Ultra-low contact resistance of 0.2 mΩ achieved by thorough control of foreign materials
Interview the People in Charge of Quality for Our High-Capacity Power Relay G9KA
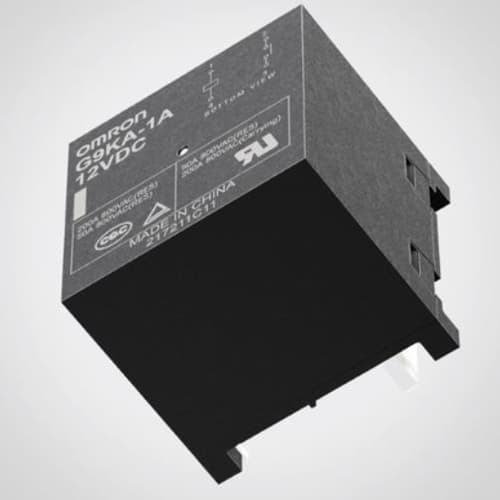
The commercialization of the G9KA, the industry's first* power relay with an ultra-low contact resistance of 0.2 mΩ, was not only a challenge to develop but also uncharted territory in terms of quality. We would like to introduce the individuals in charge of quality for the high capacitance power relay, G9KA. They worked on the mass production of products satisfying 0.2 mΩ by thorough foreign material control based on their strong belief of "never making or releasing defective products".
* According to OMRON's research in July 2021

A precision device that converts electricity produced by solar panels into electricity that can be used in homes, buildings, and factories.
Power conditioners, the main application of the G9KA, are devices in which reducing loss and heat generation is an important factor in improving product efficiency and reducing costs. The relays for them must have low contact resistance. One of the major challenges in achieving G9KA's greatest value, ultra-low contact resistance of 0.2 mΩ, is foreign materials on the contacts. Having foreign materials on the contacts will increase resistance because they obstruct the path of the current.
While conventional relays have an initial contact resistance (rated value) of 100 mΩ, G9KA has an initial contact resistance of only 0.2 mΩ. Even after electrical durability testing, the contact resistance value remains below 0.3 mΩ (reference value), showing a capability value much lower than the initial value of conventional relays. In order to provide our customers with the product value of "ultra-low contact resistance" with stable and high quality mass-produced products, in addition to the technical innovations in development, we established a new management process while repeatedly examining and verifying this unknown 0.2 mΩ range.
Thoroughly "taking action on the occurrence" and "removal" of foreign materials
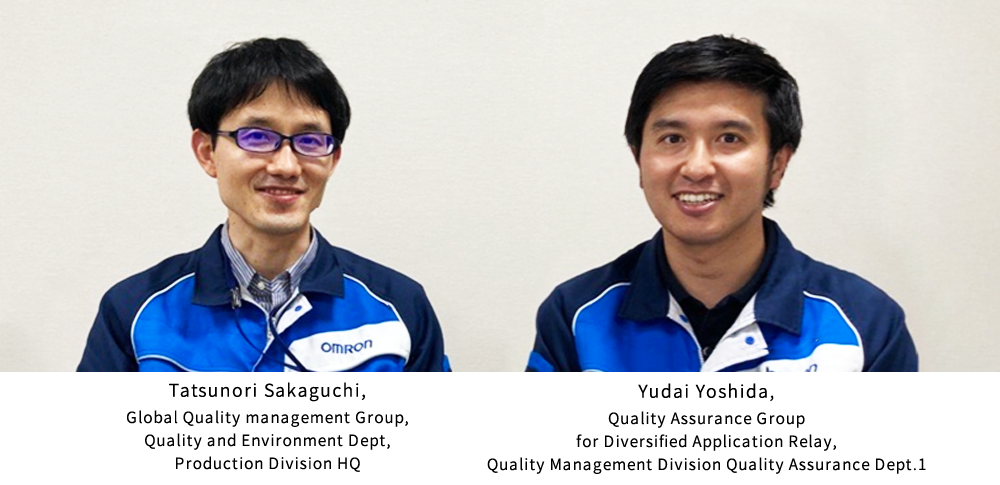
There are two main ways to manage foreign materials: "taking action when it occurs" and “removing” them. Basically, the "occurrence" of foreign materials cannot be reduced to zero. When terminals are press-fitted into a base, for example, a metal terminal is pressed into a plastic component, which is inevitably scraped by the metal, resulting in plastic debris. Therefore, we usually devise the shapes and materials of components during the design process in order to minimize the generation of foreign materials as much as possible.
Even when the utmost efforts are taken to prevent the generation of foreign materials, it is not possible to reduce their generation to zero. Foreign materials that inevitably occur are dealt with by "removal (dust removal)". Air is blown to areas prone to the occurrence of foreign materials such as press-fit locations to blow away any foreign material. This is done at each step of the component assembly process. We are very thorough in removing any foreign material that is generated on the spot. Furthermore, even if foreign material is not completely removed during the assembly process of each component, air is blown one last time to carefully remove it (final dust removal) to ensure that no foreign material remains on the contact surfaces.
Facing the big wall of being one of the best in the industry*
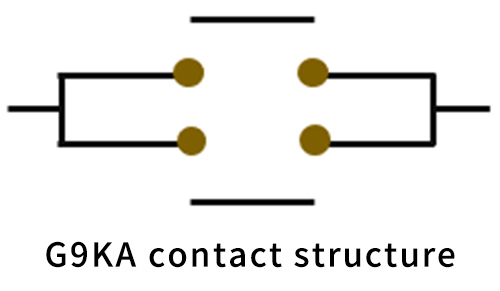

One of the factors contributing to the difficulty of quality control for the G9KA is the complexity of its structure. There are 8 contact points on G9KA. Even if one foreign material is caught in a contact point, it is difficult to detect it by normal continuity testing because electric current can flow on another contact point. Naturally, a foreign material on a contact will increase the contact resistance, making it impossible to achieve the required specification of 0.2 mΩ initial contact resistance. Therefore, with regard to G9KA, we needed the means to raise the detection power of foreign materials one more step, which "absolutely satisfies 0.2 mΩ".
Therefore, we introduced two new processes: "filter trap" and "contact point cleaning".
* According to OMRON's research in July 2021
Thoroughly controlling foreign materials by size and type
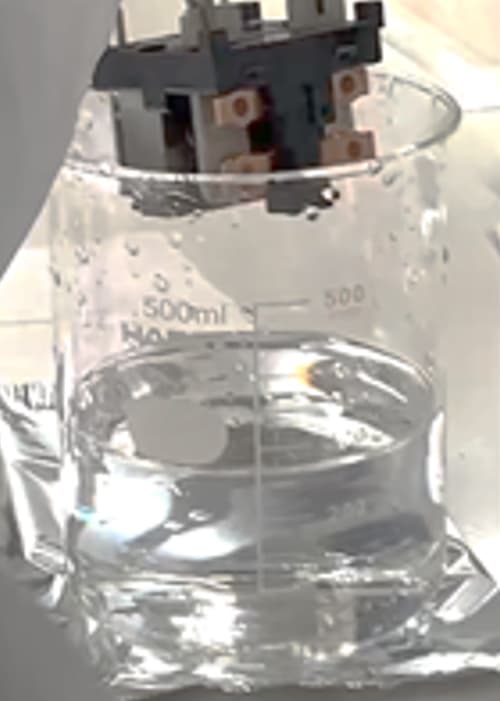
A filter trap is a method of foreign material control in which products are placed in clean water and shaken to collect and count the foreign materials that come out.
Filter traps are a common technique, usually used to confirm trends in the amount of foreign materials. Whenever there is an increase in the occurrence of foreign materials, there is always a cause or point of change somewhere. For this reason, we regularly accumulate data on the amount of foreign materials in our filter traps as an indicator of changes in their amount and the criteria for judgment.
For G9KA, however, we use the filter traps with even finer criteria for each lot. The major difference from conventional filter traps is the clear control standard value of "how many foreign objects of which type and size are present on the contact point when the contact resistance of 0.2 mΩ is not satisfied". We created this standard by actually placing a foreign object on the contact point and measuring the contact resistance, which is a steady and tedious process.
Using this standard, the number of each type of foreign material is counted for each lot and thoroughly controlled to ensure that no defects are caused by foreign materials.
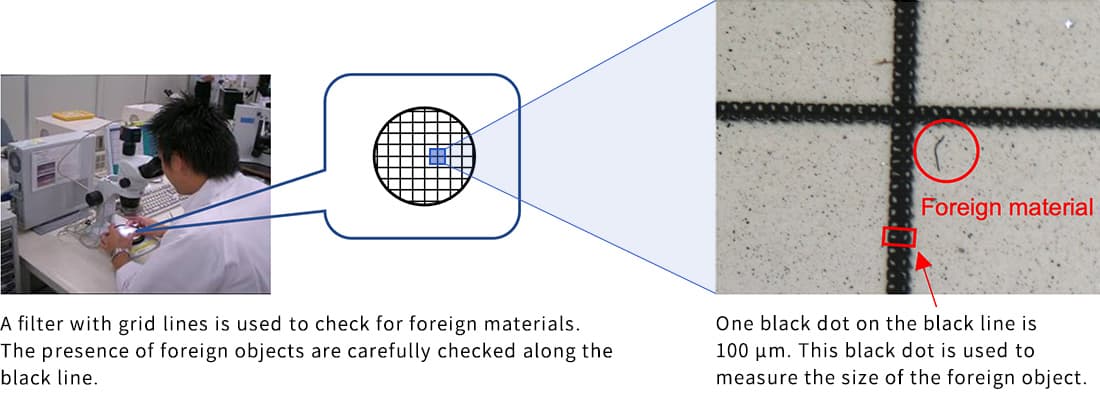
Furthermore, thorough removal of even foreign material that cannot be seen
A "foreign material" is not necessarily just something visible. Microscopic organic materials, sometimes invisible to the eye, may also adhere to the contacts. In the ultra-low contact resistance range of 0.2 mΩ, these must naturally be considered as one of the factors that increase contact resistance. Therefore, the processes for G9KA incorporate contact cleaning to remove these organic materials from the contacts.
Visible foreign materials are removed by "filter traps" and invisible organic materials are removed by "contact point cleaning", thoroughly eliminating elements of concern that stand in the way of realizing ultra-low contact resistance, the greatest value of G9KA.

To maintain a matter of course that "no quality defects are a matter of course"

Tatsunori Sakaguchi,
Global Quality management Group,
Quality and Environment Dept,
Production Division HQ
While conventional power relays have a contact resistance rating of 100 mΩ, G9KA has that of 0.2 mΩ or less, which is a product with a completely different and stricter standard than any other product I have been involved with. Everything was new and difficult to control at every step, and the conventional norm did not apply. That was the G9KA.
In response to problems that could not be anticipated using only the conventional wisdom of existing products, in process control, we worked tirelessly to identify potential defects, examine countermeasures, and eliminate them, while cooperating with related departments to create the current "defect-free process".
I believe that we, the quality control department, should do our utmost to ensure that "no quality defects are a matter of course", and that they continue to be something ordinary for our customers. I would like to continue to use my experience with G9KA to improve the quality of new products and contribute to customer satisfaction.
From "quality as a matter of course" to quality as a strength
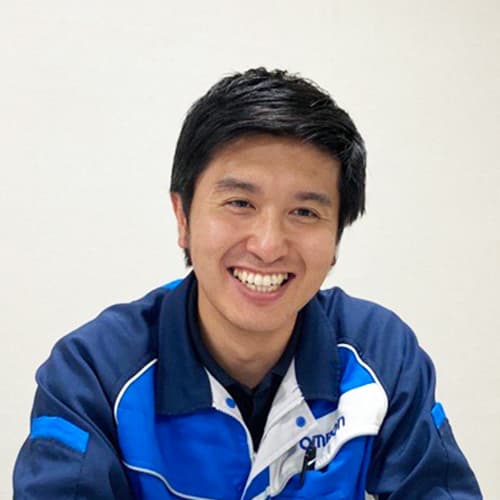
Yudai Yoshida,
Quality Assurance Group for Diversified Application Relay,
Quality Management Division Quality Assurance Dept.1
In the development of G9KA, achieving the industry's first* ultra-low contact resistance of 0.2 mΩ was a challenging and unprecedented target, even within our company.
It is obvious that product specifications are the quality assurance we promise our customers. The role of the quality assurance department in new product development is how to manage and guarantee the specifications in the process, how to deliver the product to the customer, and how to ensure that the customer does not experience any problems during use.
Frankly speaking, at the beginning of development, I was troubled by the level of difficulty and how to guarantee the quality, but the fact that customers are demanding 0.2 mΩ of contact resistance, which would become a value and an advantage of G9KA, was unique to new product development and motivated me.
G9KA is a product sold to customers with low contact resistance of 0.2 mΩ as its value. With it’s many evaluations and verifications we have conducted and the trial-and-error process of how to ensure this, I believe that we are able to confidently manage our products in order to deliver value to our customers without fail. We are proud to say that no defects will occur.
In addition, G9KA is the first new product I was involved with and I have become deeply attached to it.
I look forward to hearing from our customers that G9KA has become a part of their own product value.
* According to OMRON's research in July 2021