In recent years, the damage caused by climate change has become increasingly serious.
The mission of OMRON Device & Module Solutions Company is to solve social issues with our customers in order to achieve our long-term vision. This time. we worked with Weathernews Inc. to develop weather sensors (high-performance weather IoT sensors) to solve the social issue of reducing the risk of disasters caused by climate change.
Due to rapid climate change in recent years, conventional management methods cannot cope with such climate change in various business settings, such as construction and agricultural sites, and business losses are beginning to emerge. Therefore, in order to realize on-site spot weather observation, there was a need to develop a composite sensor module that can be easily installed and operated while keeping costs down.
We interviewed our members involved in the development of weather sensors to learn the story of how we worked with the customer to realize the sensors in just 15 months. Many new obstacles and factors such as “new industries”, “new applications”, and “new sensor technology development” stood in our way, but development members did not give up and achieved product release in a short period of time.
Interview to Module Development Dept. Members
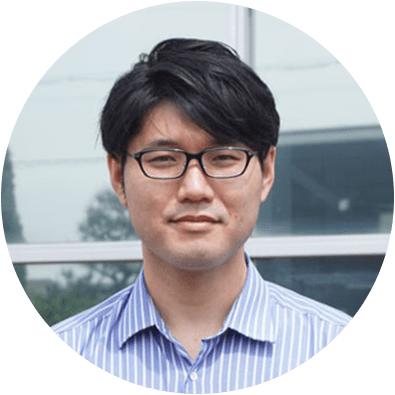
- Hideaki Kojima
- Project Leader,
Electronics Development
Group 2
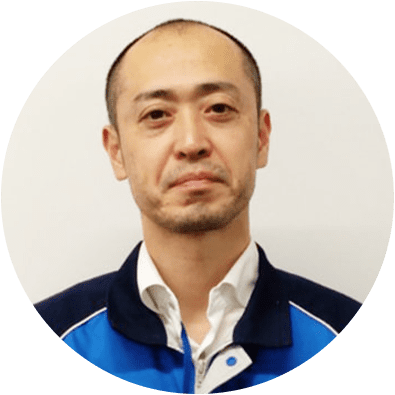
- Yusuke Aritake
- Theme Leader,
Electronics Development
Group 2

- Kenta Mochizuki
- Mechanical Administrator,
Mechanical Development Group
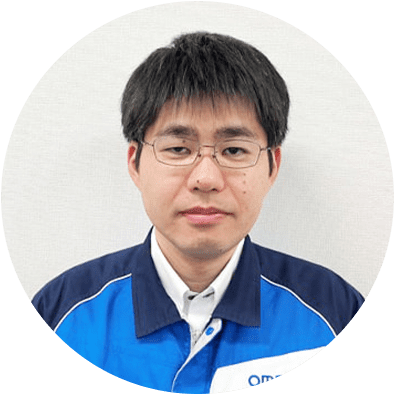
- Takashi Miura
- Systems Administrator,
Software Development Group
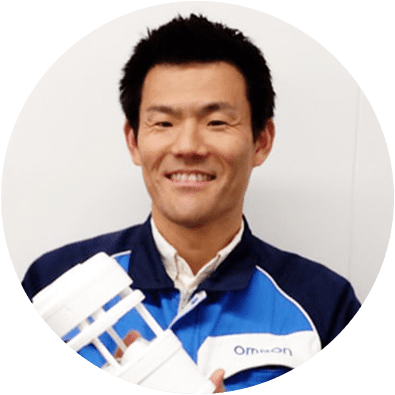
- Shingo Kawamoto
- Software Administrator,
Software Development Group
Table of Contents
- Philosophically align and resonate with the customer
Working together to solve social issues - Short-term development in new industries, new applications, and new technologies
Everything was challenging - New technology development obstacle (1): Rainfall sensor
- New technology development obstacle (2): Wind direction/velocity sensors
- Only 15 months left until realization…What's the key to success?
- What is OMRON's "module development capability" that creates new value?
- Future outlook
Continuing to solve social issues with customers
Philosophically align and resonate with the customer
Working together to solve social issues
Having previously used OMRON products in other applications, Weathernews approached us one day about the development of weather sensors needed to solve their new challenges.
The philosophy of Weathernews is “I want to help in time of crisis”, while that of OMRON Device & Module Solutions Company is “Solving social issues”. This project was started because of both companies' shared commitment to the social issue of reducing the risk of disasters caused by climate change. This shared vision reflects and resonates deeply with their philosophies, fostering a strong sense of collaboration and mutual understanding.
Aiming to solve problems through collaboration
between Weathernews and OMRON!
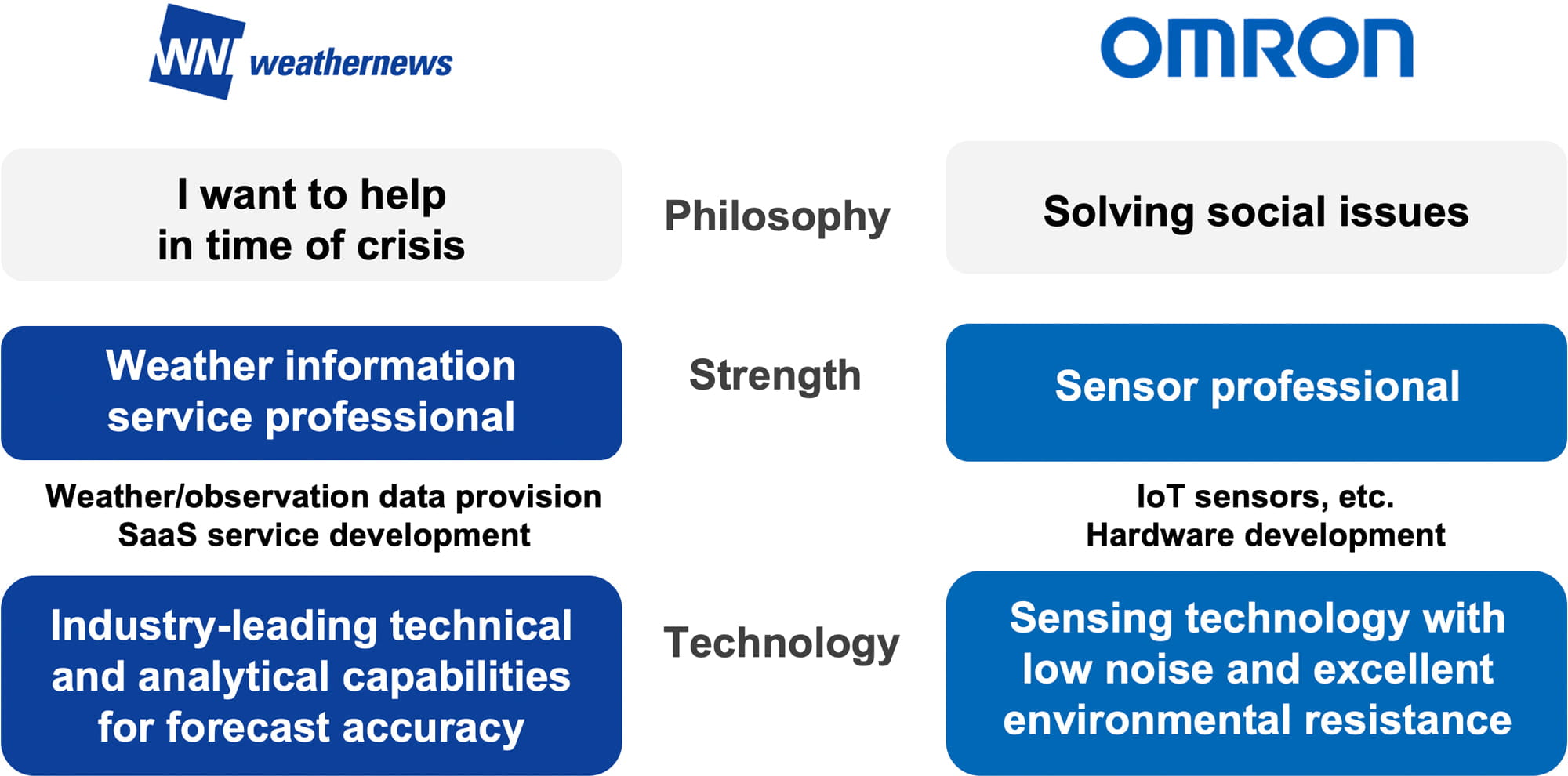
It may be well known that climate change is causing various problems, but challenges are emerging in various business settings as well. These issues include countermeasures against strong winds and heatstroke at construction sites, weather records for optimal crop management, weather management and safety enhancement at outdoor facilities, event venues, leisure facilities, etc., and marketing measures and analysis based on weather data.
Each site supervisor manages the site mainly based on weather forecast information and experience. However, we were unable to respond to sudden changes in climate in limited areas of the site, which sometimes resulted in business losses.
On the other hand, general weather sensors are comparatively expensive in terms of the unit price and operating costs, requiring large-scale installation on-site. Even in the case of relatively low-cost sensors, there were challenges in terms of sensor accuracy, and we were not always able to respond critically to solve on-site problems.
This led us to develop composite sensors that are cost-effective, easy to install and operate on site, and capable of acquiring multiple weather data with high accuracy from a single unit. It was very difficult and challenging to design the above in a well-balanced manner.
Comment from Weathernews
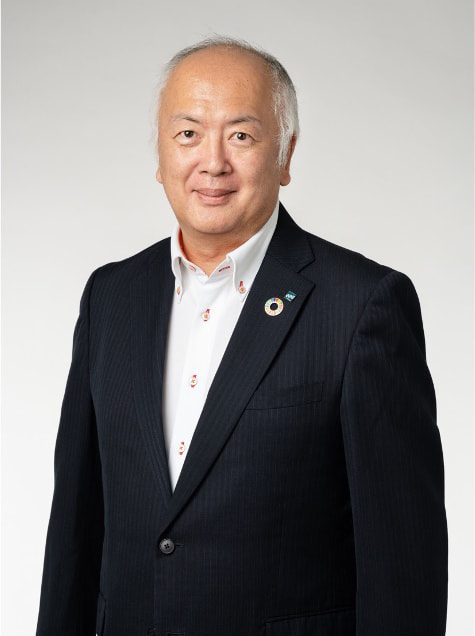
Yuichiro Nishi
Technical Director
Weathernews Inc.
We had been impressed by OMRON's superior technology, creativity and implementation from the planning stage of this project. For example, we are taught that the shape of raindrops is flattened when water droplets are crushed by air resistance, but OMRON, without being bound by conventional wisdom, actually photographs raindrops with a high-speed camera to understand the theory and reality of raindrop shapes, and then applies this knowledge to the design and shipping inspection processes. We would like to express our gratitude to OMRON for demonstrating the ability to take action through various experiments and other means to achieve a high level of quality.
Short-term development in new industries, new applications, and new technologies
Everything was challenging
We worked with our customers to determine from scratch what kinds of weather sensors would be accepted by the market, and then defined the concept.
The concept was a sensor module that can upload to the cloud 7 types of weather data necessary for weather observation and simply by connecting to the power supply users can use the information immediately.
We set a goal of releasing this sensor module in 15 months and took on three challenges in product development: one for the weather industry, one for outdoor use, and one for developing three new sensing technologies.
In order to achieve this highly set goal, we jumped into the customer’s site, shared knowledge, repeated the “Try & Learn” process, collaborated with the customer, and executed concurrent development to bring the goal into shape in a short period of time.
However, developing new technologies was not easy, and especially realizing a rainfall sensor and wind direction/velocity sensors was not a simple task.
New technology development obstacle (1): Rainfall sensor
The first challenge was developing new technology for a rainfall sensor. Since no one had any development experience or knowledge, we did not know what to reflect in the specifications.
Understanding “rain” itself before anything else
“Can we somehow create a sensor that solves on-site problems while keeping costs down?” With this in mind, we tackled the problem by first understanding “rain” itself as a step toward realizing the sensor. As an example, we tried to deepen our understanding by taking pictures of the state of falling rain using a high-speed camera, observing the characteristics of the shape during the fall, and comparing them with reference material.
After carefully observing and fully understanding the state of falling rain, we created a product concept, and eventually adopted an optical sensor detection method to build the product.
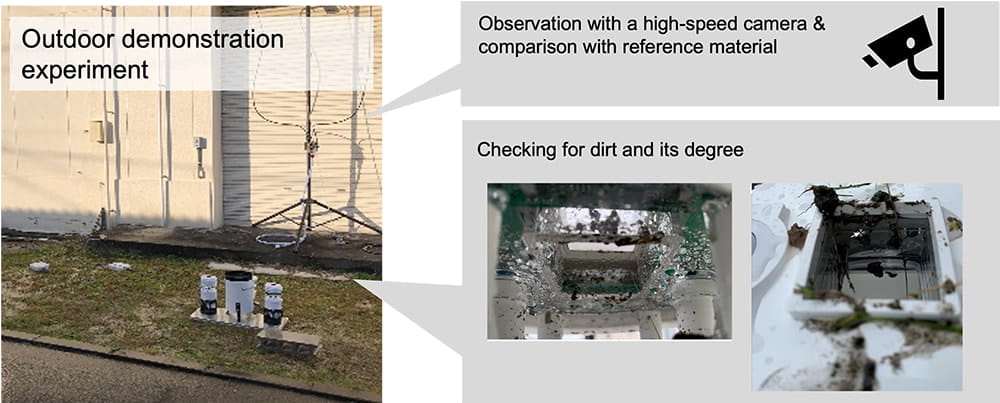
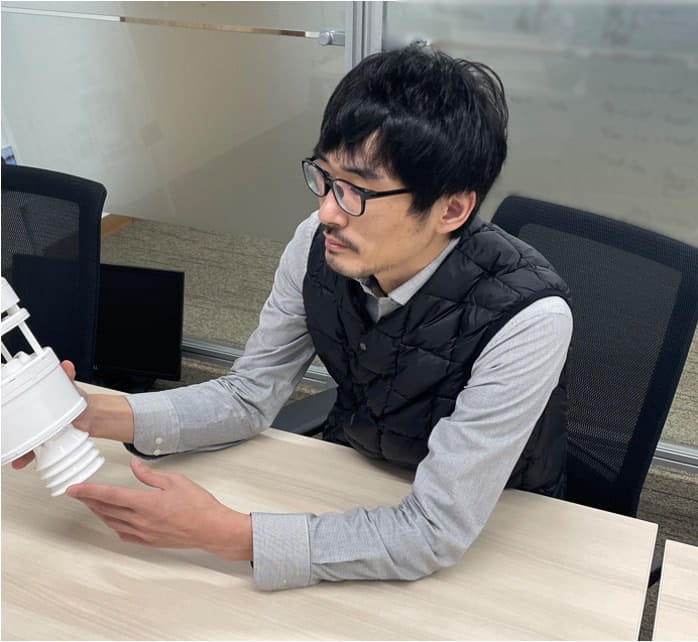
Experience industry know-how on-site and reflect it in our products
However, even if there were no problems in the experimental environment, abnormal data was sometimes detected when evaluation was conducted in the actual installation environment.
For example, when installed on the rooftop of a building or in other high locations, strong winds blow up like winds blowing through tall buildings. We experienced a phenomenon in which the number of detections jumped up due to the raindrops adhering to the sensor and staying there when it rained, and also due to the shaking of the raindrops caused by the wind.
To address this phenomenon, our software and hardware teams worked in unison to have repeated discussions while looking at the actual products on site, and together we tried an improvement approach.
By not only implementing software filtering but also reviewing the structure, we devised a way to prevent raindrops from staying on the sensor, and after repeated verification, we were finally able to create a product that could withstand the market environment.
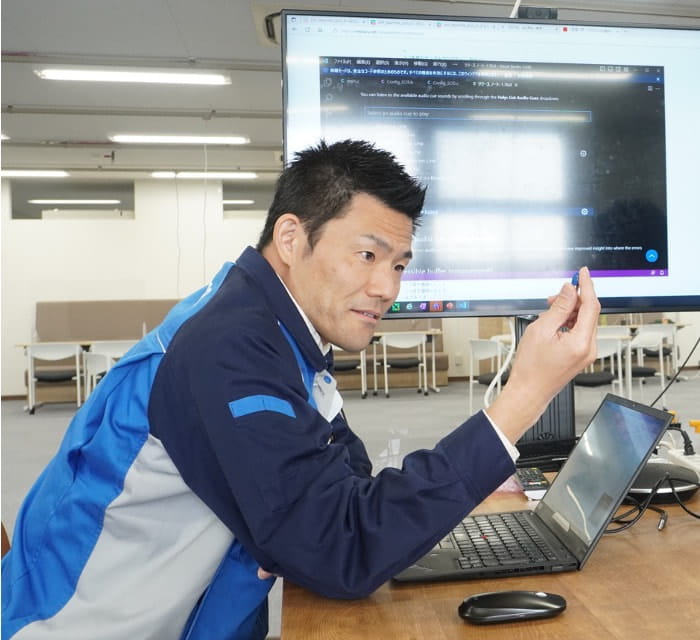
New technology development obstacle (2):
Wind direction/velocity sensors
The next challenge was the wind direction and velocity sensors. In particular, it was extremely difficult for us to make it possible to detect wind velocity of up to 50 m/s with the sensor while keeping costs as low as possible. 50 m/s is a fierce wind equivalent to 180 km/h. This velocity is said to be the speed of an express train, which could cause many trees to collapse and overturn trucks in motion. (Based on information provided by the Japan Meteorological Agency, https://www.jma.go.jp/jma/kishou/know/yougo_hp/kazehyo.html, here are the findings from the June 2024 Company Survey)
These sensors had specifications that had not been available in conventional sensors, and these specifications had to be realized because there is a strong need for observation at construction sites which are subject to considerably stronger winds than on the ground, such as building rooftops with a high risk of disasters.
Start by building an evaluation environment
How can we make the shapeless “wind” into a state that can be quantitatively evaluated? It was extremely difficult to build an evaluation environment prior to product development. We started by creating a simple wind tunnel machine that could produce quantitative wind velocity.
This simple wind tunnel machine can output up to about 30 m/s, but can only apply spot wind to the weather sensor. Therefore, by repeatedly measuring data in the actual outdoor environment and in the simple wind tunnel machine, and by using it after understanding the characteristics of the machine, evaluation in the laboratory became possible and we were able to proceed with the development.
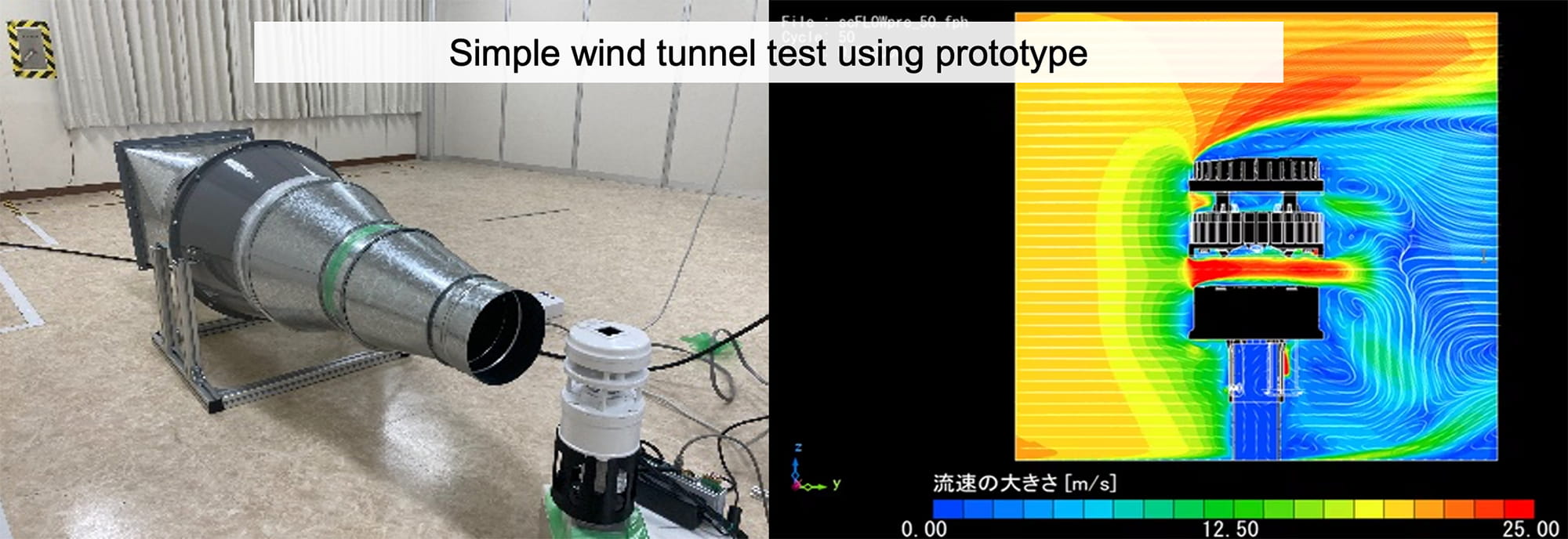
Finding optimal QCD solutions with module development capabilities
transcending mechanical/electrical/software boundaries
“Easy-to-handle sensors” were required by the market, so our challenge was how to realize target specifications as a module without incurring too much cost. This time, we aimed to realize the specifications with inexpensive elements and configurations by adopting an ultrasonic system, but realizing this was more difficult than we had imagined.
We constructed a mechanical structure that can stably capture wind through repeated simulations and actual measurement tests. We then designed the output from the sensor element to be passed to the input of the microcomputer with as much noise removed as possible on the electrical side. By preparing 35 different setting parameters on the software side and combining them, we achieved a state where accurate values can be obtained.
In this way, after transcending the team boundaries of mechanical/electrical/software skills, and by having intense discussions over and over again in the same place while looking at the same thing and the same results, we were able to make them into a shape.
Tackling the 50 m/s wind velocity obstacle
Finally, we took on the challenge of realizing a 50 m/s wind velocity measurement.
Generating this wind velocity range requires a large and special equipment, which cannot be installed in-house.
Therefore, we decided to find a special wind tunnel test site to conduct the experiment, using the customer’s knowledge as a reference.
It was only towards the end of our development that we were able to perform stable wind velocity measurements using a simple wind tunnel machine, so it was around that time that external 50 m/s wind velocity testing became possible.
With the results of our in-house evaluation using a simple wind tunnel and our desk theory, we attempted a 50 m/s wind velocity test.
However, it did not work.
Theoretically, it should be possible to measure wind velocity, but for some reason we were unable to measure normal values. We became disheartened because we could not figure out the cause of the problem.

But we did not give up.
To break through this situation, we launched an all-out battle involving the customer.
With the help of the customer's production department, we had departmental personnel implement various adjustments in many areas. It was not simply a matter of having adjustments made. There were many innovations and ideas in the adjustment process. Thanks to the customer's cooperation, we were able to generate approximately one month for development study.
In the development department, we repeatedly carried out steady hypothesis verification within a period of only one month.
We created better countermeasure ideas and repeated the “Try & Learn” process by steadily acquiring data regarding countermeasures based on hypotheses, viewing the acquired data together with the customer, and receiving advice about wind.
When ideas were connected to arrive at effective countermeasures among various proposals, we were finally able to realize a 50 m/s wind velocity measurement.
Although the customer was also present at the site, we all shouted and fist-pumped with joy. We felt like giving up many times due to the pressure of an approaching deadline. but it was a moment when we felt glad that we did not give up until the very end.
Wind tunnel test site when 50 m/s was achieved
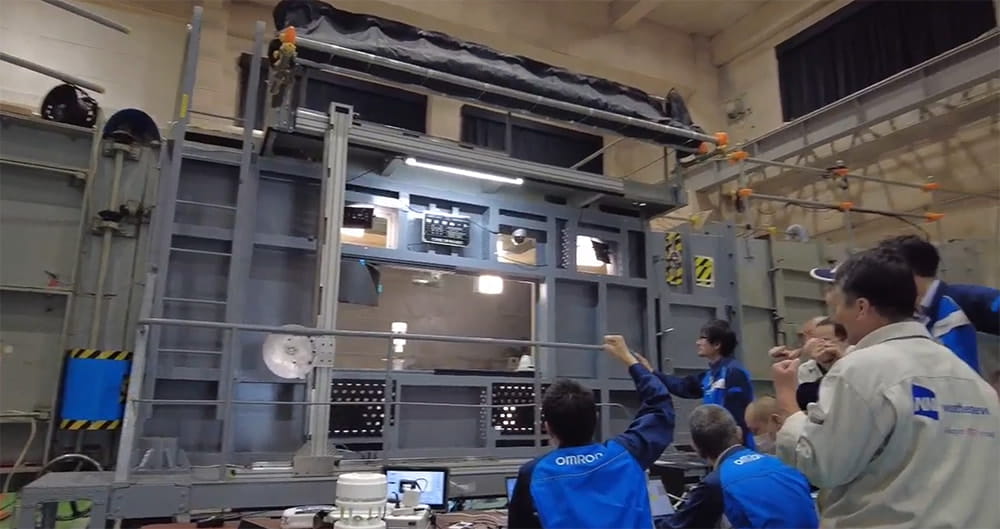
Only 15 months left until realization…What's the key to success?
Concurrent development to avoid risks while moving forward
The major change in the theme policy this time was to proceed in a lean startup* manner.
By conducting prototyping at an early stage and going through a detailed hypothesis verification cycle, we moved the theme forward even though the specifications had not yet been finalized and aimed to reach the goal in the shortest possible time.
In order to be successful, we all needed to support each other by being aware of the team’s commitment to making this theme a success, deciding how to take risks, and collectively following up with departments in need of help. By having our sales, planning, development, production, and quality staff involved in the theme at an early stage, and by having them incorporate this way of proceeding into their own departments, we were able to obtain the cooperation of the people involved.
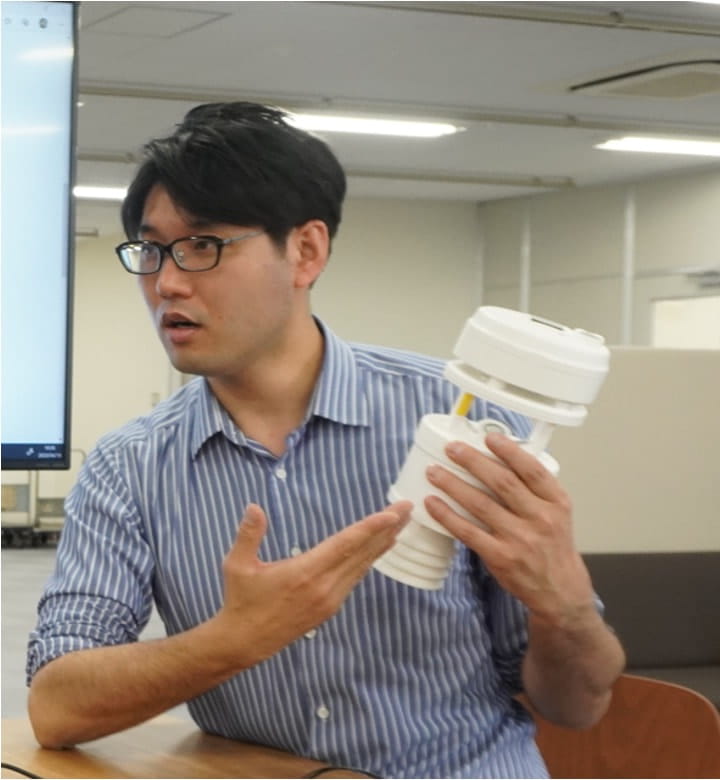
* What is Lean Startup?
A product development method that evolves while learning through repeated feedback of customer reactions and data obtained from the site at low cost, in a short period of time, and with minimum assets. This method aims to provide essential value in the shortest possible time by thoroughly eliminating waste and developing products in an agile, efficiency-oriented manner, and is considered suitable for new business development.
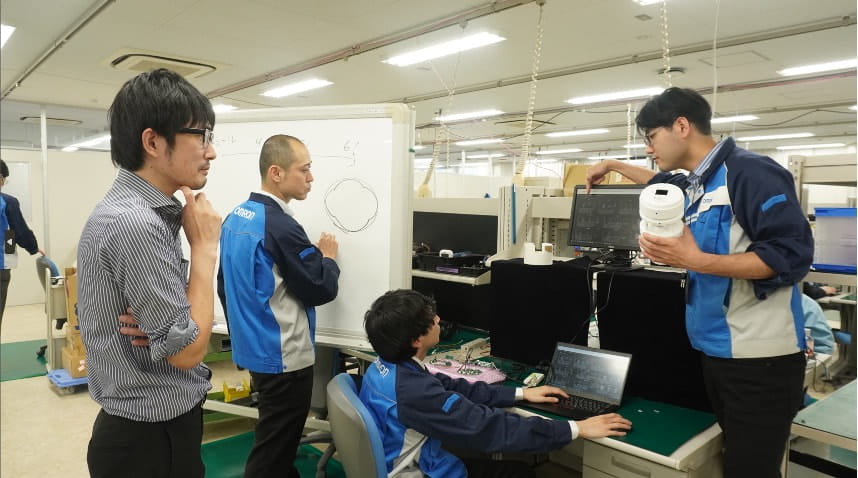
Avoid losing focus on customer-oriented perspective
We sometimes receive comments such as, “Isn't there a disadvantage in involving various departments from an early stage, making it harder to consolidate opinions?” However, we make decisions based first and foremost on a thorough customer-oriented perspective to ensure that we do not waver in our direction. For this reason, we ourselves, as developers, communicate directly with our customers and conduct repeated on-site demonstration experiments so that we can talk about “why these specifications are necessary” in a first-person manner.
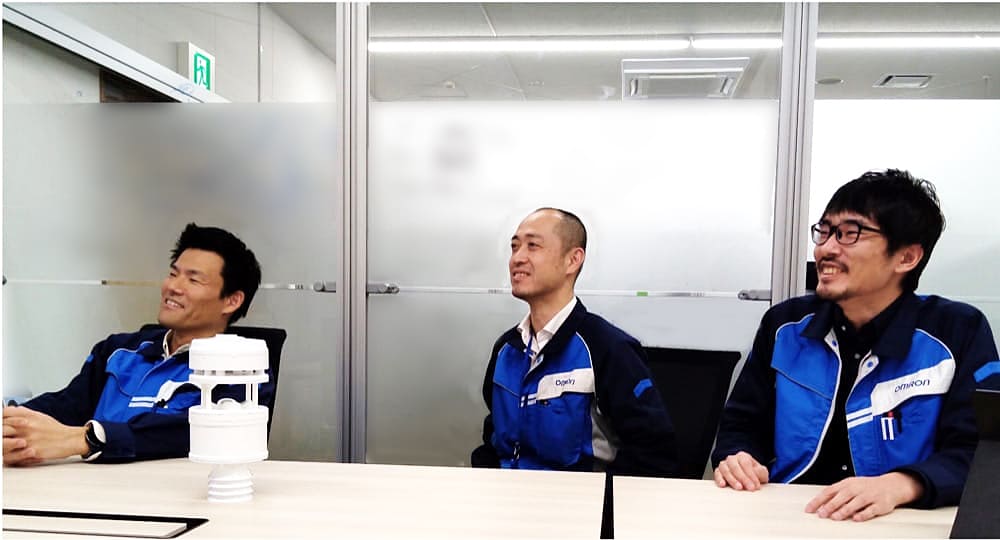
An equal relationship where we can talk about anything is most important
Another important thing is to foster a climate in which we can say whatever we want to say. If we are too concerned about the delivery date and avoid what we want to say, we won't be able to make a truly good product. I believe that we can deliver new value by thoroughly discussing and conflicting based on market and customer challenges. To this end, we have long built relationships with various related departments, and have also fostered a sense of camaraderie at events outside of work.
What is OMRON’s “module development capability” that
creates new value?
In general, module development is sometimes talked about synonymously with embedded development, but the definition is different from what we mean by module development. We do not consider it simply “embedded technology” (technology to optimally incorporate and package various materials and components), but rather consider it synonymous with the ability to provide solutions.
We believe it is important for us to provide solutions while keeping an eye on the social issues that lie beyond our customers and their customers. We cannot provide solutions simply because we have embedded technology. In order to deeply understand actual applications through collaboration with customers and provide speedy solutions, it is important to maximize and effectively utilize not only internal assets but also external assets that are not owned by the company. Therefore, we value early involvement of all relevant departments within the company through concurrent development to provide solutions that fit the customer's application as early as possible.
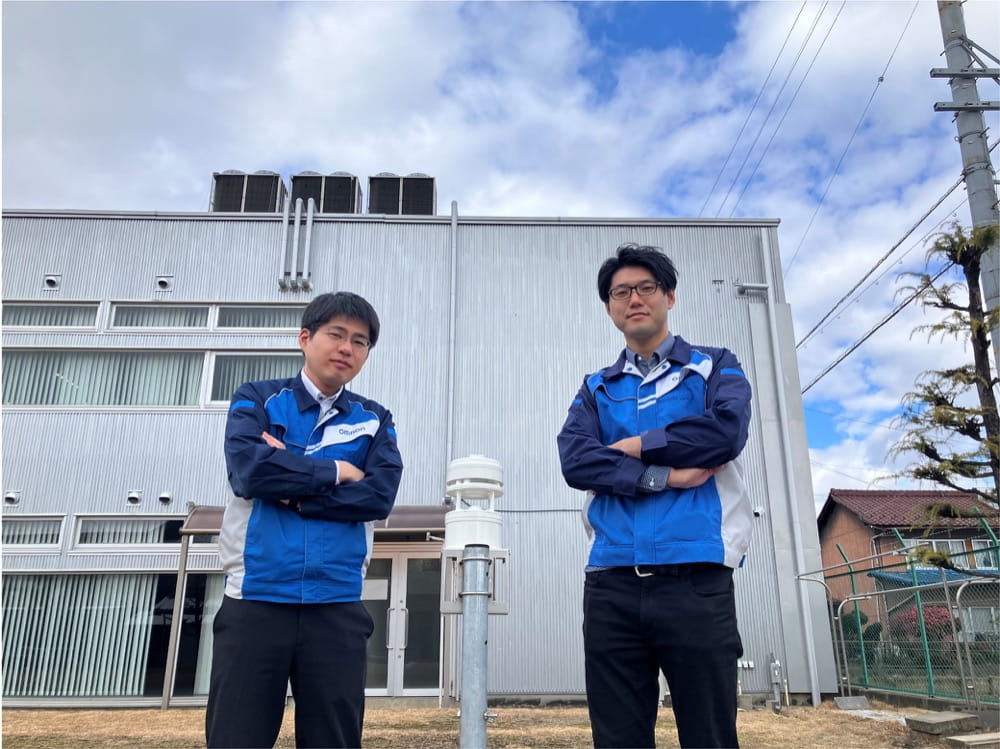
We identify the issues that need to be solved and materialize solutions to the customer's problems by using embedded technology to fit the application through collaboration with the customer. We then supply them as mass-produced products with quality assured at an early stage through concurrent development. Only when these can be realized in an integrated manner, we can say that we have the ability to provide solutions. This is what we call module development capability.
OMRON's module development = Capability to provide solutions
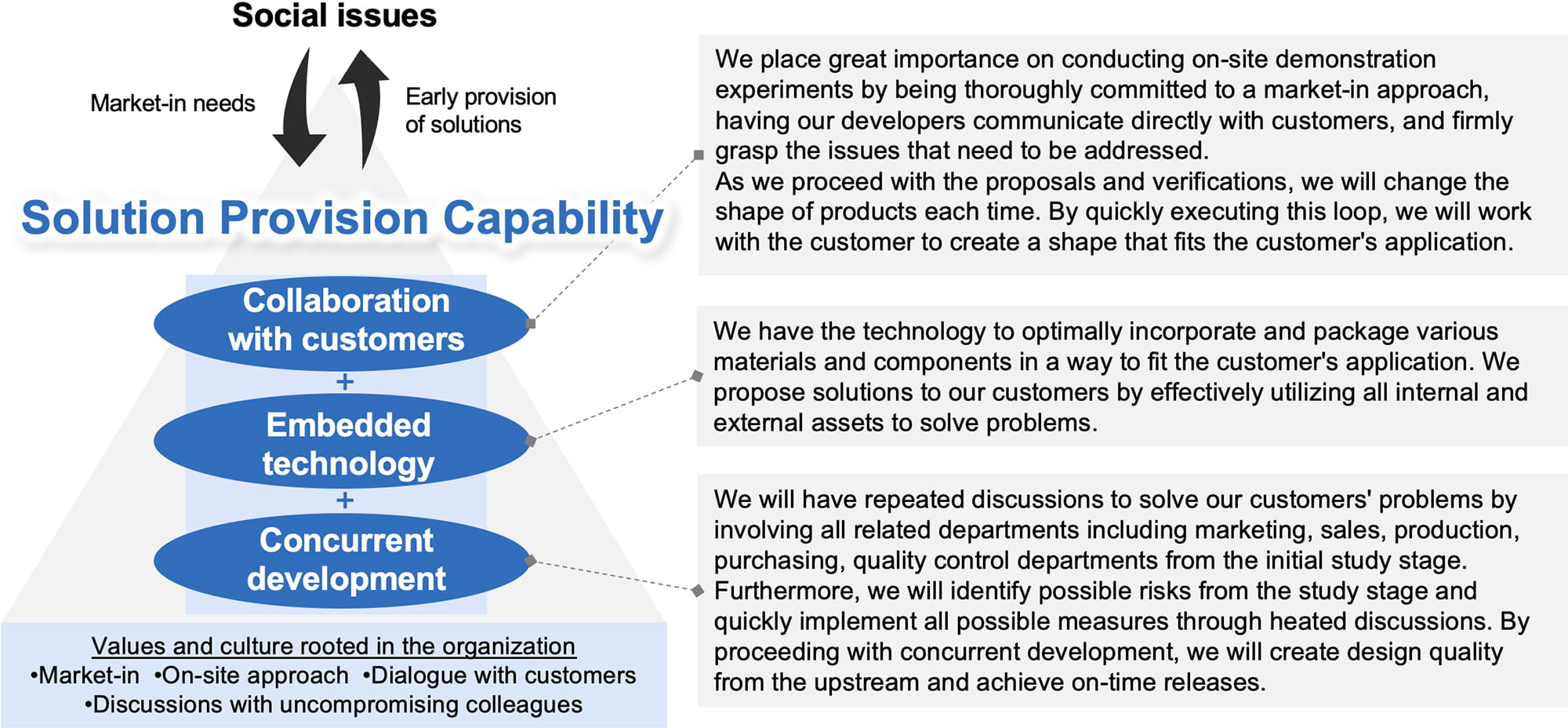
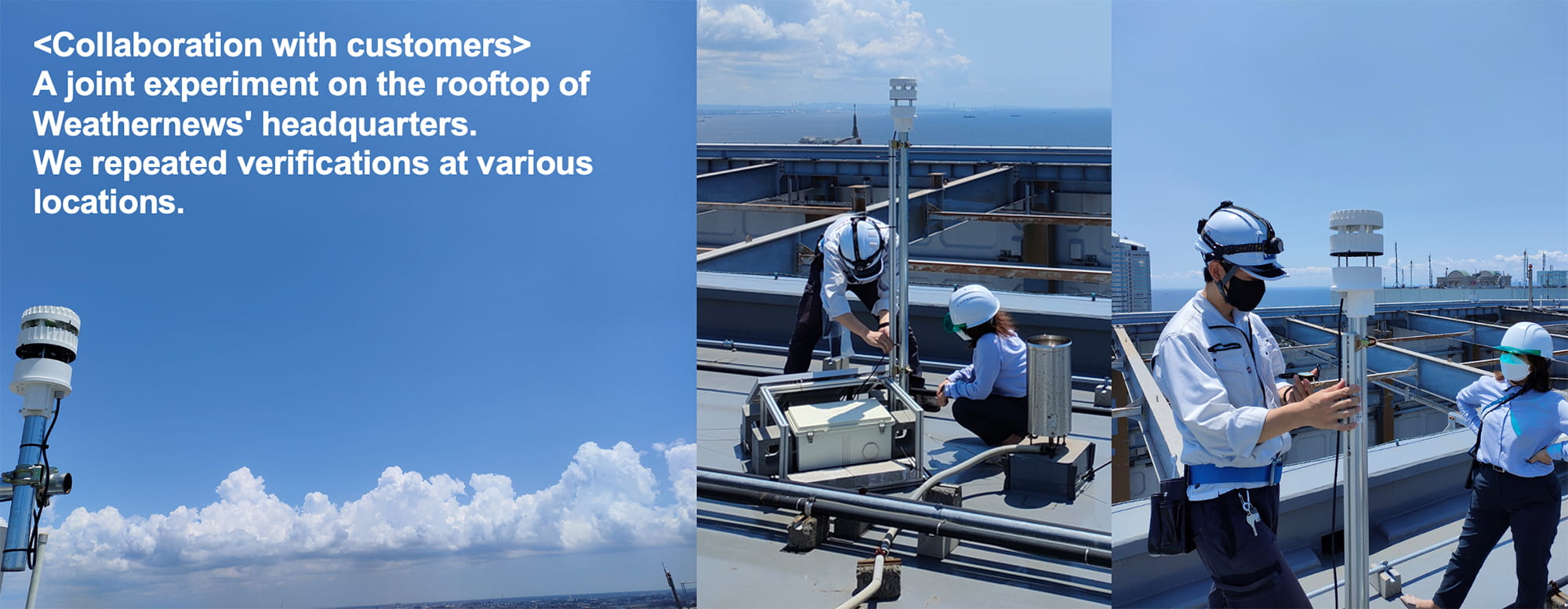
Future outlook
Continuing to solve social issues with customers
“We want to solve social issues with our customers.” This has always been our strongest desire.
We have been creating value based on market-in and on-site approaches, and we are convinced that our stance of developing products from the perspective of the market and customers has not been mistaken. We would like to show both inside and outside the company that even component manufacturers like us can solve social issues.
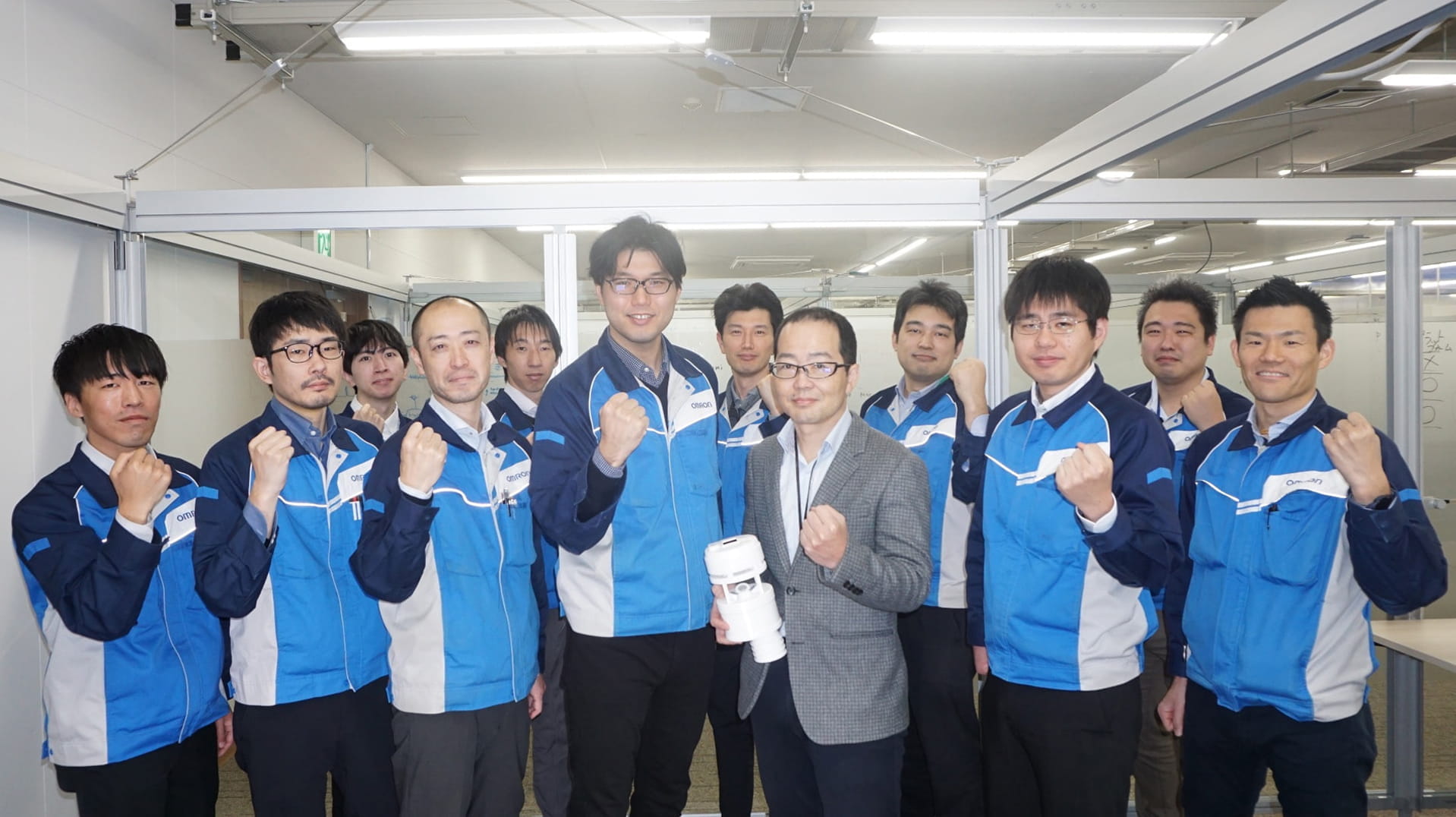
Contact Us
Contact Us
Related Contents
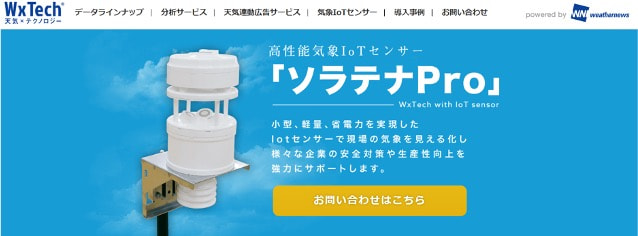
Click here if you are considering weather forecasting
services using weather sensor modules
(Only Japanese)
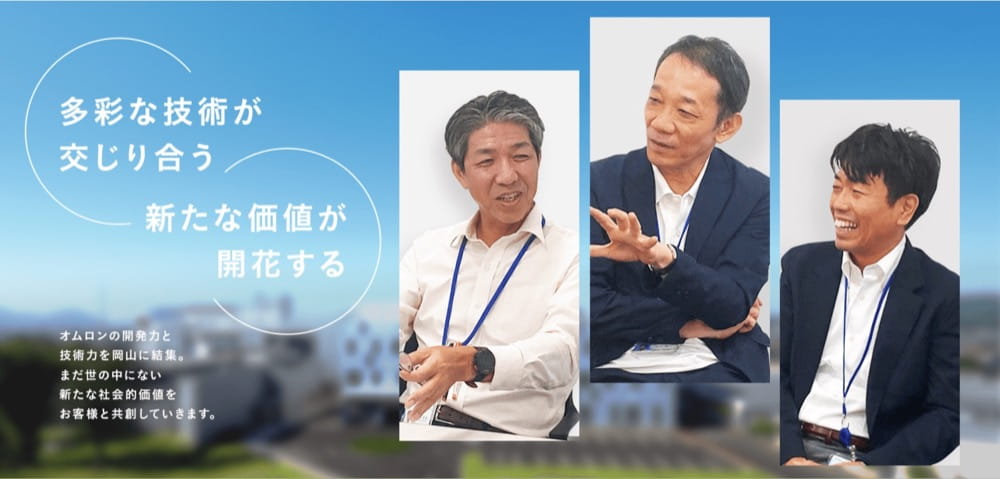
Click here if you are interested in our development trends
(Only Japanese)
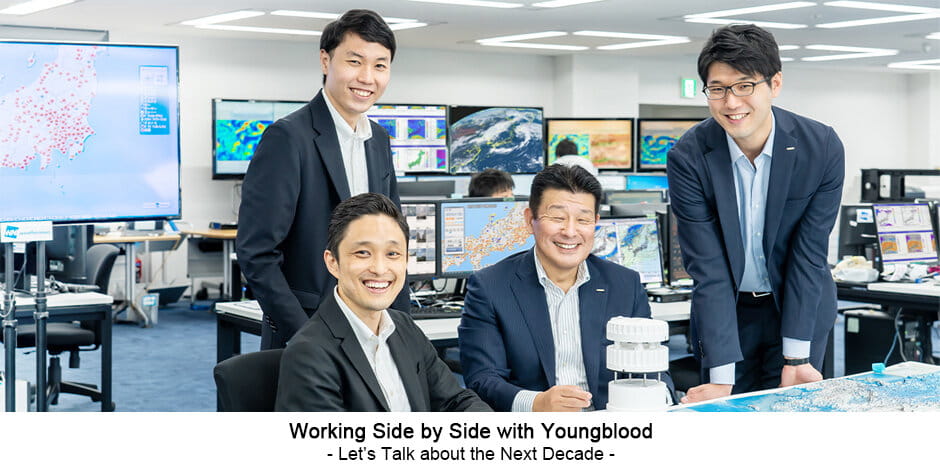
Click here to learn more about the interview between
Weathernews Inc. and OMRON
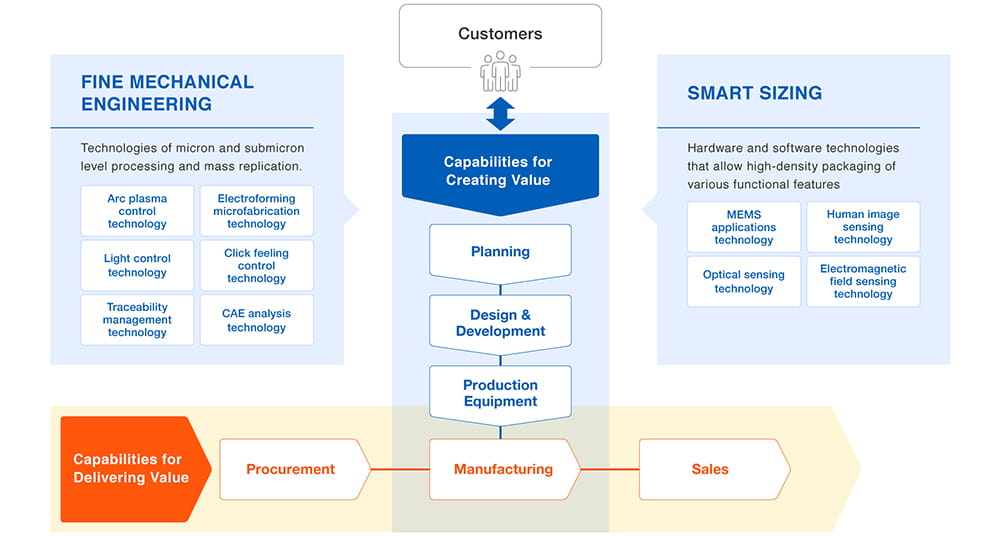
Click here if you are interested in our technology
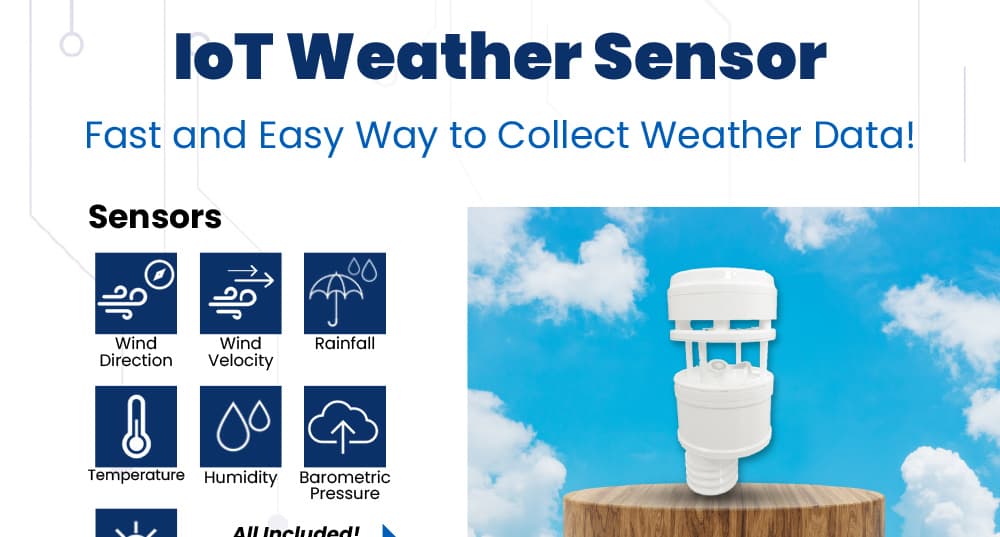
Click here to download OMRON IoT Weather Sensor PDF