Table of Contents
- What is the new concept of ultra-subminiature switches that realize "space saving" born from the needs of automotives?
- What is the ideal form of a switch that realizes "effective use of limited space"?
- Why not make the most of small gaps? Creating an ultra-subminiature switch that can be pressed from any angle
- The key to "space saving" was "rice ball".
- Rice ball that stands in the way (1): The conventional seal construction method can no longer be used.
- Rice ball that stands in the way (2): Circle or Oval? The overwhelmingly different difficulty level of sealing
- Rice ball that stands in the way (3): Rice ball with a big head prevents assembly.
- Innovative ideas not bound by conventional frameworks! This is the best solution for the structure to commercialize rice-ball shaped buttons!
- It is rewarding for developers to be recognized for their value by customers.
What is the new concept of ultra-subminiature switches that realize "space saving" born from the needs of automotives?
D2EW switch was originally developed for automotive door latches.
Switches for automotive door latches are strongly required to be "compact" as well as highly reliable as switches.
This is because it is essential for automotives to have thinner doors to provide more living space in the car, to pack in many features, and to improve fuel efficiency by reducing weight.
To achieve these goals, the switches and the peripheral mechanisms that operate the switches themselves must be made even smaller.
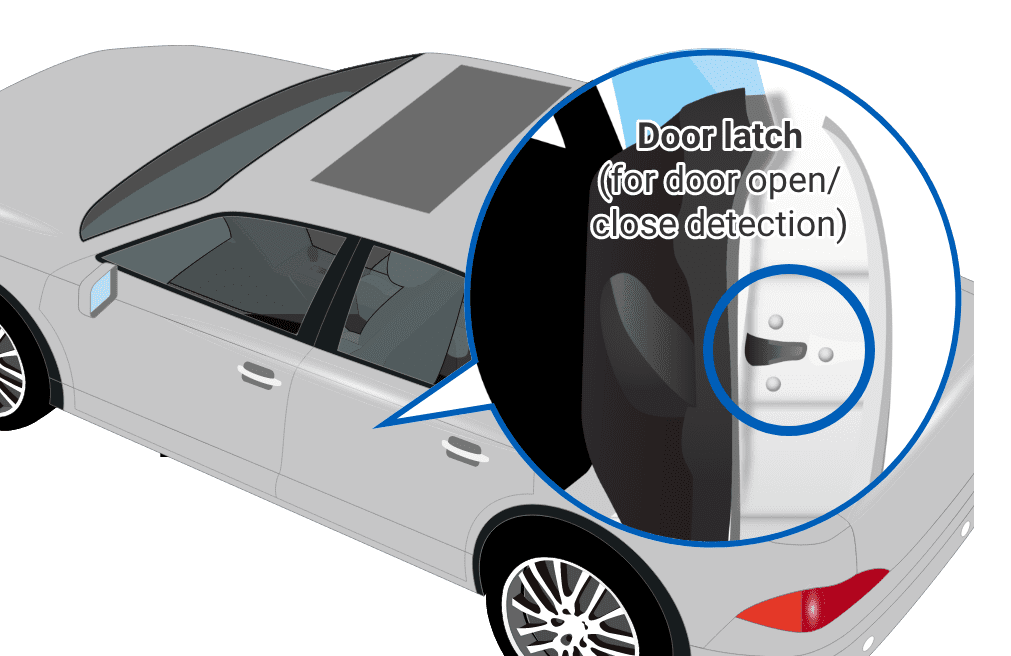

We have newly developed a compact sealed switch that can be operated in multiple directions and angles without a lever.
D2EW, which contributes to downsizing, space-saving design, and high-density mounting of switch peripheral parts by improving switch operability, is packed with various innovations made possible by OMRON's many years of experience in switch development.
Improved operability of switches also contributes to reduced production costs for the customer that installs them.
D2EW, which does not require a lever, allows the operating mechanism of the switch to be made smaller and simpler, leading to the reduction of materials used, the number of parts, production man-hours, and design man-hours on the customer side.
Switches are used in many devices around us. Similar problems with automotives occur with many devices. If you are anxious to save space, why not try D2EW first?
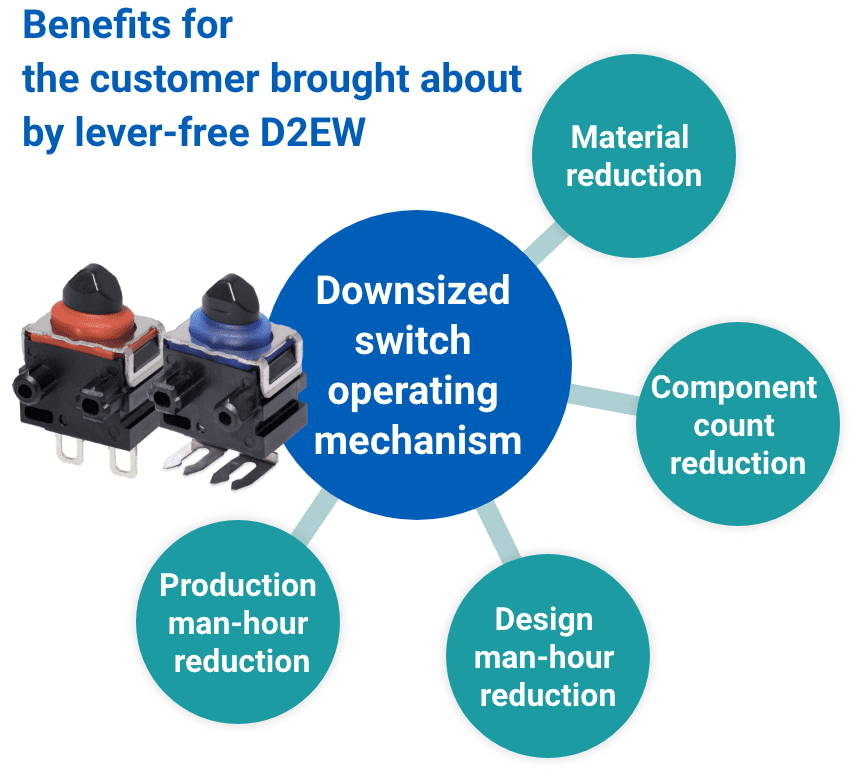
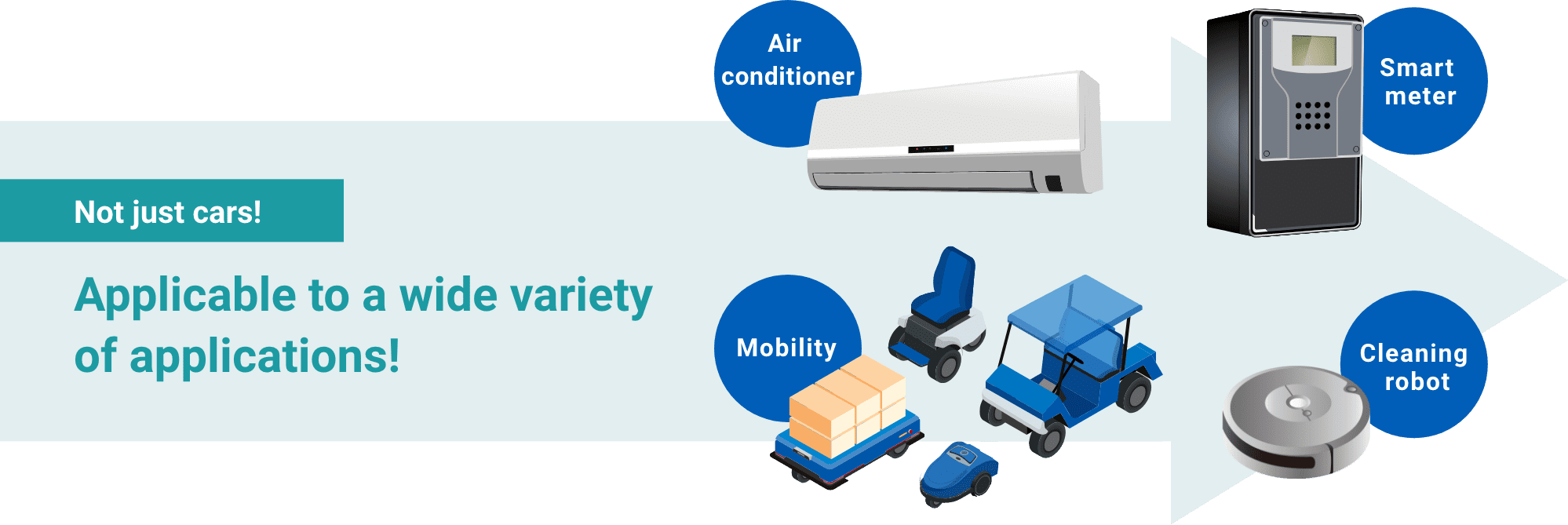
D2EW, born from automotive applications, has excellent environmental resistance and water resistance (equivalent to IP67).
D2EW is also useful for applications that require high functionality (high-density mounting) but have size limitations and are prone to water and condensation.
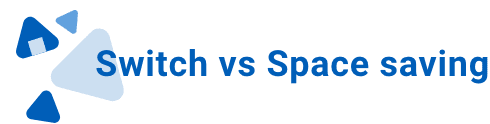
What is the ideal form of a switch that realizes "effective use of limited space"?
While new functions are being added to various devices one after another and smaller sizes are required, the number of components in devices is increasing rapidly. What is required of a switch to contribute to a customer's need to "maximize the effective use of limited product space"?
To achieve high-density mounting without increasing the size of the device and without wasting space, the following two points are important:
- (1) Small parts for pressing a switch
- (2) Small volume occupied by the switch itself
Meeting both of these requirements at the same time, however, is more difficult than you can imagine.
<Concerns arising from the operation method>
- Vertical operation
- Horizontal operation
(with lever) - Horizontal operation
(without lever) - Horizontal operation
(30° cam)
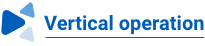

The easiest way to achieve (1) and (2) is simply to press from directly above, i.e., from the angle where the stroke (distance across the switch) is shortest. But designing a tiny switch with a stroke of only a few millimeters to be pressed vertically is not always easy.
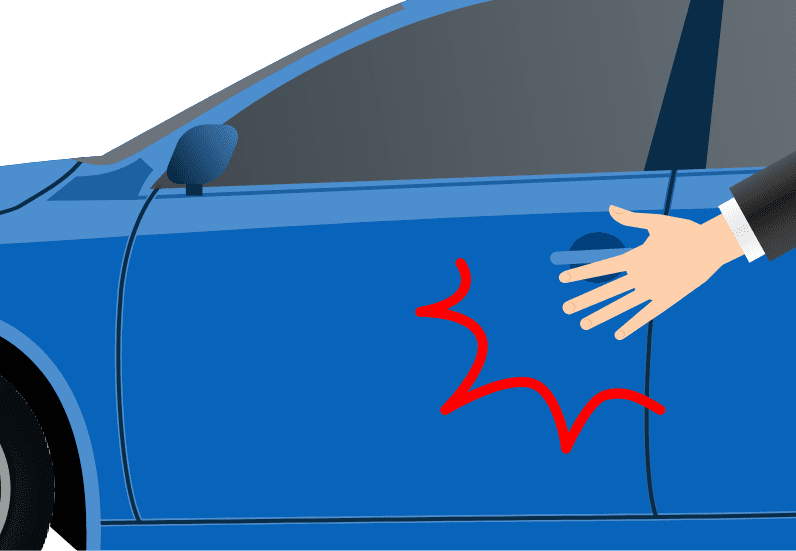
If the stroke is too small, an application in which people open and close with a lot of force will damage the switch unless it can be designed to absolutely stop after a few millimeters of pressure.
The fact that there is only a few millimeters for the pushbutton to drop all the way down means that pressing it any further will break the switch. To ensure that the product does not break, the customer must build a structure that absolutely stops the switch actuator within a few millimeters of contact with the pushbutton. This would be possible with a mouse or similar device that is operated with fingers. If you are designing a door for a car or other vehicle that opens and closes with great force, however, you may wonder, "How can I design it so that it moves only a few millimeters?"
In fact, for applications where large forces are applied, such as door latches, levers or other separate components are added to increase the stroke or change the direction of operation.


A switch with a lever enables horizontal operation, but the exclusive area of the switch itself becomes larger as the lever is installed.
And since the operating distance of the lever is greater than that of the switch itself, the size and travel space for the cam to push the lever in are larger, as are the gears and peripheral components used to move the cam. The use of a lever goes against the need for miniaturization and increases the size of not only the switch but also the device itself.


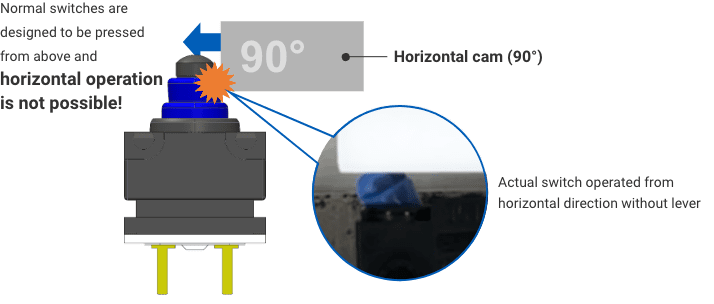
On the other hand, if you try to force the switch from the side without using a lever, of course the button will break.

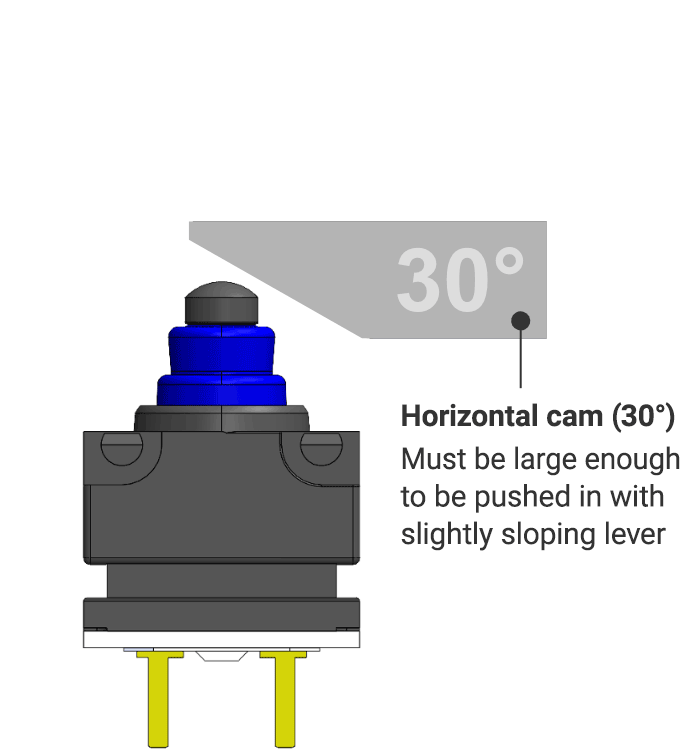
Push buttons are usually designed to be pressed from directly above. To operate with a horizontal cam without a lever, the switch actuator of the cam must be angled, and the maximum angle is about 30 degrees (depending on the model). The larger the angle, the more stress is placed on the pushbutton, shortening its life as a switch.
When operating with a horizontal cam, it can pass over the pushbutton even after the button is pushed all the way down, preventing excessive force from damaging the switch. However, if the horizontal cam is sloped, a larger space for the horizontal cam to move must be provided to push the button all the way down. This results in the customer's equipment becoming larger in size.

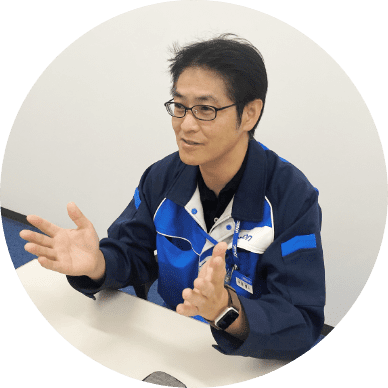
Hiroto Yonehara
Mobility Product Development Dept.
Business Management Division HQ
Ideally, both of the following should be achieved in order to reduce the size of the customer's equipment:
(1) Small parts for pressing a switch
(2) Small area occupied by the switch itself
But it is not easy to design a switch structure that can achieve both of these goals.
We had to rethink the switch concept from scratch which was a very high hurdle for development.

Why not make the most of small gaps?
Creating an ultra-subminiature switch that can be pressed from
any angle
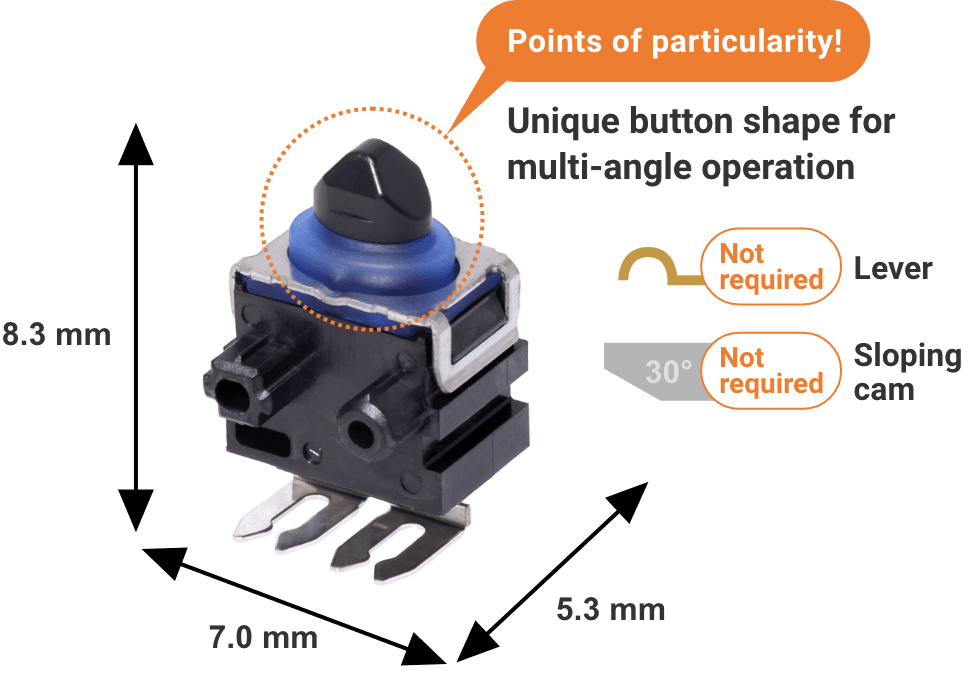
D2EW broke through this impregnable barrier.
D2EW has a unique push-button shape, newly conceived by OMRON, that allows it to be operated from a horizontal direction without a lever and without the need for a sloping horizontal cam. It can be operated not only horizontally but also from other angles. (See below)
Any application requires multi-functional and high-density mounting. D2EW, which can be operated from multiple angles, is an ultra-subminiature switch that can be easily integrated into small available spaces. Eliminating a lever also improves the cost performance of the switch itself.
Make the most of small gaps in your application with D2EW which allows for multi-angle operation.
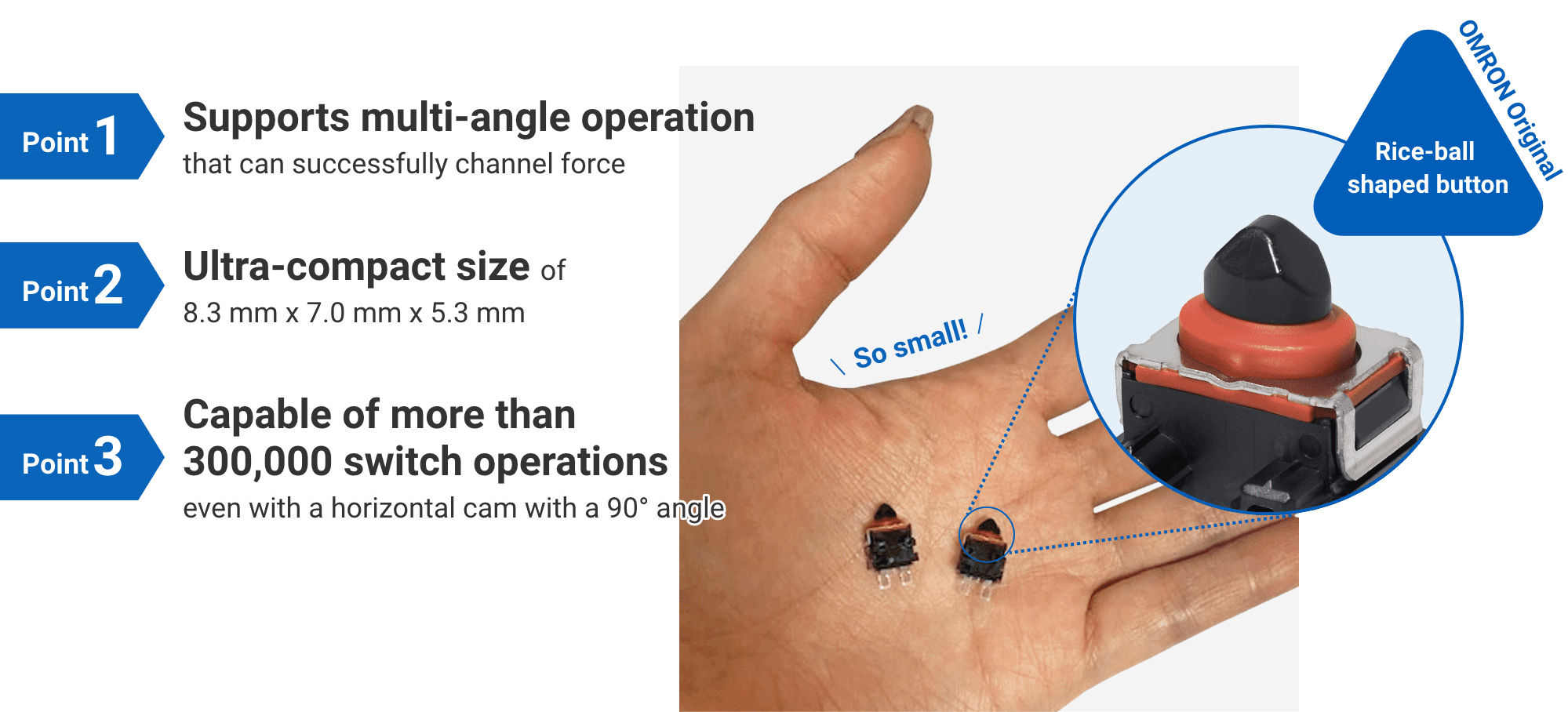


The key to overcoming this difficulty

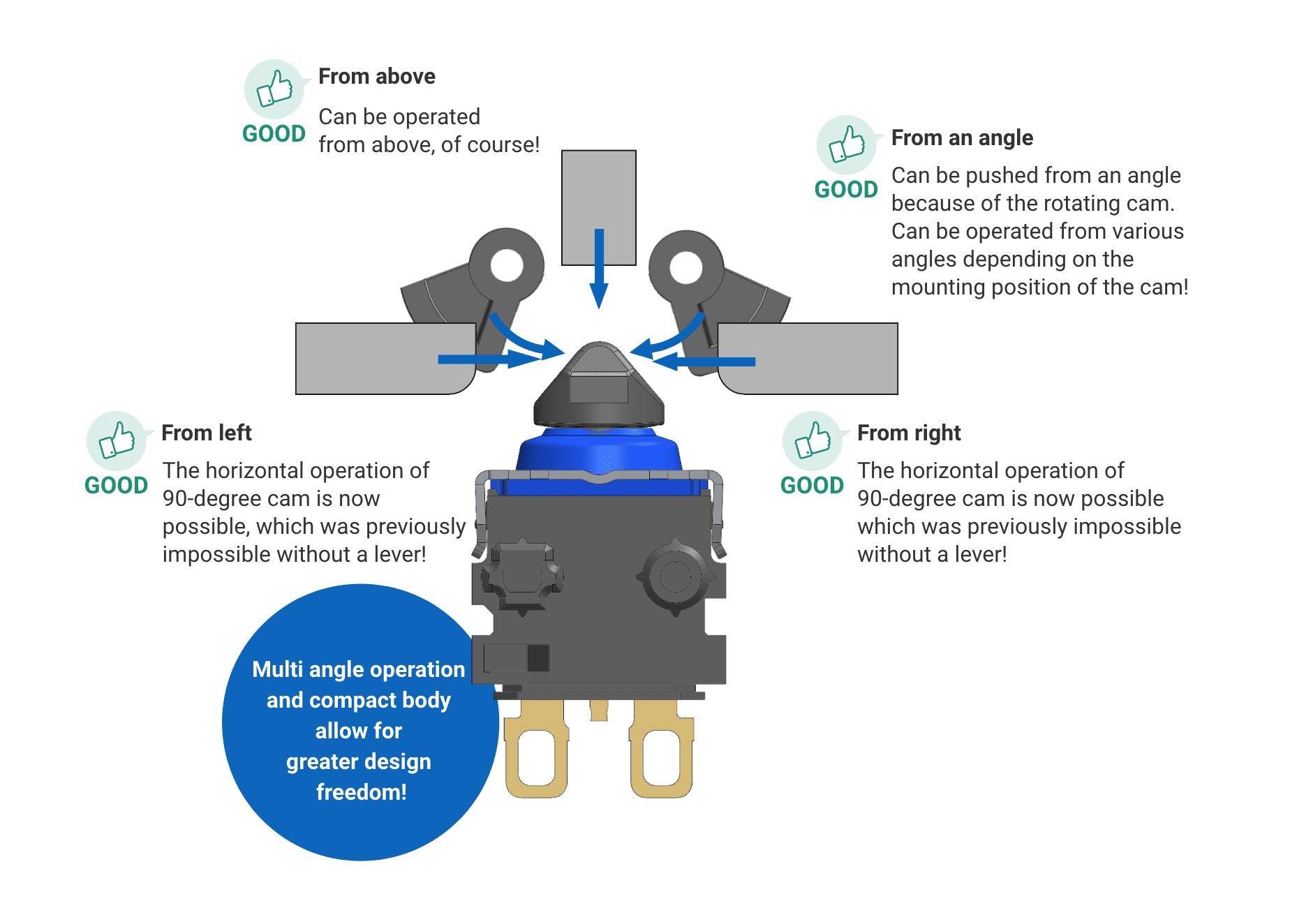
D2EW, which can be operated from multiple angles even without a lever, can open and close contacts horizontally with a stroke of only a few millimeters as well as when pressed from the vertical direction. Therefore, peripheral components such as cams and gears can be made much smaller, as they only need to be able to push the switch by a few millimeters.
The greatest feature of D2EW is its ability to contribute greatly to customers' design freedom and equipment miniaturization while maintaining cost-effectiveness.
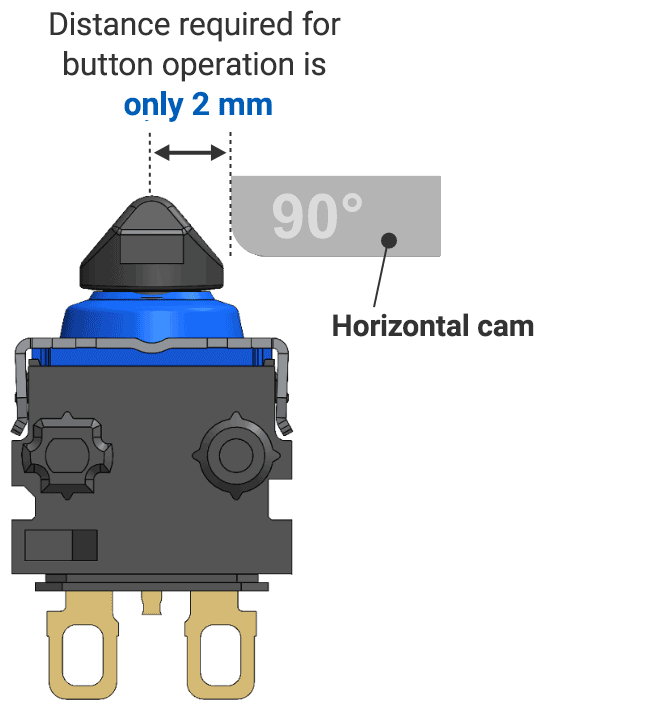

With Lever
VS
Without Lever
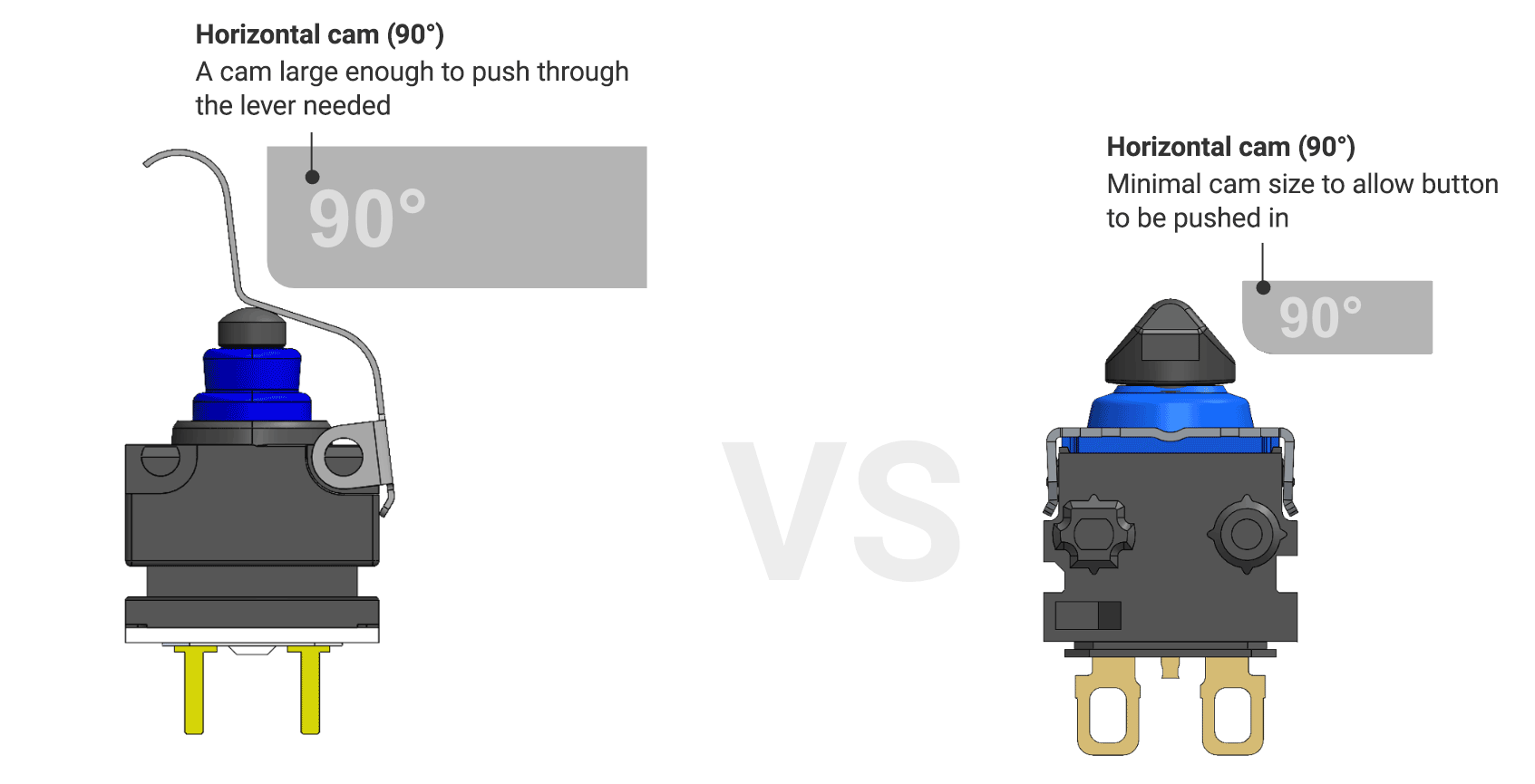
D2GW
The horizontal cam must be installed on the upper side as the switch has the lever which increases the space required.
It also increases the stroke distance of the horizontal cam until the pushbutton is fully pressed.
D2EW
No lever and minimal horizontal cam movement to push the button all the way through, contributing to space savings.

Without Lever(Round button)
VS
With Lever(Rice-ball shaped button)

D2GW
Conventional products require a tilt of less than 30 degrees to push the pushbutton from the side which increases the travel distance of the horizontal cam to push the button completely through and increases the size as well.
D2EW
No lever & shortest distance for horizontal operation
The switch can be operated even with a 90° cam, thus drastically reducing the travel distance of the cam. Super space-saving compared to switches of equivalent size without levers.

The key to "space saving" was "rice ball".
Before we could release D2EW, a product that achieves both "space saving" and "cost performance" which are the needs of our customers, there were many trials, tribulations, and struggles naturally.
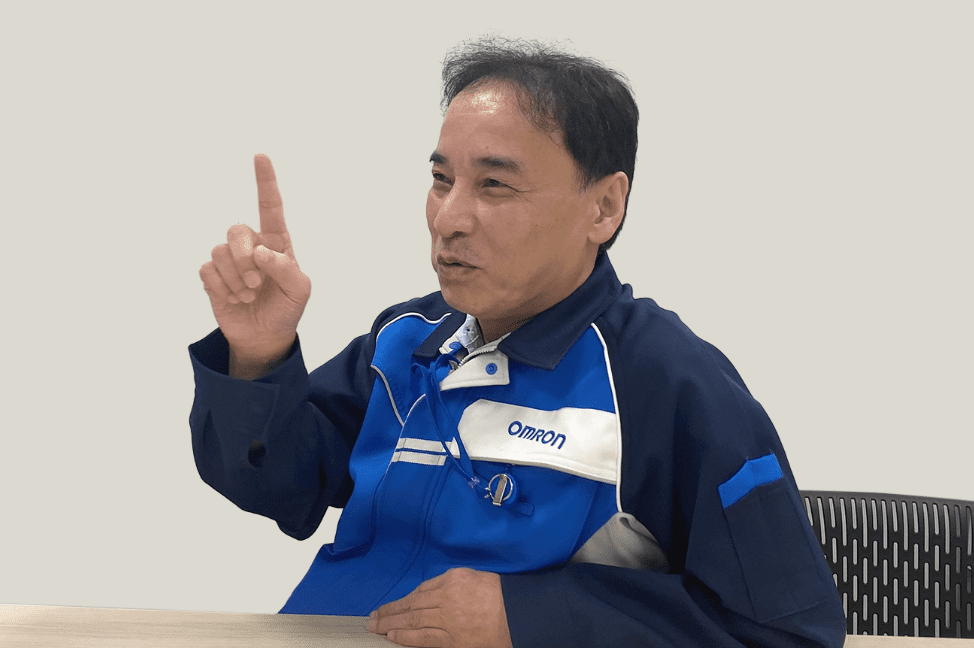
Kenji Shinohara
Mobility Product Development Dept.
Business Management Division HQ
The shape of the button was inevitably limited to a triangular one (rice-ball shape) in order to operate the switch horizontally, without using a lever. With the restriction of this rice-ball shape, we calculated the optimum angle of the slope of the button in order to realize a button shape that can be securely pressed from above and can be opened and closed with a minimum of stroke movement.
Button slope not steep
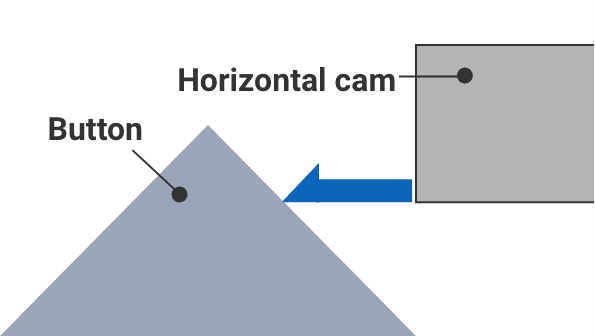
A distance from the side is required to push the button all the way through. The size of the unit (switch + cam) is larger because of the space required to move the horizontal cam.
Button slope too steep

The distance from the side to push the button all the way through is reduced, but if the slope of the button is too steep, the button will be damaged by the side impact.
D2EW

Triangular shape with a minimum stroke distance that is neither too gentle nor too steep.
In addition, the curved shape of the convex part was carefully designed to ensure that the button can be operated not only from the side, but also from the top.
Convex part is sharp
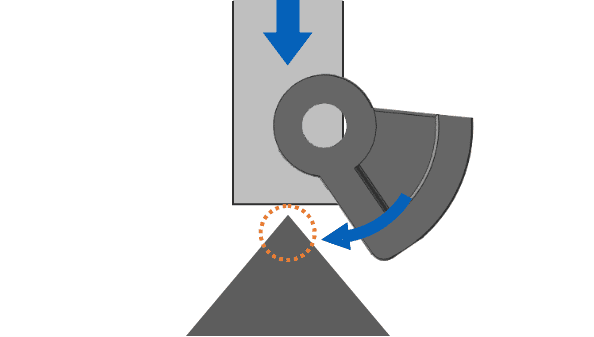
Unstable operation with sharp tip
D2EW
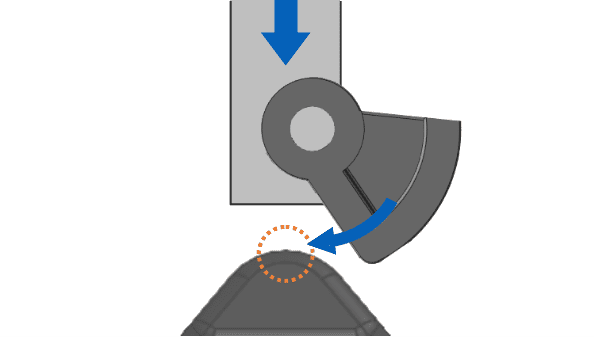
Optimized shape ensures stable operation
Rice ball that stands in the way (1): The conventional sealing
construction method can no longer be used.
However, although we were able to design a rice-ball-shaped pushbutton shape to save space, it was extremely difficult to ensure sufficient sealing performance (hermetic sealing performance) because of the original button shape, which was completely different from the conventional one, and this caused us a lot of headaches.
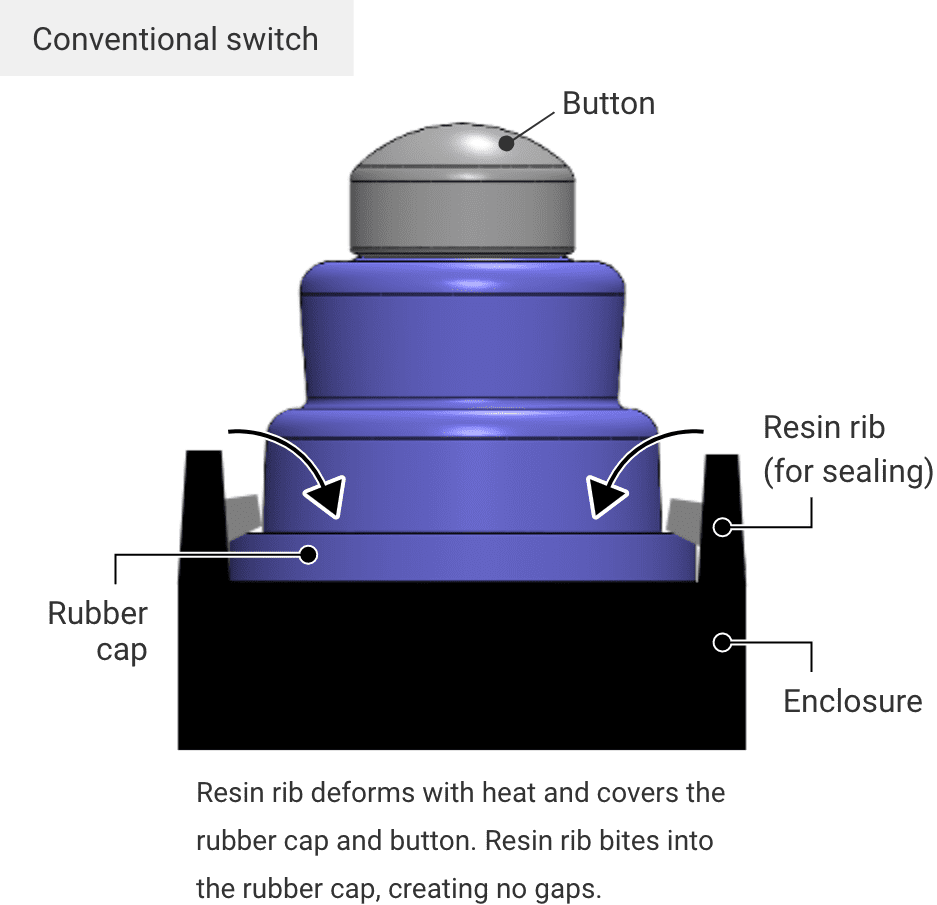
Conventional circular pushbuttons use a process called "heat caulking", in which resin rib is tipped toward the button and bites into the rubber cap to tighten the rubber cap.
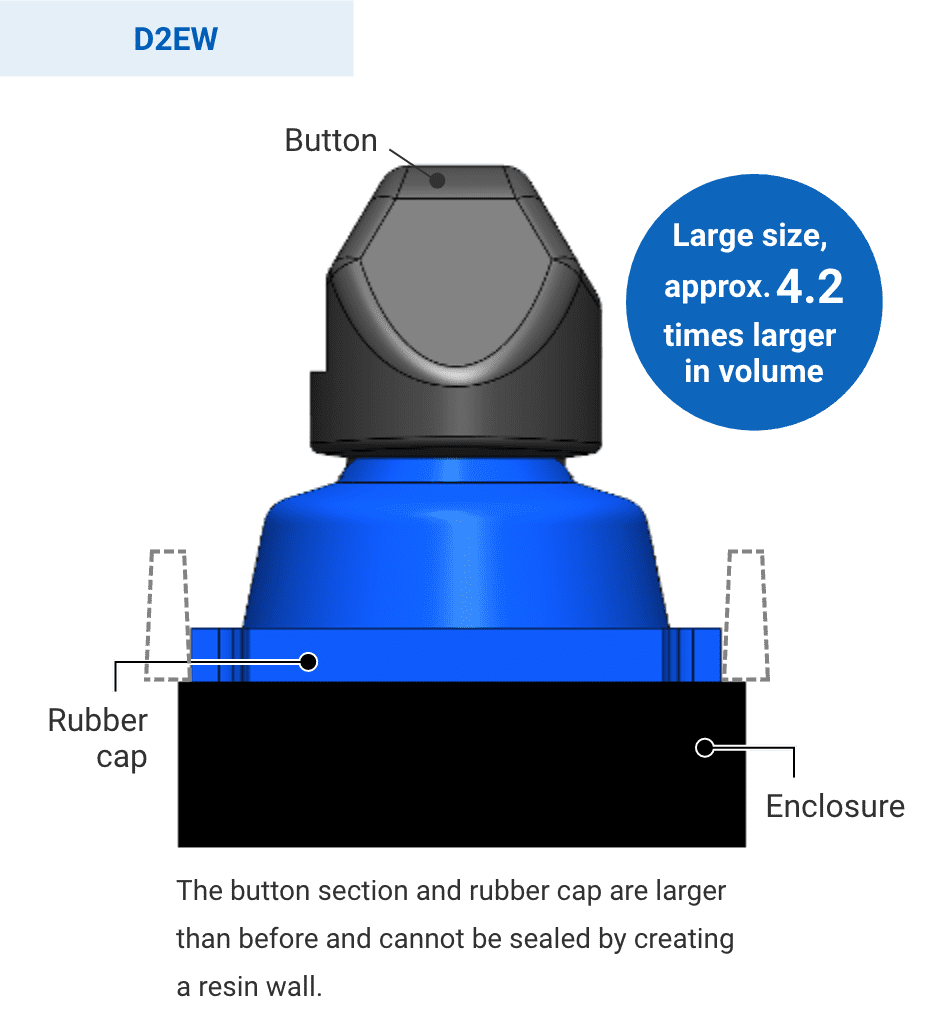
However, the pushbutton of D2EW is approximately 4.2 times larger in volume than the circular pushbutton, thereby increasing the size of the rubber cap itself. There was no space for a resin wall. For D2EW, we need to consider a new sealing method.
Therefore, we adopted a sealing structure to seal the case and rubber cap by "snap-fit", whereby the rubber cap is sandwiched between the case and cover with sufficient pressure to satisfy IP67. However, in sealing the pushbutton and rubber cap, it was the "rice-ball (oval shape)" that once again stood in the way.
Rice ball that stands in the way (2): Circle or Oval?
The overwhelmingly different difficulty level of sealing
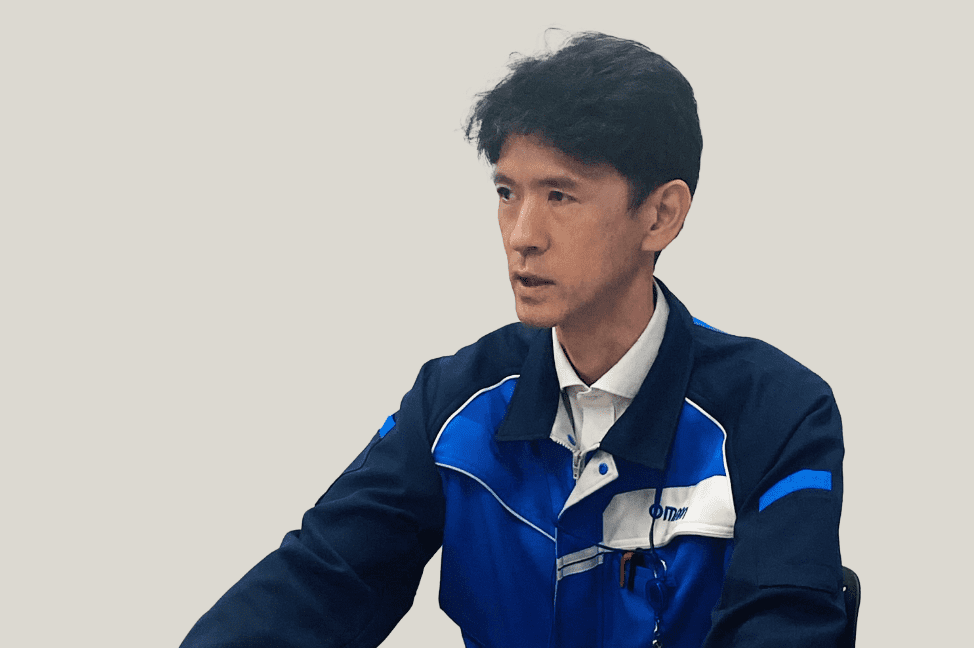
Hiroyuki Fujita
Mobility Product Development Dept.
Business Management Division HQ
When the button is circular, sealing performance could be ensured by applying pressure evenly from all directions. When the button part is oval (non-uniform shape) as in D2EW, however, there will inevitably be areas of strong tightness and those of weak tightness. Thus, we devised a shape that makes the shaft of the button as close to a circle as possible. In addition to adjusting the design of the button body shaft, it was also necessary to adjust the shape of the rubber cap and the thickness of the rubber to compensate for variations in load. As a result, in establishing a waterproof performance that meets IP67, we went through a trial-and-error process over several months, repeating design and analysis many times to arrive at the optimal shape.
D2EW's oval pushbutton
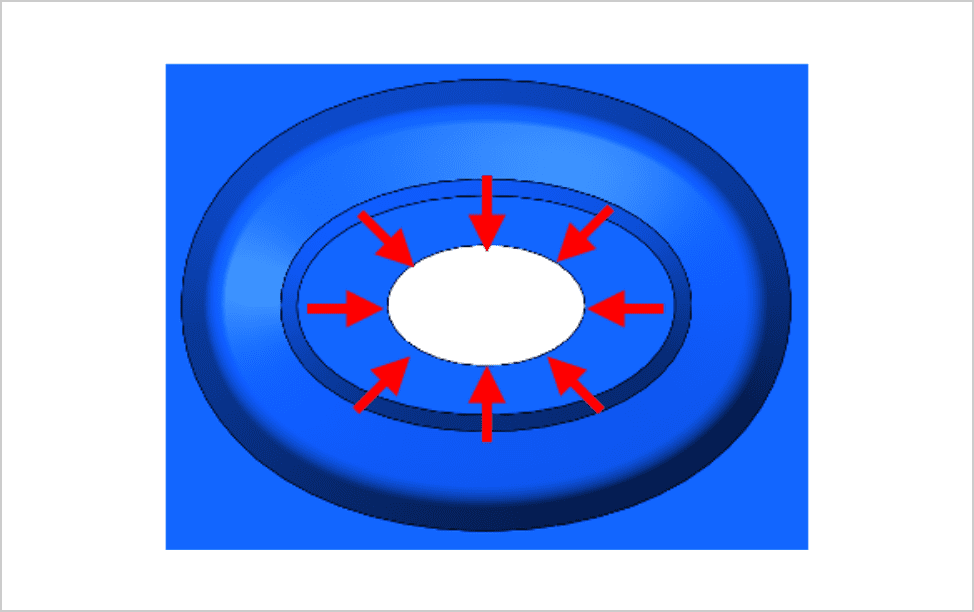
Oval shape requires ingenuity to tighten with even force
Conventional circular pushbutton

Circular shape makes it easy to tighten with even force
Rice ball that stands in the way (3): Rice ball with a big head prevents
assembly.
The newly developed "rice-ball" shaped pushbutton caused us a lot of trouble even in assembly.
The pushbutton, which is approximately 4.2 times larger in volume than conventional ones, could not be assembled using conventional methods, and new component shapes were essential for the enclosure as well.
D2EW's oval pushbutton
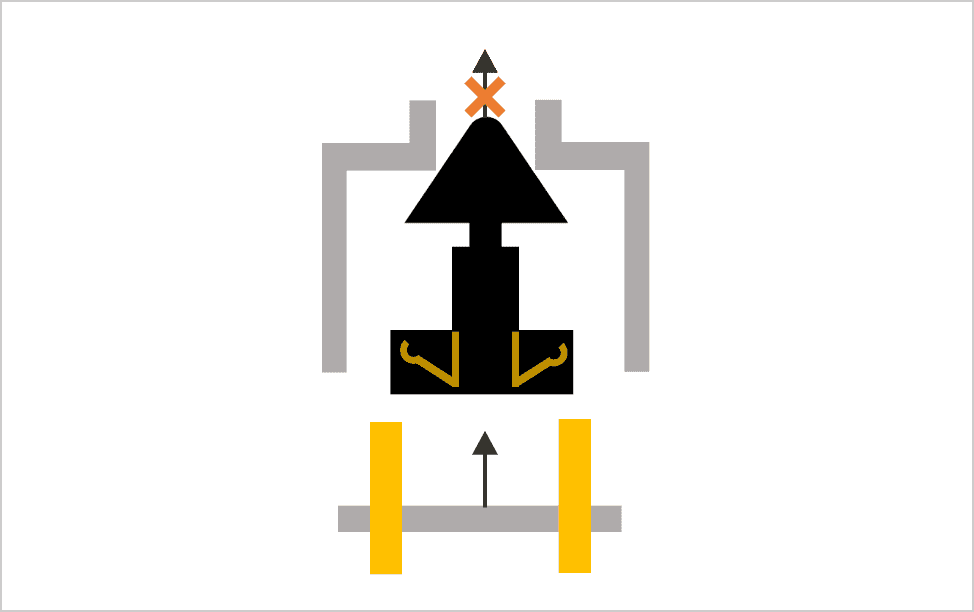
The rice-ball shaped pushbutton is too large to be inserted from the bottom as in the past.
Conventional circular pushbutton
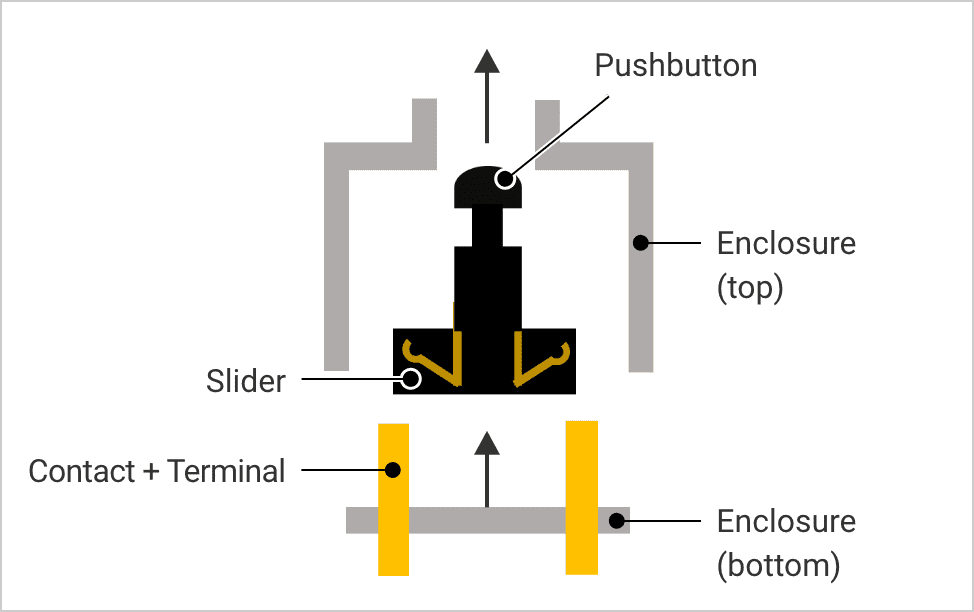
Pushbutton unit inserted from the bottom into the enclosure (top) due to the large slider.
New concept of enclosure, "bathtub" as we call it
Therefore, we adopted a "bathtub shape" for the enclosure and stacked the components from the top.
But to realize this bathtub shape by insert molding, in which metal and resin are integrated, a complex mold with a sliding structure is required. The lead frame (thin metal sheet) that serves as the contact point must be positioned precisely inside the bathtub shape as well.
With a simple structure that only requires stacking up components, "How can we open and close the switch?" "How can we connect the slider and terminal when we cannot use the conventional structure?" We could not come up with a good idea and racked our brains daily and redesigned the product many times. However, we shared the same thoughts as the entire team.

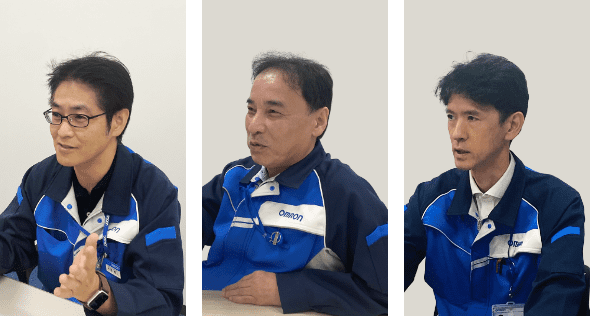
Everybody's thoughts
We will not compromise on anything.
We want to create a switch that makes our customers feel "This is the kind of switch we wanted".
Innovative idea not bound by conventional frameworks!
This is the best solution for the structure!

A slider is placed at the bottom, and contact surfaces are consolidated from two to one. (1) When the pushbutton is pressed, (2) the slider is pushed sideways by the button and the switch can open and close by the slider contacting the contact.
The best solution for a structure that achieves all three of these elements, "multi-angle operation without levers, miniaturization, and simplified assembly", is a completely new one that is not bound by the conventional method of opening and closing detection switches. D2EW has a pushbutton with a slider at its bottom, which slides sideways when the button is pressed, instead of a conventional pushbutton and a slider that move in unison. Furthermore, by integrating the contact surfaces into a single surface, we have achieved a structure that can be assembled using a simple construction method and can open and close the contact points with the smallest possible combination of components.
It is rewarding for developers to be recognized for their value
by customers.
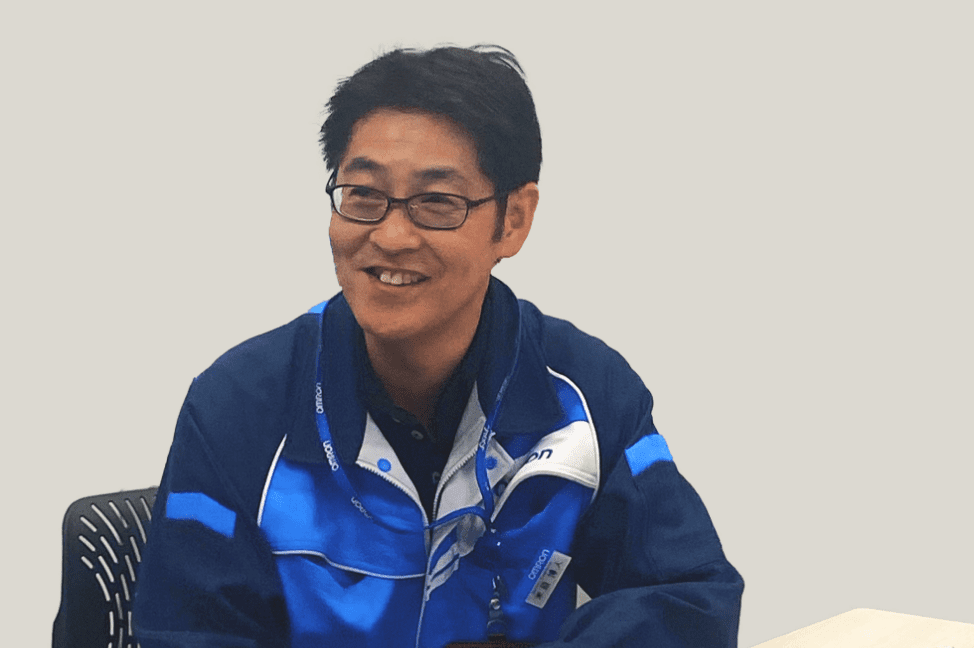
Hiroto Yonehara
Mobility Product Development Dept.
Business Management Division HQ
In fact, the idea of creating a "small switch that can be turned on and off at multiple angles without a lever" had been in the works for five years.
As a recent trend, for example, car door latches are increasingly getting new features, such as automatic door closing even when the door is half open. The more functions are added, the more components are needed for control. In order to maintain a small & slim design, high-density mounting is required, such that switches are packed into gaps without changing the latch size. Naturally, there may be cases where the switch must be pressed at an unreasonable angle.
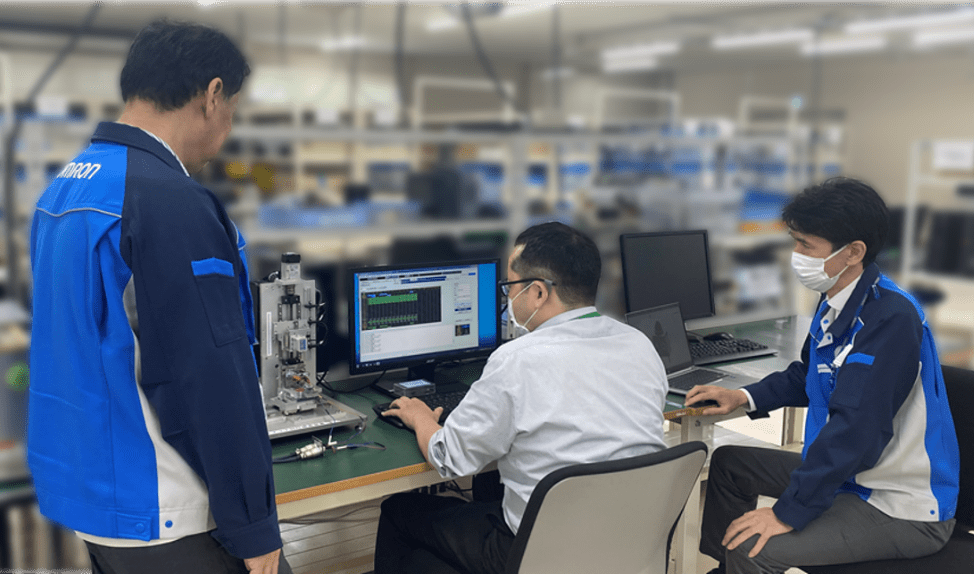
Over and over again, we created ideas, discussed them with customers, and revised the concepts, asking ourselves, "What kind of switches would be easy for customers to use?" We have long pursued the ideal form of a switch that can solve our customers' problems and issues, but have been unable to achieve it. This is because the conceptual design we developers envisioned was much more difficult than the product design, not to mention the process design and mold design.
Thanks to the uncompromising efforts and ingenuity of the process design and mold design members, we were able to overcome this high hurdle this time. There were many other challenges which were resolved through concurrent development by members of related departments. I believe that we were able to produce D2EW we have been pursuing because of the efforts of all the members involved in this product.
To be honest, we were also concerned about whether this product would really be accepted by customers. However, we are relieved to see that the D2EW concept has been very well received by our customers, just as we had hoped. In the future, we plan to add variations with different terminal shapes, different post shapes, and with lead wires.
In addition, we are currently developing D2EW-R, a switch with built-in resistor that can also detect disconnection failures.
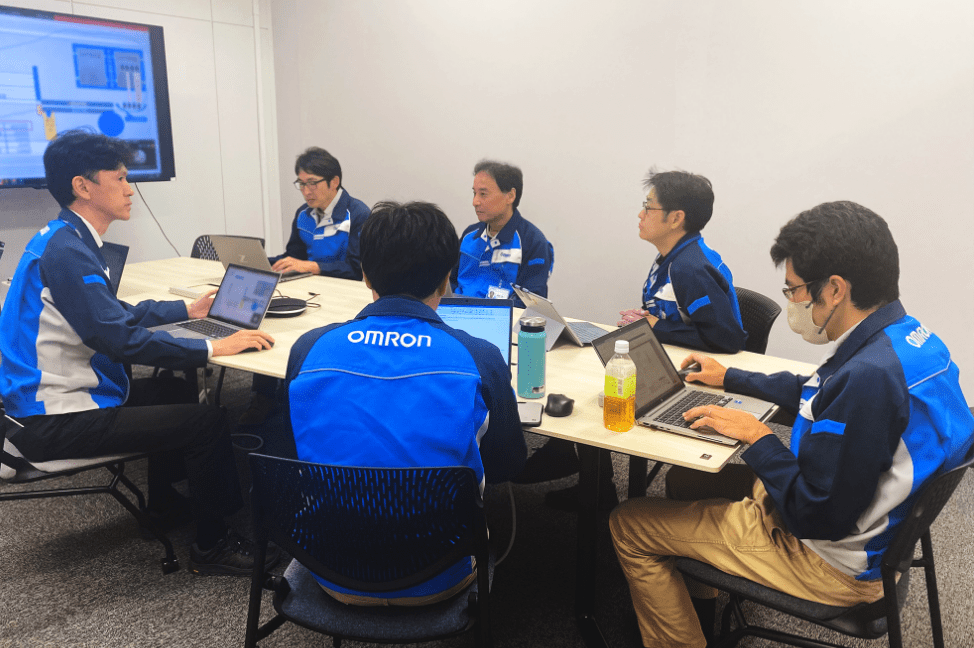
The moment when we truly feel a sense of accomplishment is not when we introduce a product to the market, but when a customer purchases it. It is proof that the customer has recognized the value of our products, not for our self-satisfaction. We will continue to realize high value-added products that satisfy our customers with flexible designs that are not bound by conventional ideas.
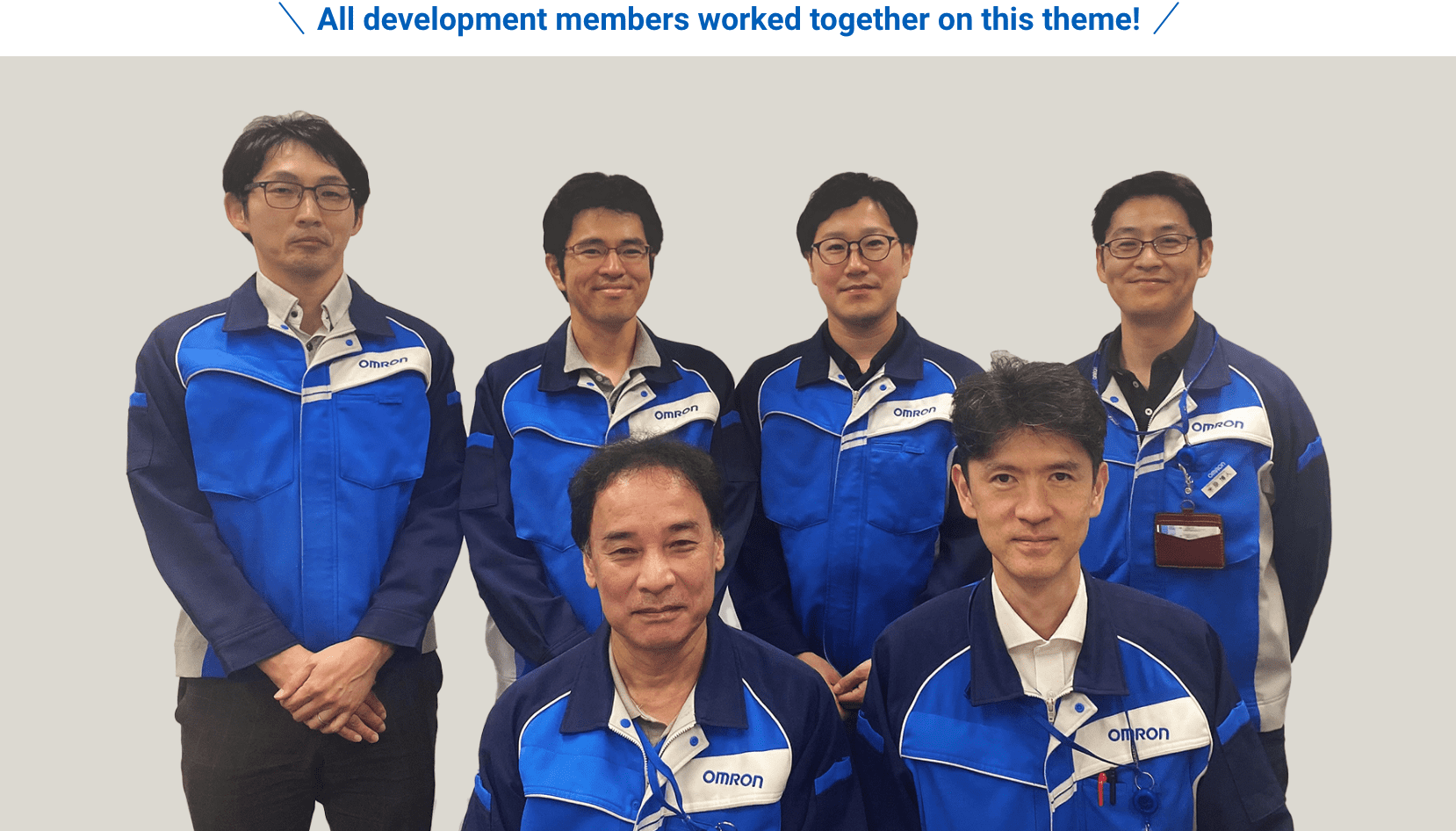
Mobility Product Development Dept.
Business Management Division HQ