Product Development in the New Normal
Information
Accelerating Digital Transformation in Manufacturing with AI x IoT x CAE
Hoofddorp, Netherlands, Tuesday, 9 February 2021– Recent years have seen companies across Japan adopting digital technology to transform their services and businesses (digital transformation, or "DX"). Following the announcement in September 2020 of the establishment of a government agency dedicated to the acceleration of DX, the shift towards a digital society is gathering momentum.
In the fields of factory automation and healthcare, OMRON is promoting DX to the manufacturing and medical fronts by providing services that utilize firsthand data, while proactively updating our digital processes to fit the latest standards. In this article we will present a pioneering attempt to advance our manufacturing DX through the use of CAE.
CAE Playing an Increasingly Important Role in Developing Products in the New Normal Era
Computer-aided engineering (CAE) refers to a body of design technologies for developing well-crafted and quality products with the fewest possible trials by conducting computer-based virtual prototyping and testing from the early stages of product development. CAE typically uses numerical-analysis software, which employs the finite element method (FEM) and other approaches, to analyze metrics such as stress, heat-transfer and fluids.
In the past, it took a multitude of arrangements to perform CAE analysis tasks, including pricy software, dedicated computers, a workstation and CAE-capable specialists. As such, the technique was used exclusively for the development of certain products, such as aircraft and automobiles. With improvements in the usability of hardware (computers, etc.) and software in recent years, however, CAE is finding broader applications as it is now easier to implement and anyone can handle it with a certain level of knowledge. Furthermore, advancements in the communication environment and security technology have made it possible to use CAE remotely. Even in extraordinary circumstances, when our ability to commute and freely move is limited due to the COVID-19 pandemic, CAE makes it possible for engineers to perform prototype studies and various tests in a virtual space, allowing product development to continue without interruptions, thus attracting attention from the perspective of business continuity planning as well.
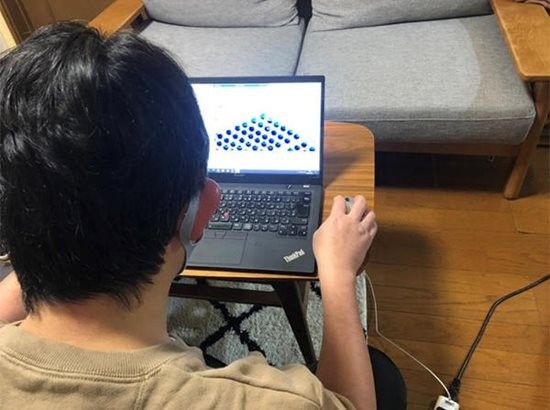
Verifying design by using CAE at home
CAE Forming an Integral Part of OMRON's Manufacturing
OMRON has long used CAE for the entire engineering chain from planning and designing to production, to efficiently manufacture quality products that help create a better society. In the early 1980s it was applied to product design, and by the mid-2000s it was used in the production process.
If you ask, "what makes OMRON's CAE different from other manufacturers?", the answer is, "It is driven by people on the production floor". For manufacturing excellence, OMRON believes that every designer and production engineer involved in the engineering chain should be able to choose which CAE approaches to use for their tasks. Now, CAE is being used in the design of all sorts of OMRON products and for the start-up of their production processes. For example, it is prominently used for verifying the characteristics and durability of tiny springs, which are hard to test-manufacture, and for assessing the possibility of a solder joint breaking when mounting electronic components onto a printed circuit board (PCB).

Simulating disc spring processing

Simulating crack propagation at IC component's solder joint
AI x CAE to Realize Defect-Free Designs
In 2020, OMRON took on a new challenge of "designing defect-free products" through the combination of automated design by AI and verification by CAE.
In this regard, we are working to reduce the number of defective products to virtually zero at the reflow soldering process*, where electronic components are mounted onto PCBs.
In the traditional reflow soldering process, after PCBs are designed, production engineers use their experience to set the temperature and velocity for the process over time as they check products. As this is the case, if arrangements of components or wiring patterns on PCBs are originally designed unbalanced, PCBs may be thermally deformed and warped, resulting in the breakage of the joint between a component and its solder, even if experienced production engineers have set optimal conditions.
To eliminate this technical bottleneck, OMRON programmed AI to learn from accumulated data on various conditions related to the process, so that the AI can automatically design the shape of PCBs, arrangements of components, and wiring patterns on PCBs. CAE is then used to verify the AI-designed data. Our goal is to bring about the optimal conditions for PCB designs and the reflow soldering process. At present, we are teaming up with a university to demonstrate the approach to "designing defect-free products", which combines designs by AI and verifications by CAE, for the mounting of several pieces of components onto PCBs. Going forward, we are planning to enhance practical utility of this approach by increasing the number of components to be mounted and the variety of wiring patterns on PCBs and to expand the scope of application of this technique to include designs of housing and other mechanisms.
HR Development Is the Key to Expanding the Scope of Application of CAE
"You have to remember that AI and CAE are just mere tools - nothing more and nothing less. Even if you take advantage of AI and CAE to efficiently produce designs that you think are practical, the responsibility for manufacturing the products thus designed rests with people and companies. Suppose a product automatically designed by AI and CAE turns out to be defective. Can you claim, 'AI is to blame for producing such and such results' or 'CAE gave me such an answer'? No, you cannot, because designers and production engineers are required to understand how AI and CAE 'think' so that they can account for the results that such tools have derived. I believe that all engineers working at a manufacturing company, which is socially responsible, must be accountable in this way. This is why continuing to develop human resources is so important", says Hiroshi Okada of the Global Procurement & Quality Management HQ, which promotes the use of CAE within OMRON.
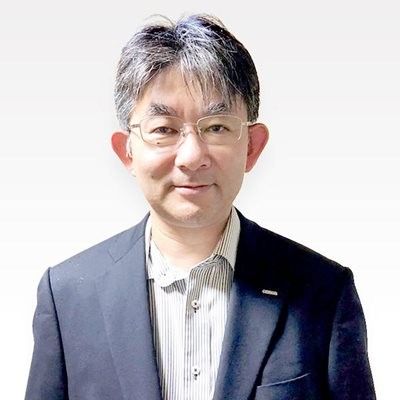
Okada is focusing on the development of human resources who know CAE inside out. To this end, he teaches mechanical engineering to designers and production engineers and shows them how to use CAE software. At such internal workshops, he uses concrete examples of products as he believes that engineers need to accumulate firsthand experiences, on top of know-how on the use of design and production engineering, computational dynamics and software knowledge. He also makes it a point to discuss findings with those concerned with products in question at each stage of the process (planning, CAE analysis, review of findings). This is because he wants everyone involved to teach and learn the CAE design method among themselves and enhance their motivation.
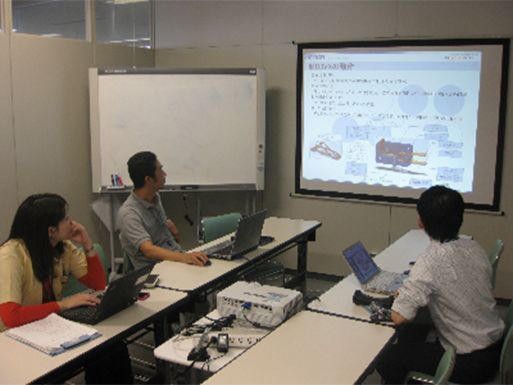
AI x IoT x CAE to Integrate the Engineering Chain and the Supply Chain
Okada shared his vision of how CAE can be better utilized in the future: "I think it would be most effective if we combine AI, IoT, and CAE to integrate the engineering chain and the supply chain from planning, designing and procurement to production, and manage the two chains as one".
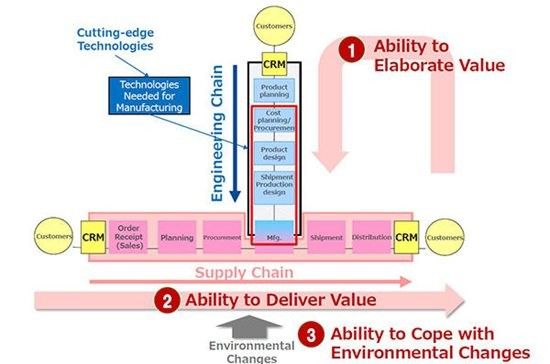
"If, for example, we use AI to 'analyze market needs, materials, and manufacturing methods to offer ideas for effective product development', 'discover a rule from a yet-to-be-defined phenomena and incorporate its logic into CAE', 'extract the logic out of experiences and intuitions of experienced engineers to hand down their expertise and skills' and 'quantify human sensations to improve sensory quality evaluation', we can expand the breadth of what CAE can do through integration with AI and IoT. By realizing these tasks one by one, I believe that we can promptly provide products that meet diverse market needs without going through prototype studies or producing defective units, thus eliminating waste. I also believe that producing quality and user-friendly products without generating waste will be one of the sources of business competitiveness going forward. With this in mind, we are hoping to encourage everyone to use design methods that combine AI and CAE even more consistently", Okada concluded.
*Reflow soldering is a process in which a printed circuit board with electronic components is heated for soldering. Solder cream (powder metal solder wrapped with a thick medium called flux [soldering aid]) is applied onto a circuit board on which a wiring pattern is printed. The solder cream is applied with a brush called a squeegee (a metal mask is used to prevent solder cream from being applied where it shouldn't be). After components are mounted by an automatic machine, etc., the PCB is heated in the reflow oven in several stages with hot air ("reflow profile") to melt the solder paste.
Download PDF version here.