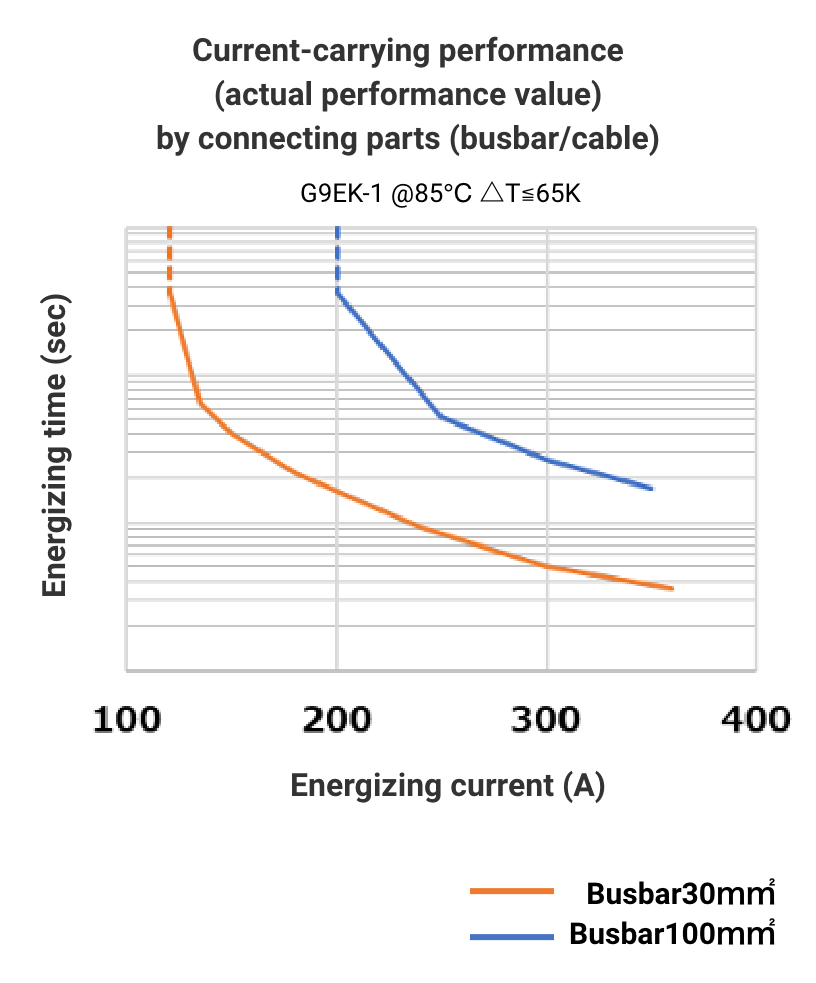
When a busbar with a thickness of 30 mm2 is used, 120 A can be energized, but when a busbar with a thickness of 100 mm2 is used, up to 200 A can be energized. (Actual values)
2-unit series connection capable of interrupting high voltages of 500 V or more
2-unit series connection capable of interr-
upting high voltages of 500 V or more

upting high voltages of 500 V or more
When connecting one G9EK
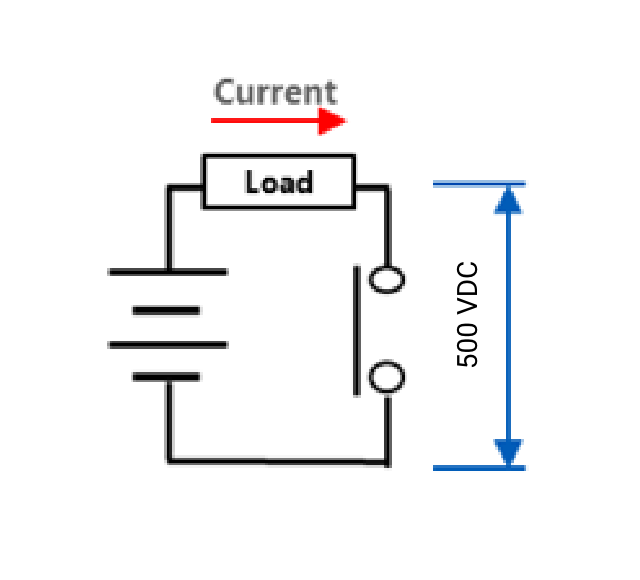
500 VDC interruption is possible
When connecting two G9EKs in series

One relay can interrupt 400 VDC, so two units can interrupt a total of 800 VDC. Using two units allows for greater resistance to short-circuit currents.
2-unit parallel connection capable of interrupting large currents of 1,000 A
2-unit parallel connection capable of
interrupting large currents of 1,000 A

interrupting large currents of 1,000 A
Two G9EKs connected in parallel can interrupt large currents of 500 A or more that cannot be interrupted by a single relay.
When connecting one G9EK
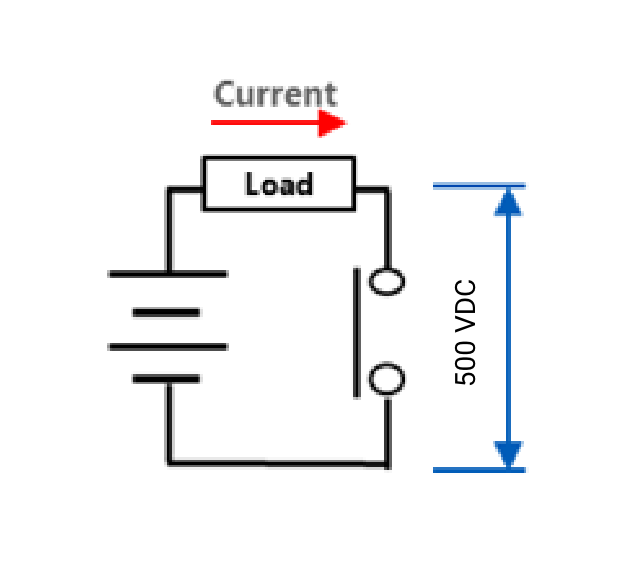
500 VDC interruption is possible
When connecting two G9EKs in series
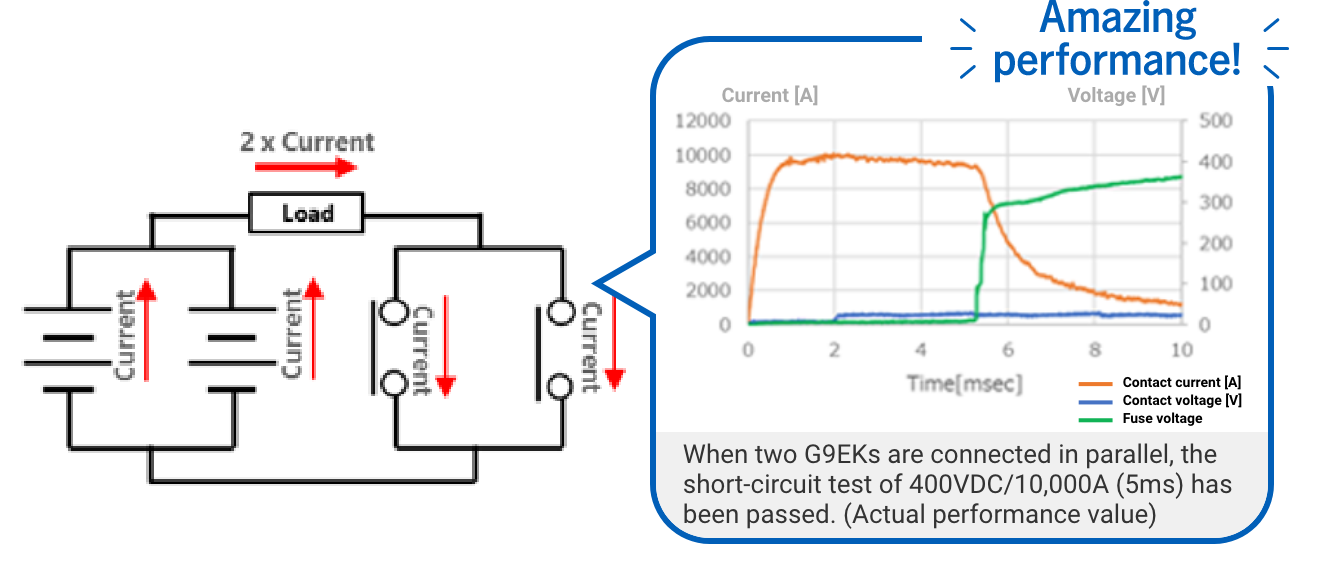
One relay can interrupt 500 A, so two units can interrupt a total of 1,000 A. Using two units allows for greater resistance to short-circuit currents.
However, contactors are air switching (gasless) types that do not have a special structure to interrupt arcs, such as gas-sealed relays. Therefore, the problem was that the contactors were inevitably large in size.
The G9EK achieves large-current switching of 500 A while maintaining its compact size. It is 80% smaller than contactors in the same capacity range, contributing to the downsizing of your applications.
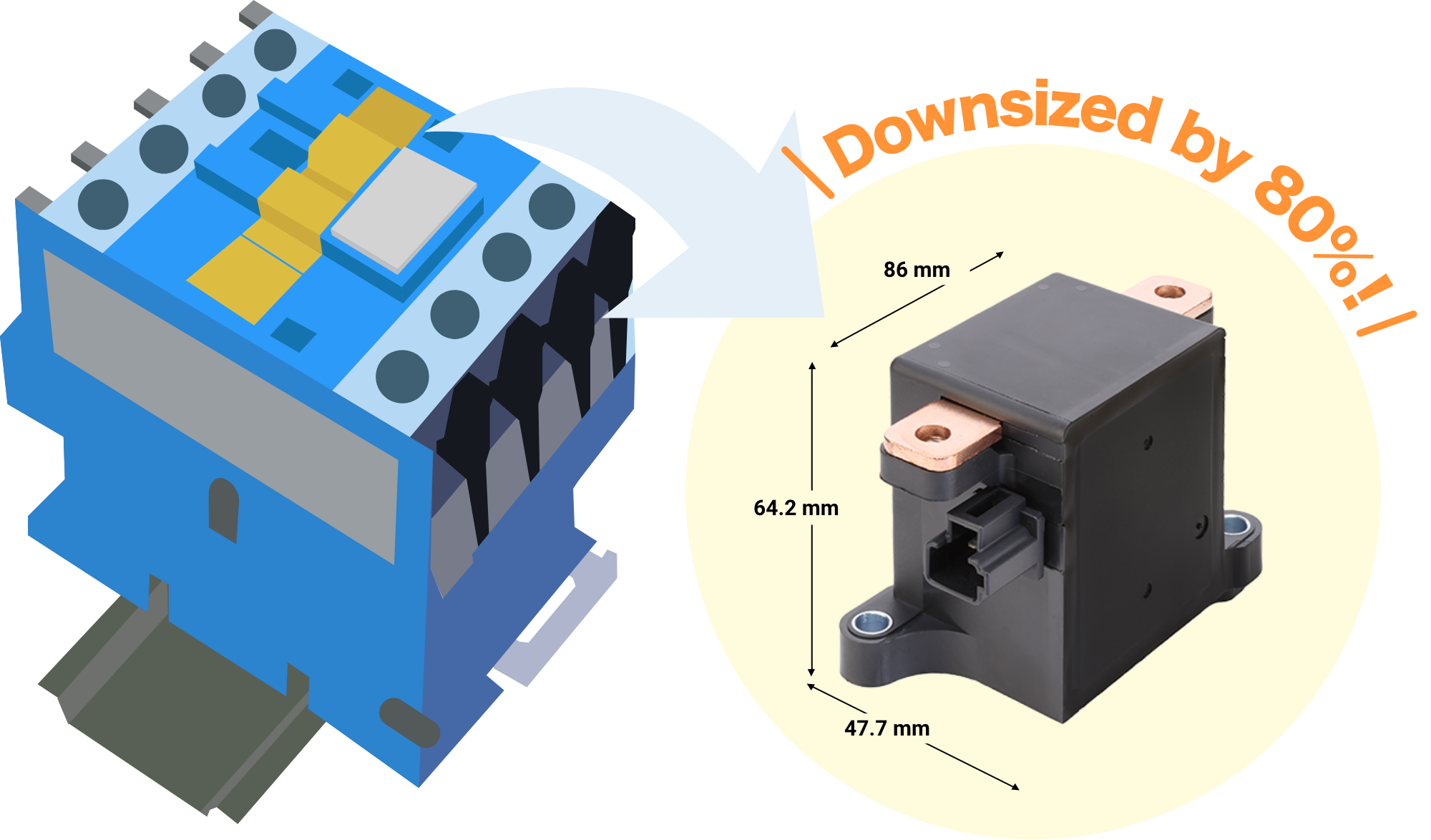
Supporting both charging and discharging helps reduce the size of equipment
Supporting both charging and discharging
helps reduce the size of equipment

helps reduce the size of equipment
Relays with polarity (for unidirectional switching)
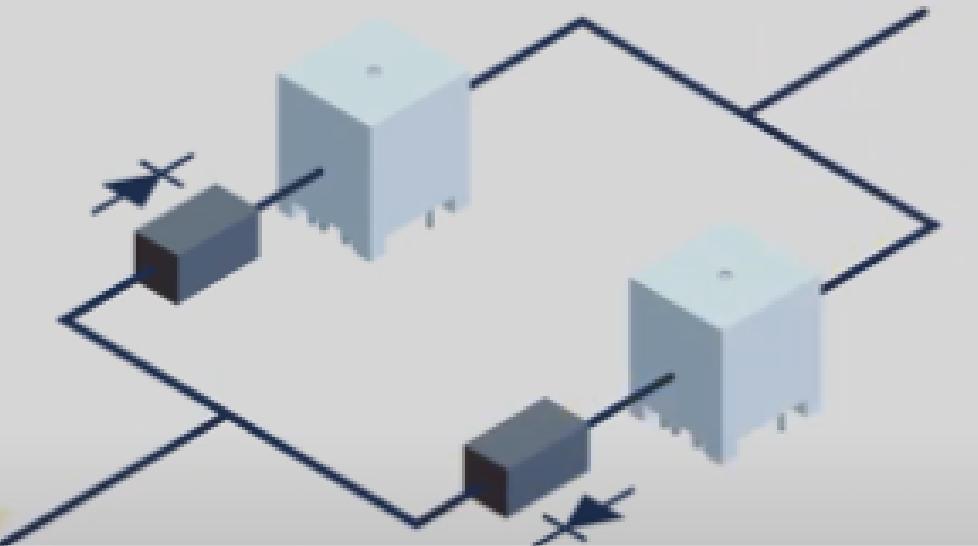
For non-polarized relays, the charge/discharge system requires two relays and two diodes connected in parallel.
Relays without polarity (for bidirectional switching)
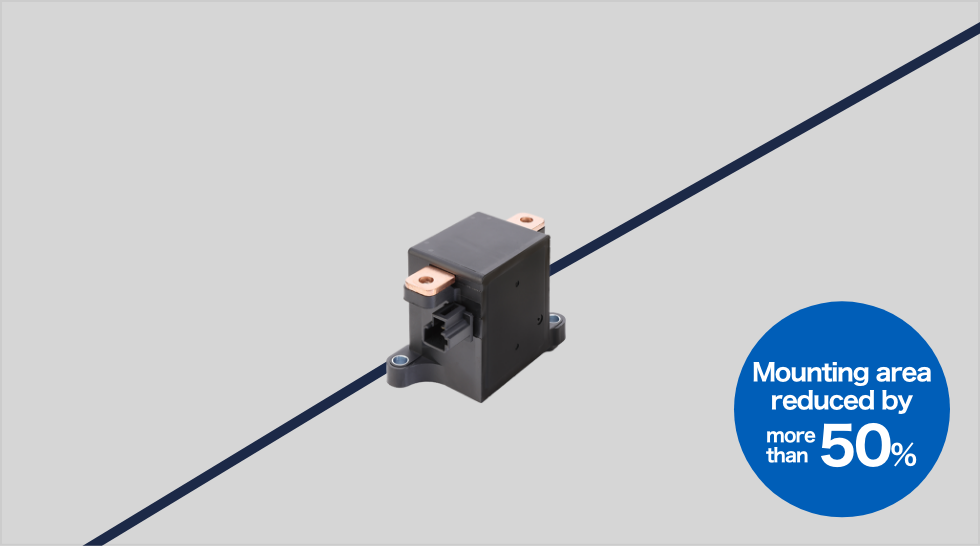
G9EK can switch in both directions (charging and discharging) with a single unit.
When there is polarity on the energized side
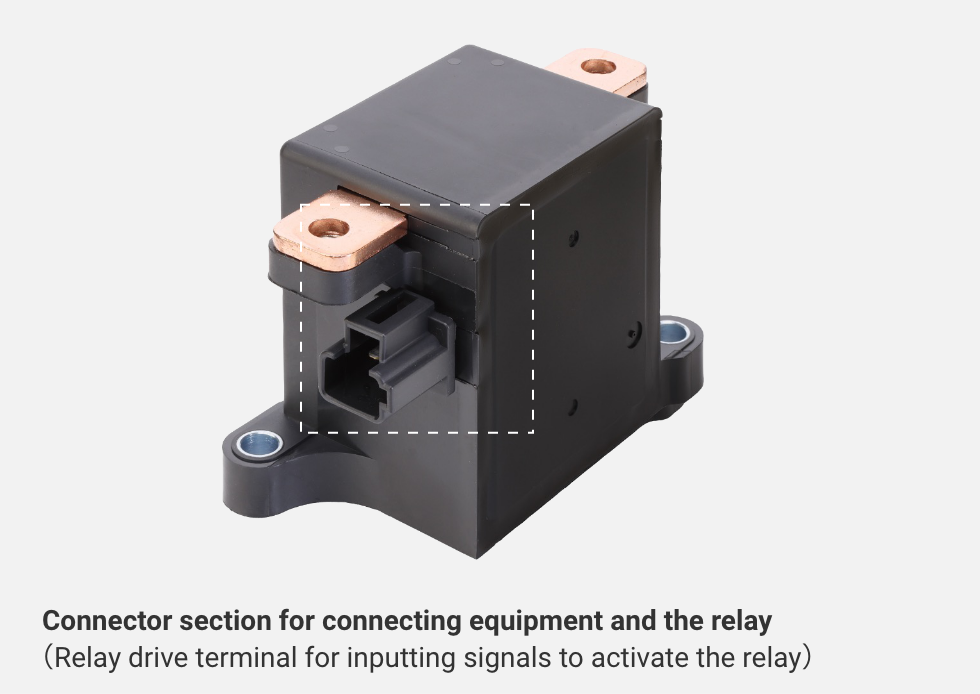
With polarity (unidirectional switching)
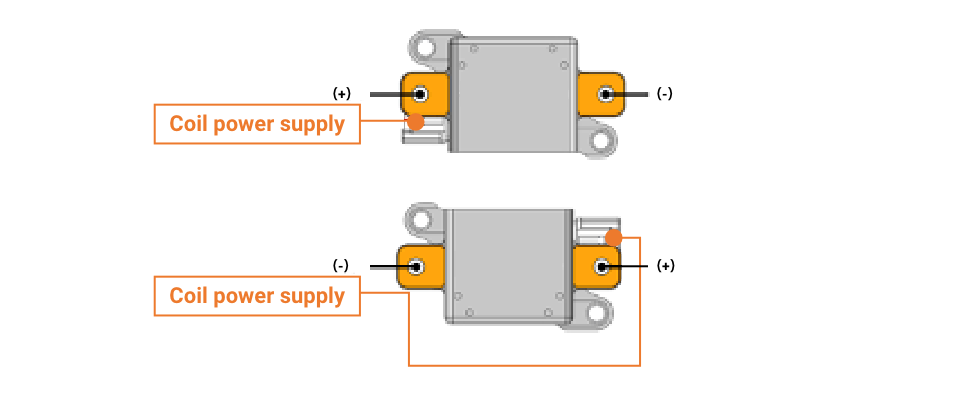
Because the terminals have polarity, the direction of the connector is determined, and space for wiring may be required depending on the equipment to be used.
Without polarity (bidirectional switching)
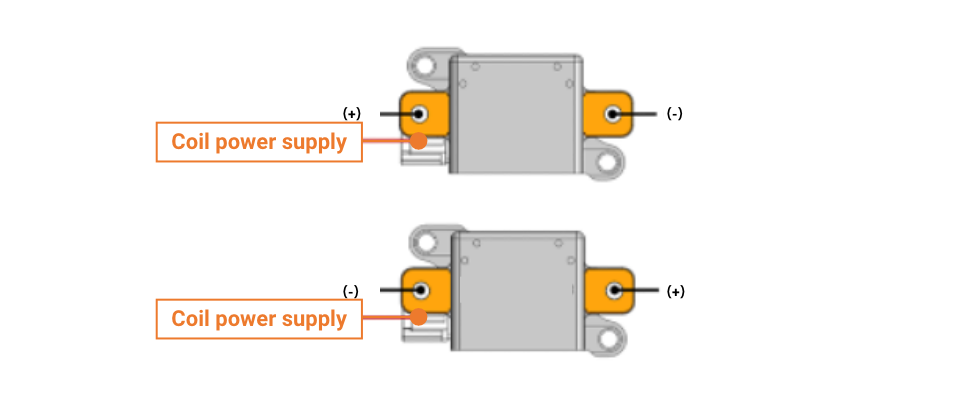
Because the terminals have no polarity, the direction of the connector can be determined depending on the equipment to be used.
*OMRON’s data as of November 2024
A high-capacity battery stores lots of power, which is instantly released in the event of a short circuit. This results in an instantaneous flow of extremely large currents. Large currents can cause not only heat generation and fire, but also damage to electrical equipment and circuits. The current in the event of a short circuit is expected to range from several thousand to 20,000 amperes, so it is necessary to protect electrical circuits and connected electrical components, and to ensure safety as a system, including safety parts (e.g., fuses) to prevent overheating and fire. Relays are required to have enough short-circuit performance to withstand large currents until safety is ensured by safety parts.
The G9EK has an excellent short-circuit performance that can withstand large currents of 5,000 A for 5 ms or more. This is the level at which an application using a 10 to 20 kWh class lithium-ion battery can withstand a short circuit in the event of an abnormality.
Example of current during short circuit
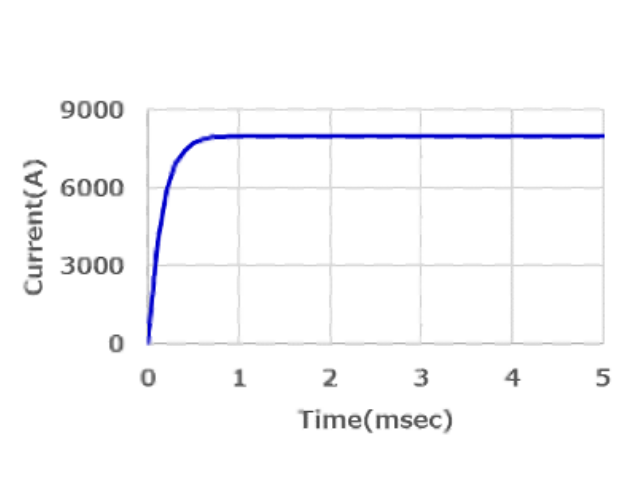
Electromagnetic repulsion generated on the contact surface
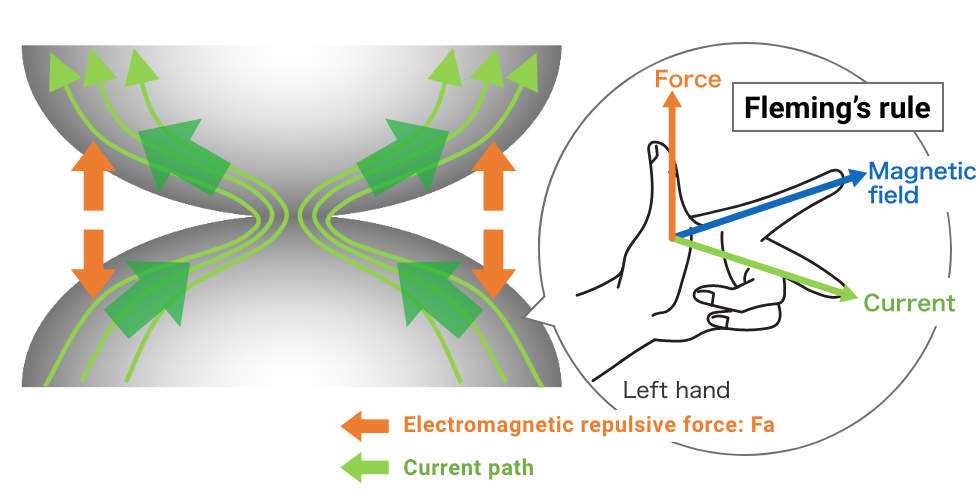
Short-circuit currents flow with a steep rise of up to several thousand amperes in a short period of time (up to 1 ms). When a large current flows, a strong magnetic field is generated around the current-carrying part, and the force of the current from the magnetic field (Lorentz force) acts in the direction of contact separation. This phenomenon is called "electromagnetic repulsion". To withstand large currents, a structure that can push the contact with a force stronger than the generated Lorentz force is required. The higher the capacity of a battery, the larger the short-circuit current and the stronger the electromagnetic repulsive force, which dramatically increases the difficulty level of design.
Conventional terminal structure
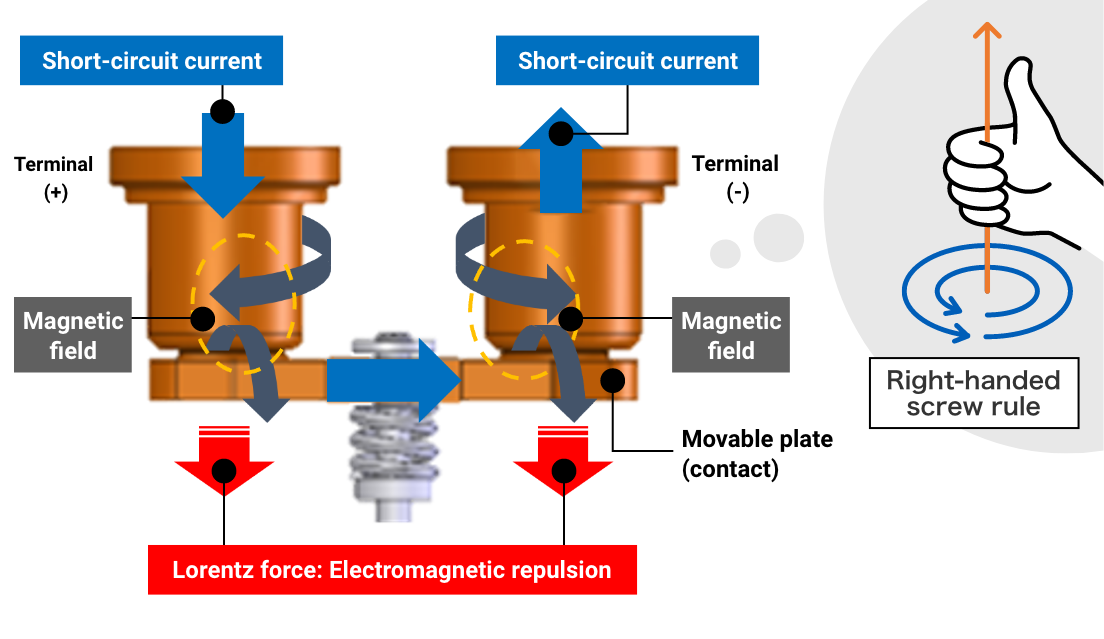
The magnetic field is concentratedly generated in the center due to the current flowing in a U-shape. As a result, the Lorentz force (the force the current receives from the magnetic field) is applied downward, making it easier for the contact to separate.
G9EK terminal structure
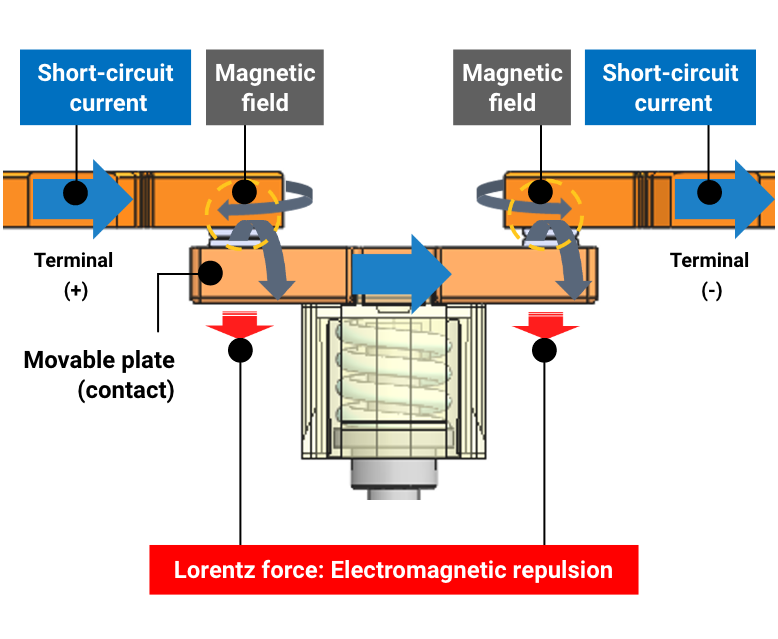
Due to the structural design in which the current flows almost horizontally, the direction of magnetic field generation is dispersed. As a result, the magnetic field generated around the contact point becomes smaller and the Lorentz force acting in the direction of pulling the contact point apart becomes smaller.
Comparison of electromagnetic repulsion force generated at the contact (movable plate)

Electric vehicles and electric motorcycles are typical examples in the mobility field and require a large amount of power (large currents) during acceleration and rapid recharging. Many battery-powered devices are also equipped with motors, which require large currents to rotate more powerfully. Therefore, high capacity (large currents) is also required for relays built into electric vehicles and electric motorcycles for safety interruption purposes.
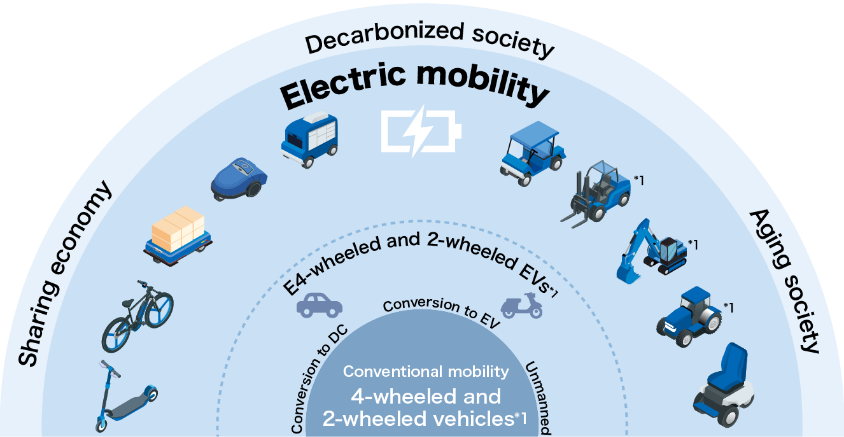
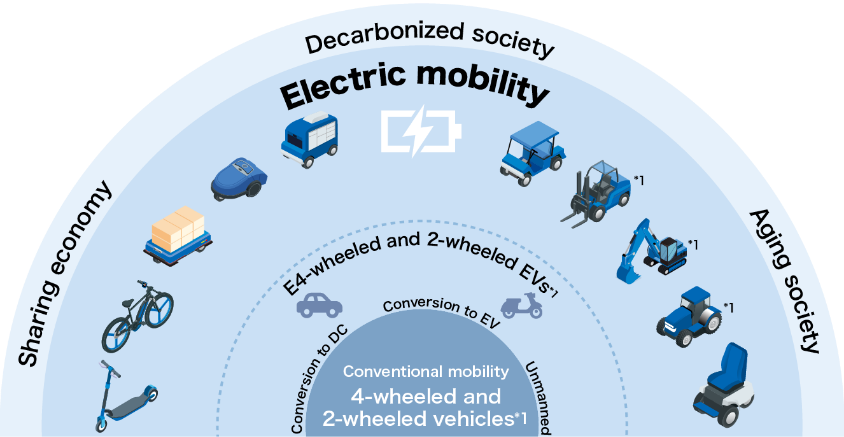

How much impact is 100G?
A general car collision is about 60G
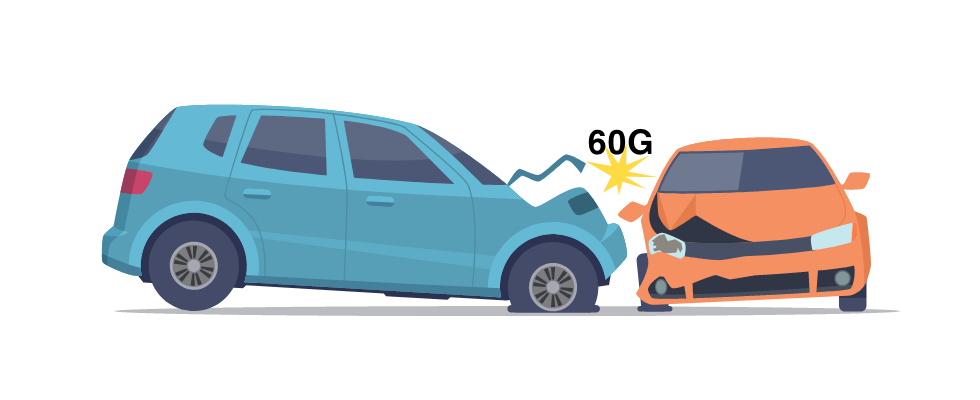
Note: This is just an image.
G9EK has 100G impact resistance
Withstands impact at the level of an F1 car collision!
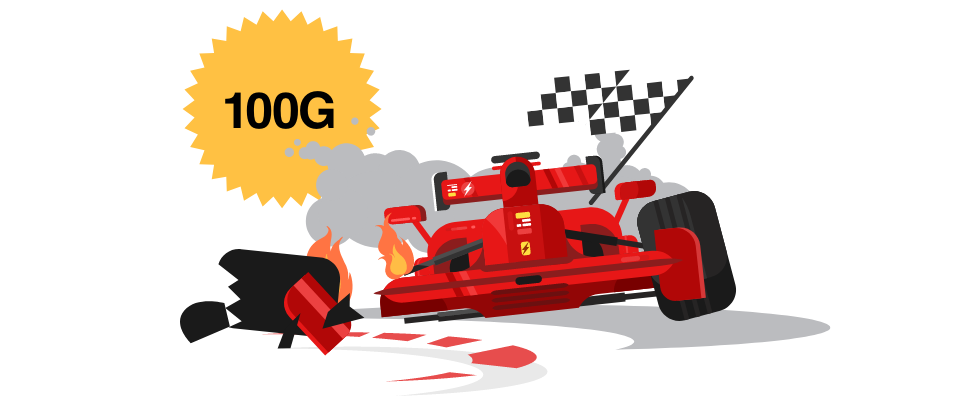
Note: This is just an image.
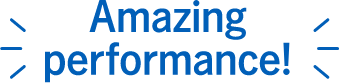
How about impact resistance when G9EK is ON or OFF?
Impact resistance when G9EK is ON
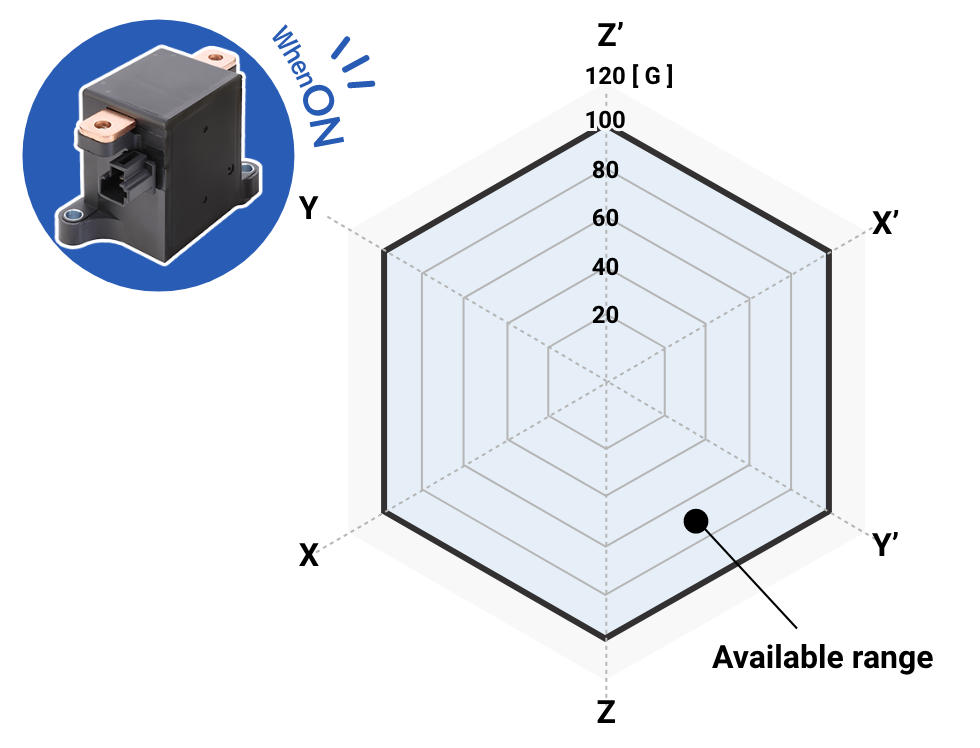
Impact resistance when G9EK is OFF
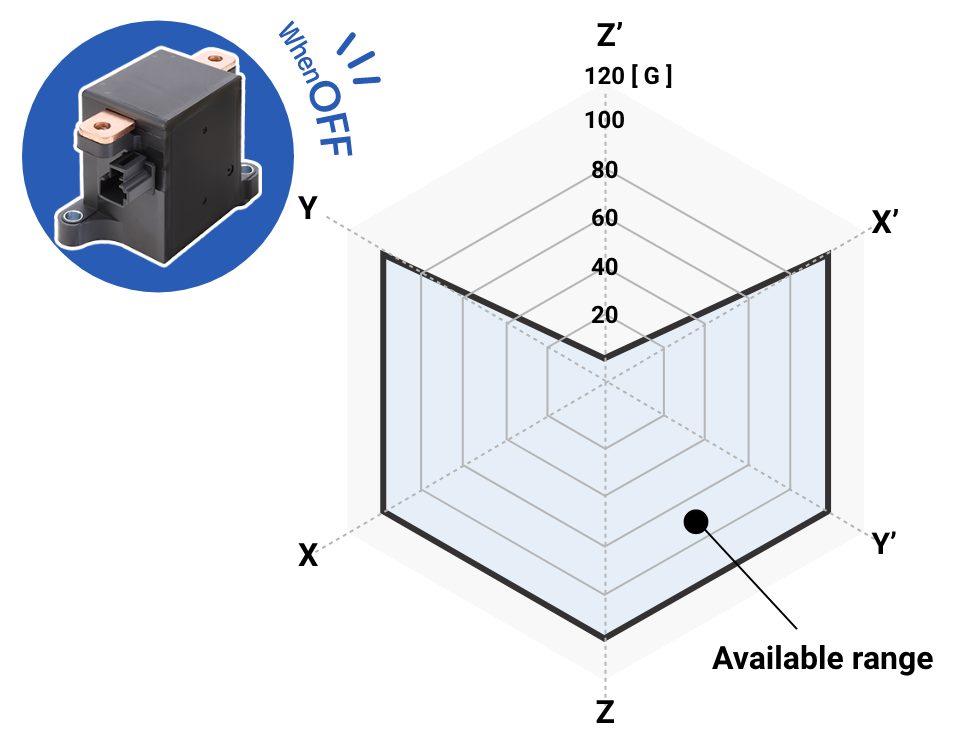
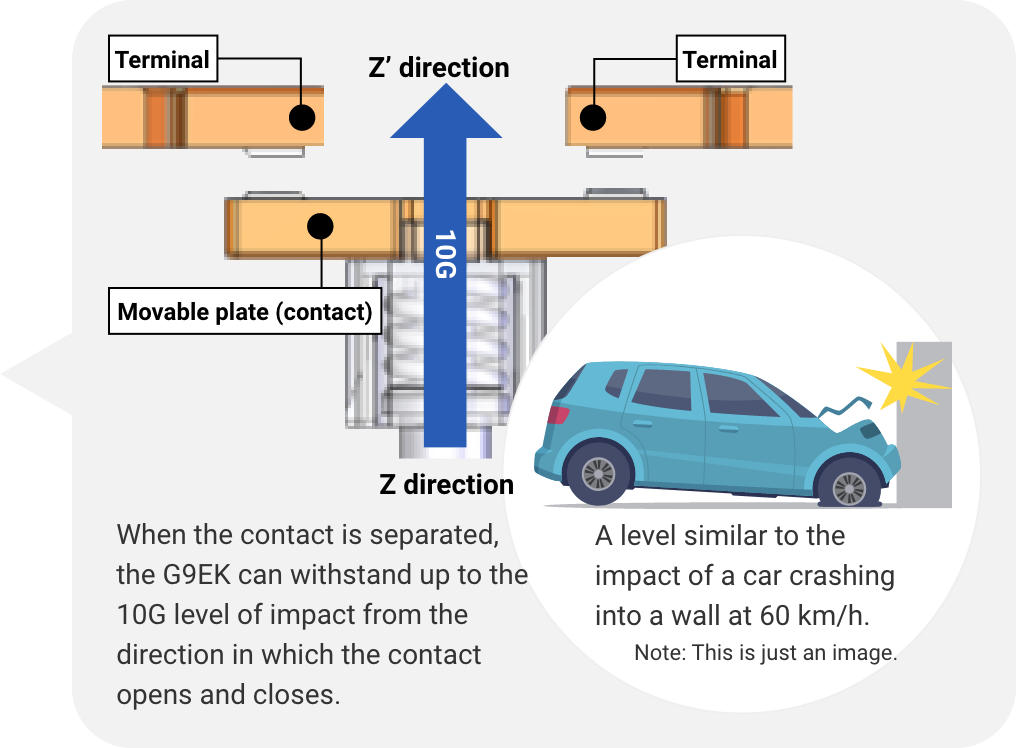
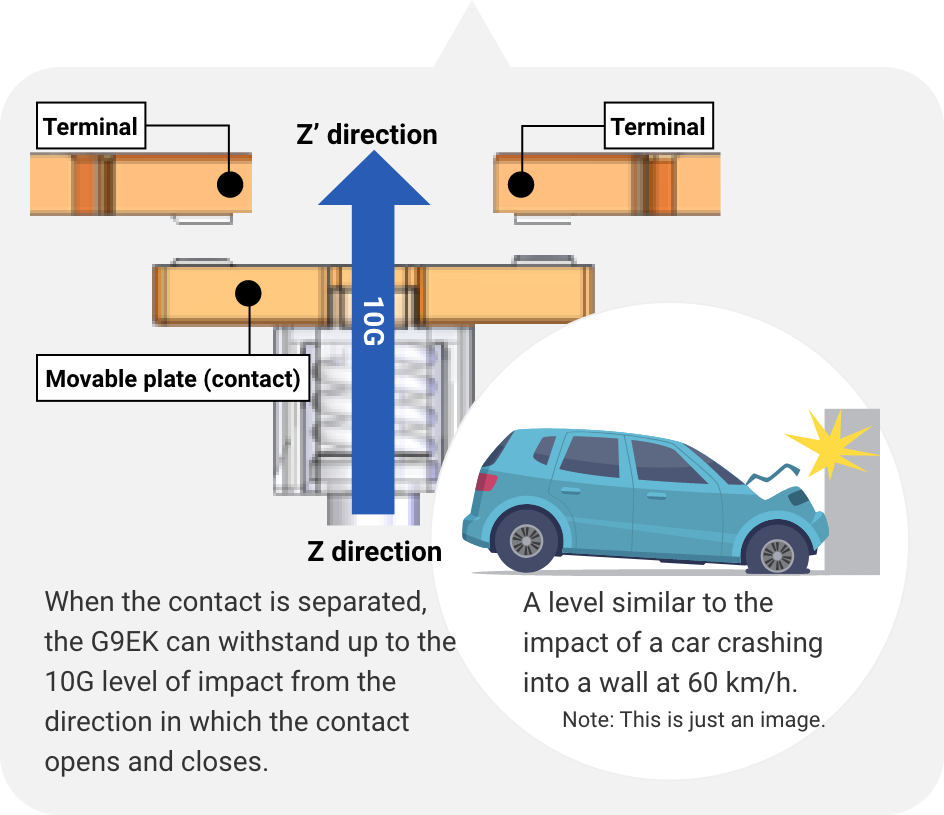
Conventional relay hinge type
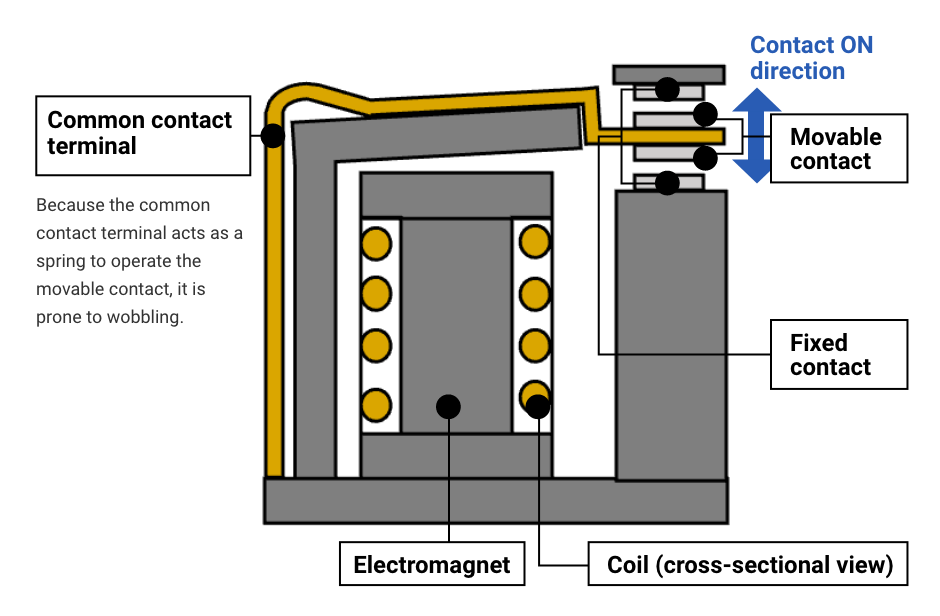
In the hinge type, the movable part of the contact is supported by a wire. Because the structure is simply pressed sideways by the force of the spring, it moves with impacts that are greater than the specified level.
G9EK adopted structural plunger type
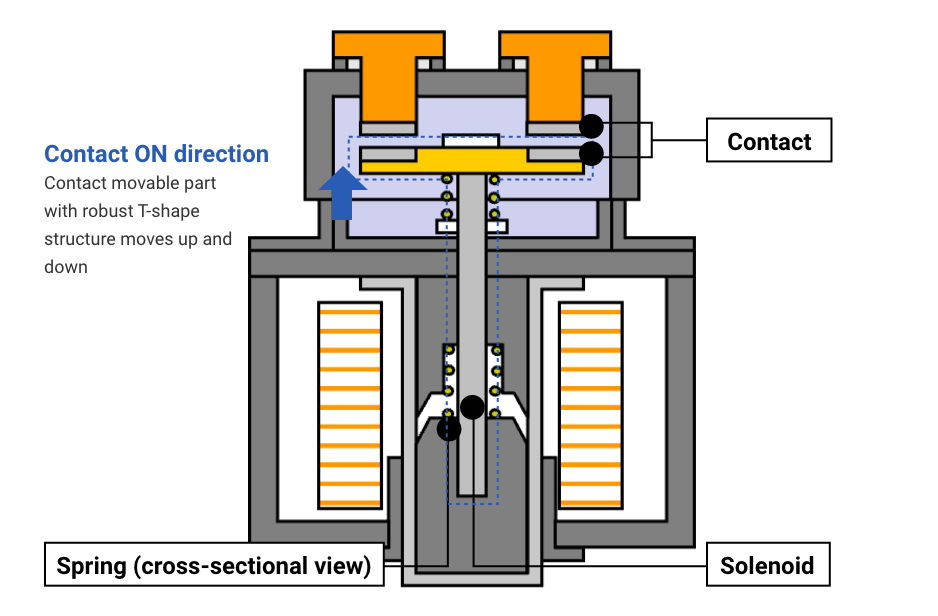
Due to the T-shaped design of the contact movable part, the plunger type is virtually unaffected by vibrations from the left, right, front, or back, except from up and down, which is the direction in which the contact moves. In addition, a solenoid coil is used to strengthen the magnetic force, which increases the contact pressure between the contact points and creates a structure that is even more resistant to vibrations.


500 A cutoff wall that could not be overcome only with conventional know-how relying on the power of gas
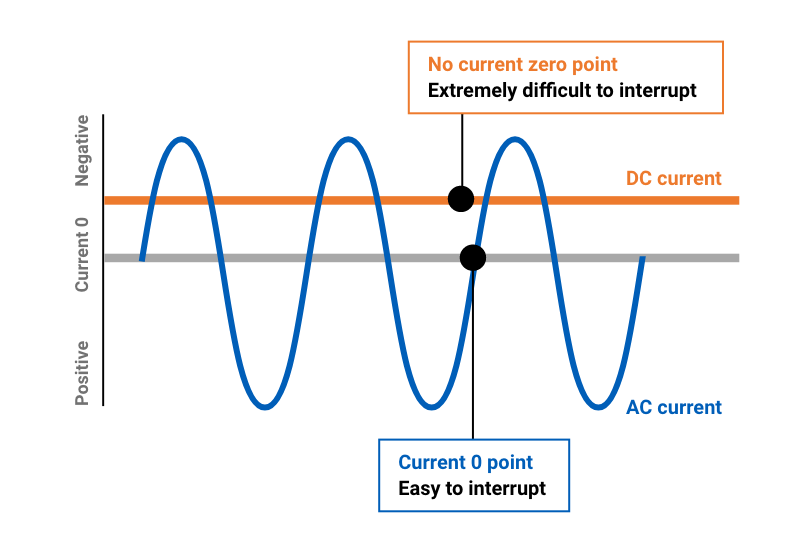
When trying to realize air switching (gasless) with high capacity and compact size
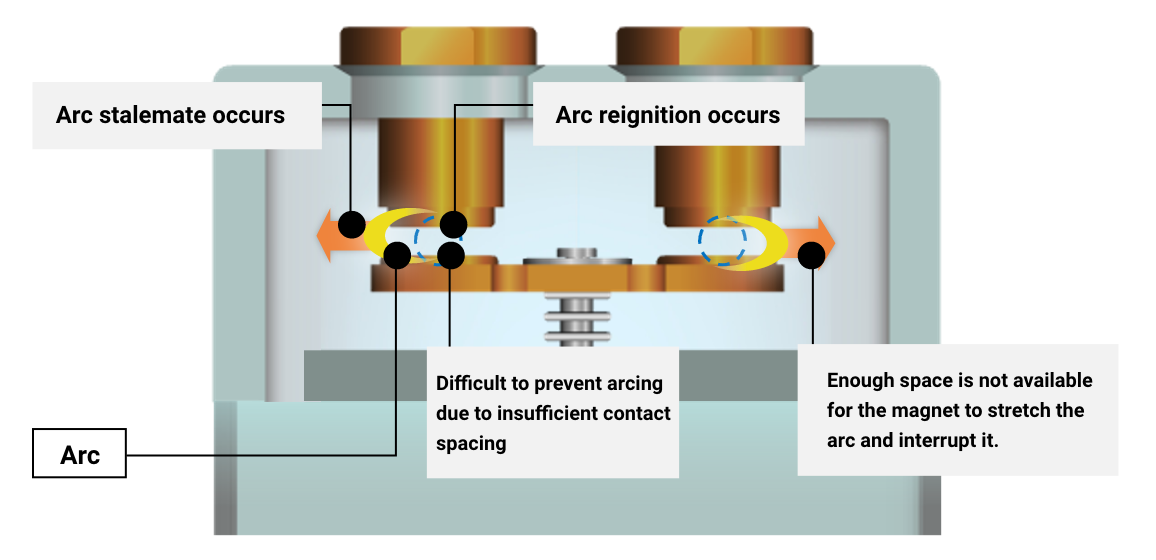
Regarding the Arc reignition phenomenon, we knew from past experience that the use of space is effective, but we had no data on exactly how much space was required. Until then, arc cutoff performance was dependent on the power of gas, so we did not have to consider detailed spatial design to extend the arc. What is important, however, is that the size is the same as that of conventional gas-sealed relays.
Even if we could achieve high capacity, customers would not see any benefit if the size of the product were to become too large.
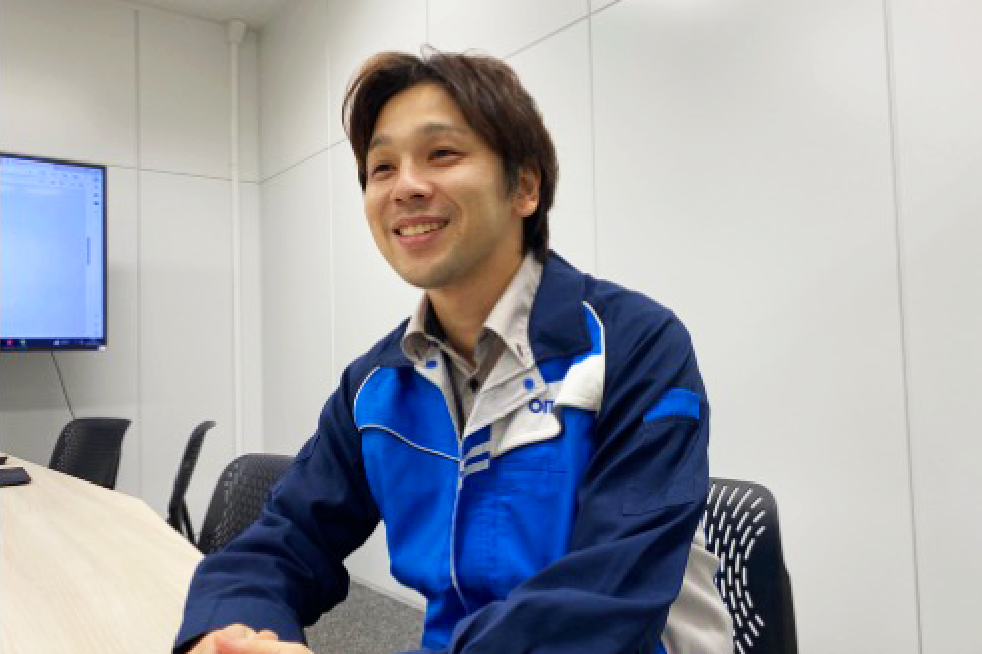
High Power Switching Technology Gr,
Business Management Division HQ
High Power Switching Technology Gr,
Business Management Division HQ


OMRON's unique new DC power relay structure
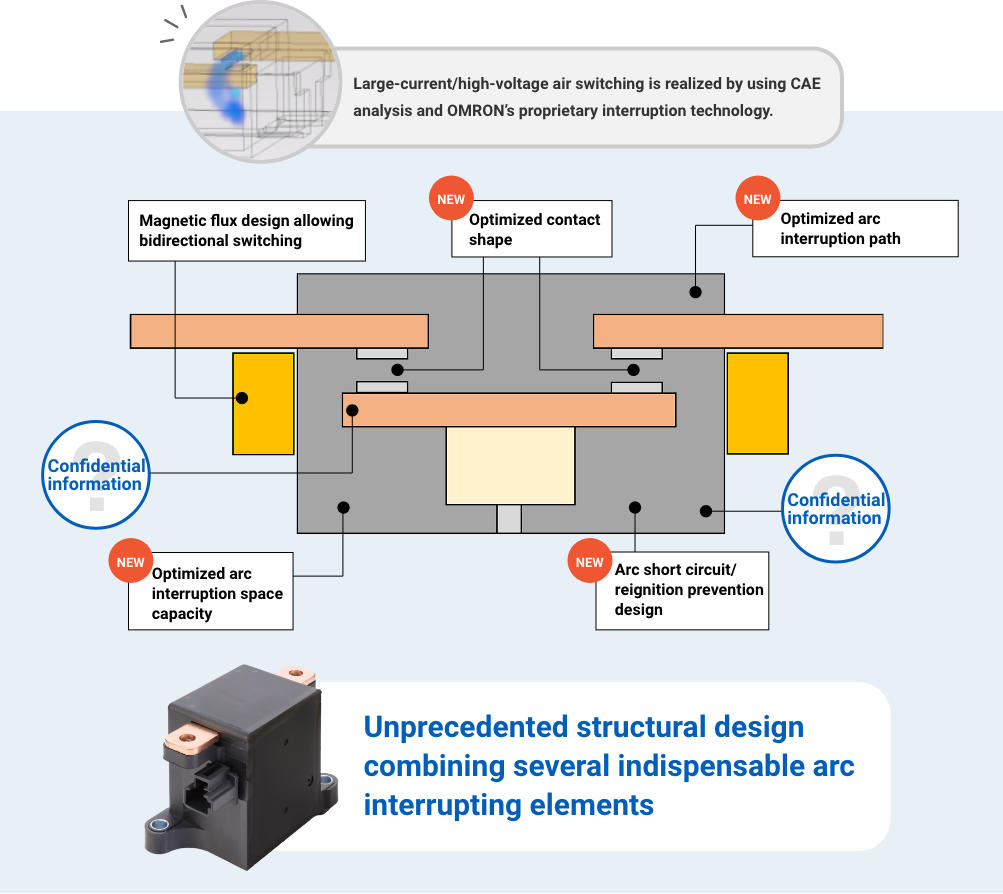
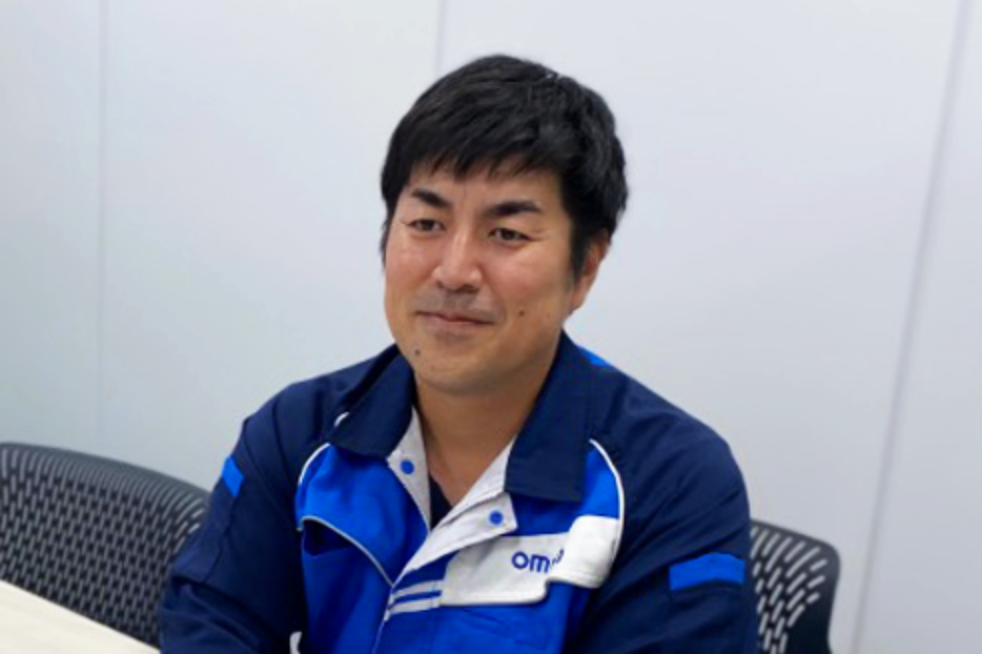
Business Management Division HQ
Business Management Division HQ
Through repeated simulations of how the arc moves during interruption using OMRON's proprietary CAE analysis technology, we incorporated structural engineering into the design to maximize the use of a small space and to increase the distance over which the arc can be extended. Furthermore, we actually confirmed by using an electromagnetic mirror whether the arc was actually moving as expected through the arc simulation and adjusted the structural design in detail to ensure the necessary spatial distance and to prevent arc merging/reignition. We also devised the shape of the contact to give it an advantage in interrupting large currents.
The design of the G9EK incorporates many such structures that are superior to interruption.


Ideal design vs. Mass-producible structure
Although there is an ideal shape in design, it is difficult to reproduce complex shapes and tight tolerance settings in mass production. Various adjustments were needed to realize the shape of parts that can be assembled on the production line and mass-produced with quality assurance. The absence of gas eliminates the need for the large equipment required to fill the product with gas and simplifies the structure of the product itself, while conventional production methods cannot be used because the structure of almost all parts is new. Various adjustments were necessary to correct unstable quality problems, such as assembly defects that could not be identified during the prototype stage and the inability to meet the process capability of each specification to ensure quality. I paid careful attention to the design of the key aspects of the product, such as interrupting performance and short-circuit performance, so we were able to obtain results that were generally in line with our expectations, but errors occurred in unexpected areas. After resolving one error, I was soon faced with another error. I could not improve the situation in one go, and it was similar to playing a game of whack-a-mole. However, I could not afford to waste time here, as the technical review stage took a considerable amount of time. Anyway, I tried to make improvements by repeating trial and error in the limited time I had.
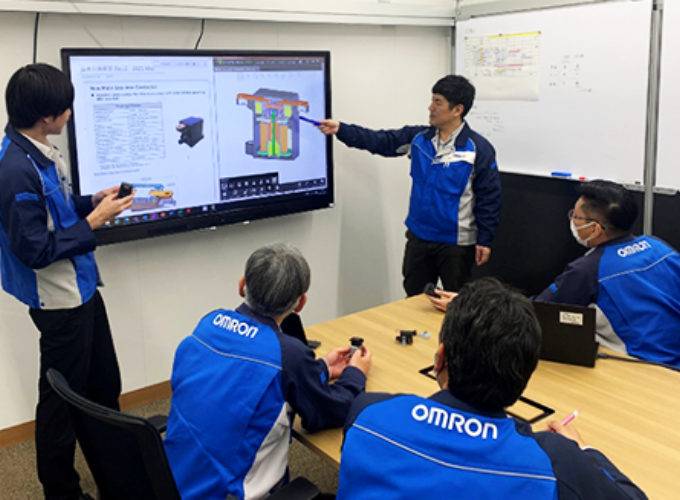


Electronic components can help address social issues
The road to commercialization was not smooth at all, and I encountered obstacles over and over again and I felt like giving up. However, all the members involved overcame the obstacles one by one and were able to launch the G9EK.
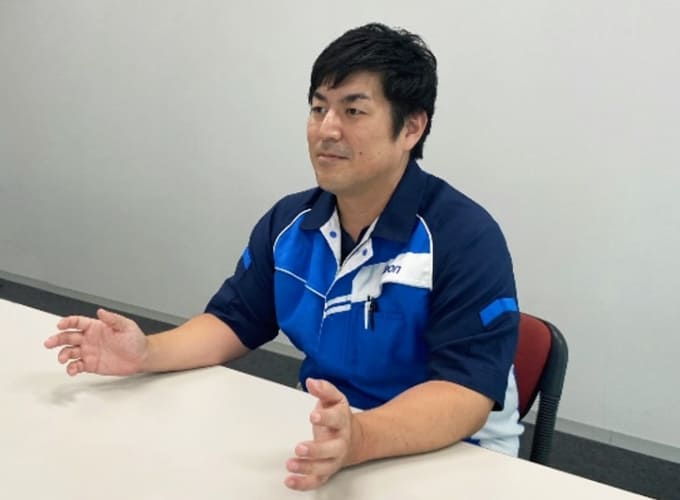
I have been working on DC power relays at OMRON for about 10 years, and the G9EK is not only my most challenging and difficult product to date, but also the one I have the most affection for. Being in a position to promote the electronic components business, we became increasingly aware that we could contribute to solving social issues by promoting carbon neutrality of the products we offer through the development of the G9EK. Looking back on that time, I feel that it was a few years during which everyone, backed by a strong sense of mission, worked together to push forward toward the commercialization of the product.
In order to create a carbon neutral world, it would be great if we could deliver G9EK, which is filled with our passionate desire, all over the world.
Recently, the required specifications for relays are on the rise, and we are developing DC power relays that can handle larger currents and higher voltages to meet these requirements. Although this is a challenging project, the entire organization is working to create new products through concurrent development that involves members from all fields from upstream to downstream. I would like to respond flexibly to the needs of society by speedily creating new value while using the technology and experience gained through the development of the G9EK. Please look forward to OMRON's DC power relays in the future.
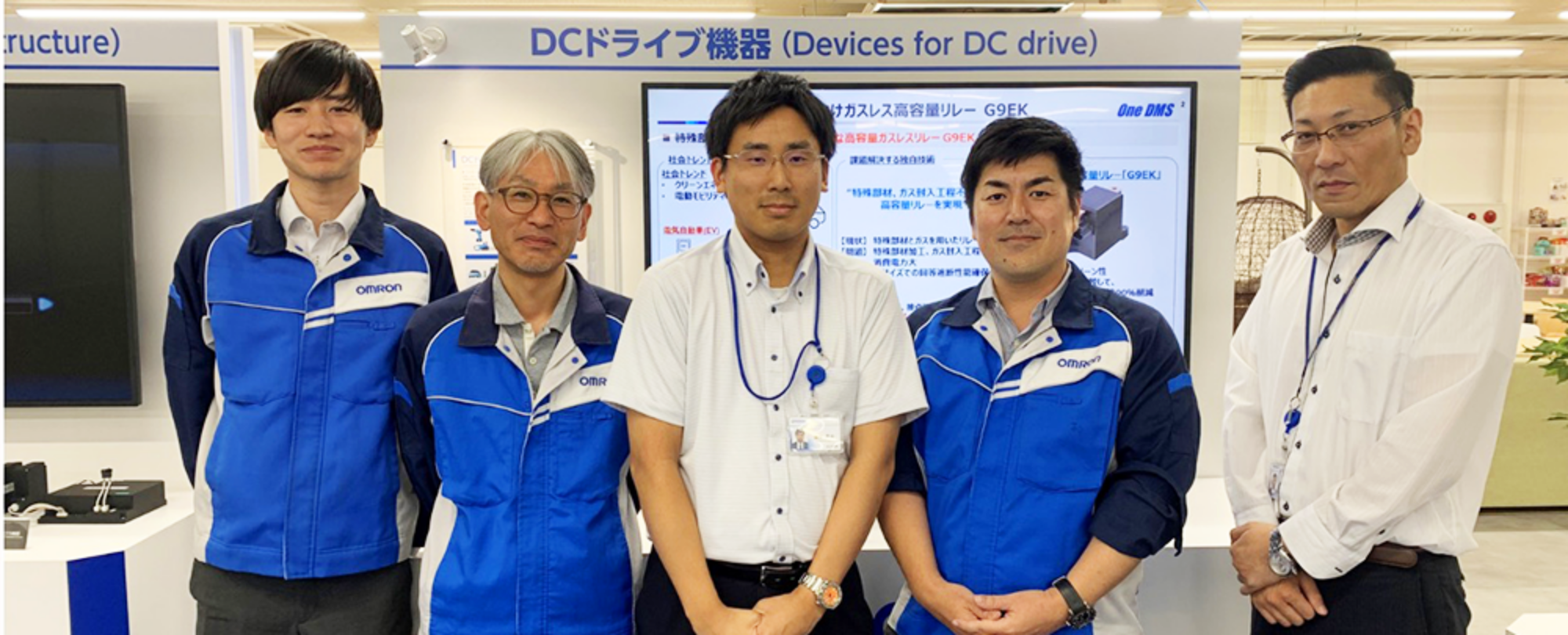
Related Contents
For automotive applications, please refer to webpages for In-vehicle Relays and In-vehicle Switches.