Confronting the major social issue of "carbon neutrality" with a small electronic component "relay"!
Challenge to industry's top class* ultra-low contact resistance of 0.2mΩ
* As of October 2022
As you all know, abnormal weather caused by global warming is no longer simply "climate change" but is also said to be a "climate crisis" that shakes the survival basis for all living things on earth. In order to prevent the "climate crisis" caused by global warming, there is a growing movement in the world today to accelerate the spread of clean energy with the goal of "achieving carbon neutrality by 2050".
With the desire to "solve the social issue" through our business, we focused on solar power generation systems, which are indispensable for the spread of renewable energy, and developed the power relay G9KA.

Table of contents
- The key was to reduce "heat generation"
- Surprising numerical value; 0.2mΩ
- With the completely new, unknown structure, we became spiritually broken many times but giving up was not an option
- The 0.2mΩ cliff that we all faced in "concurrent development"
- What we valued was "dialogue" and "unity"
- Ceaseless challenges led to great results
The key was to reduce "heat generation"

Ayaka Miyake
Fine Mechanical PD 1
High Power Switching Technology Gr.
Business Management Division HQ
As we visited many customers to see if there was anything we could do in the electronic components business, we came to realize that the "heat" generated by power generation equipment was a major barrier to the spread of clean energy. The role of relays is to help ensure the safe and reliable use of power generation equipment by switching the power conditioner on and off. However, relays, which we specialize in, were a major source of heat in the equipment.
The higher the capacity, the more heat the equipment generates. If the current doubles due to higher capacity, the amount of heat generated will quadruple. Since heat generation shortens the life of equipment, cooling mechanisms such as fans and heat sinks are required. The incorporation of cooling mechanisms leads to larger equipment and higher costs, resulting in the exact opposite of what society needs. In addition, there was a demand for a "further increase in power generation efficiency over the current situation," as well as "higher capacity," which conflicts with the need for low heat generation. To address the issue of "heat generation" caused by high capacity, the development of a relay with low heat generation can realize energy saving and energy efficiency improvement of the equipment itself. Convinced that confronting the issue of "heat generation" with relays, which are small components, would be a major step toward solving the social issue and contributing to carbon neutrality, we launched a project to develop a new relay product.
The G9KA was created as a product that combines two contradictory features, "ultra-low contact resistance" and "high capacity". These two performances are the greatest value of the G9KA, which has achieved the industry's top class* "ultra-low contact resistance of 0.2mΩ or less".
In order to realize a high capacity of 200A, low heat generation, and a compact size, the G9KA has achieved a structure and specifications that are unprecedented for an OMRON relay.
* As of October 2022

Surprising numerical value; 0.2mΩ
The "contact resistance of 0.2mΩ" was a numerical value that emerged from interviews with many customers. Since the temperature inside the equipment can reach up to 85°C when used in desert areas, it became apparent that the PCB needed to be heat resistant to 110°C or less. To meet this goal without a cooling mechanism, relays, which are one of the largest heat sources in the equipment, must be kept at a slight temperature of "25°C or less". To achieve this, the contact resistance of the relay had to be "0.2mΩ or less". When we heard the words "0.2mΩ or less", all of us who specialize in relay development were at a loss for words. The contact resistance of our general power relays is 100mΩ. 0.2mΩ is 1/500th of that scale and was truly an impossible challenge.
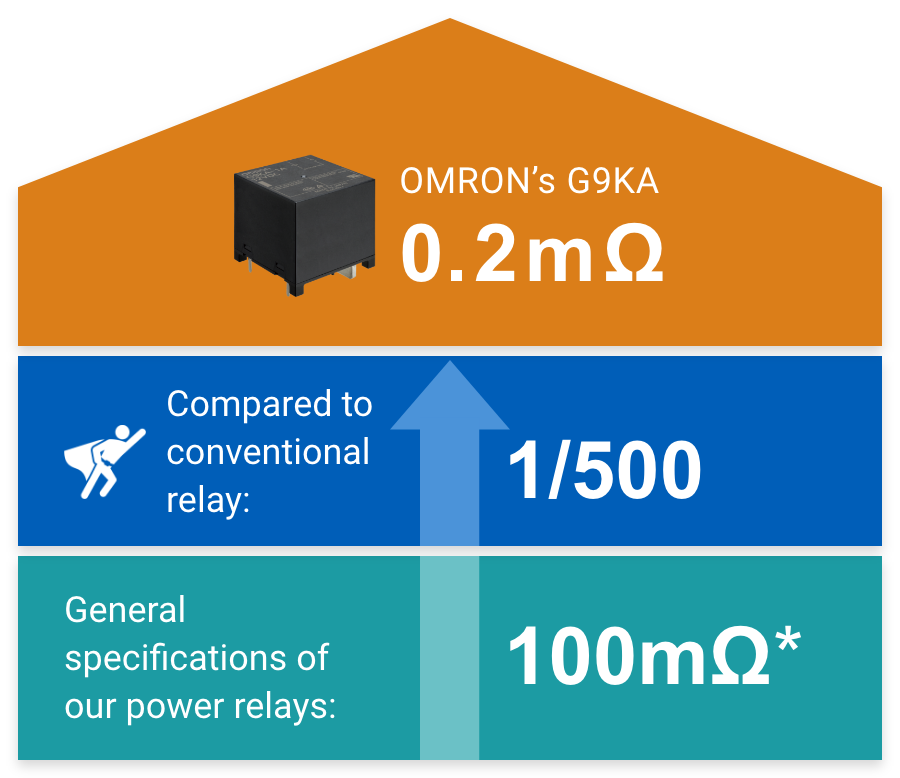
* Note: Measurement conditions and capacity bands vary.
The values are generally listed in our catalogs.
With the completely new, unknown structure, we became spiritually broken many times but giving up was not an option
In addition to realizing "ultra-low contact resistance of 0.2mΩ or less," realizing "high-capacity 200A switching" is a conflicting requirement for relays. In attempting to realize both of these, we concluded that a unique structure that defies conventional wisdom is essential. We spent an enormous amount of effort and time, more than 10 times as much as before, to build a desk theory, including preliminary experiments. Although we managed to create a "desk theory", when we proposed this to the relevant departments, there was a negative atmosphere of doubt about the feasibility of a structure that had never been seen before.
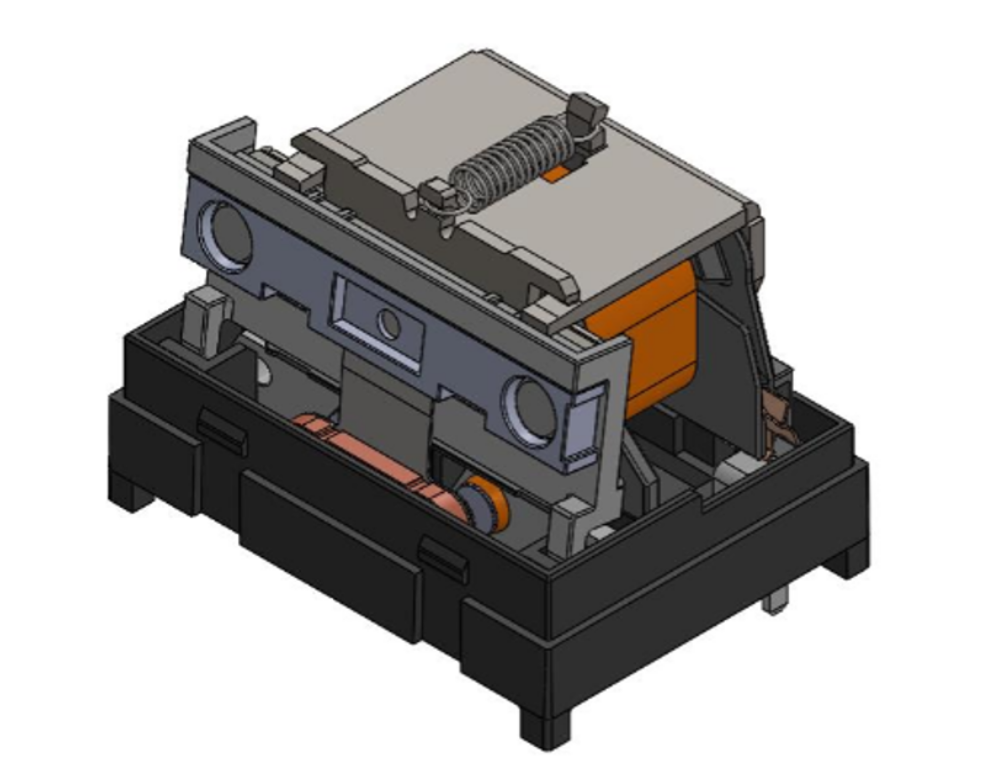
Conventional high-capacity relay structure
(100A class)
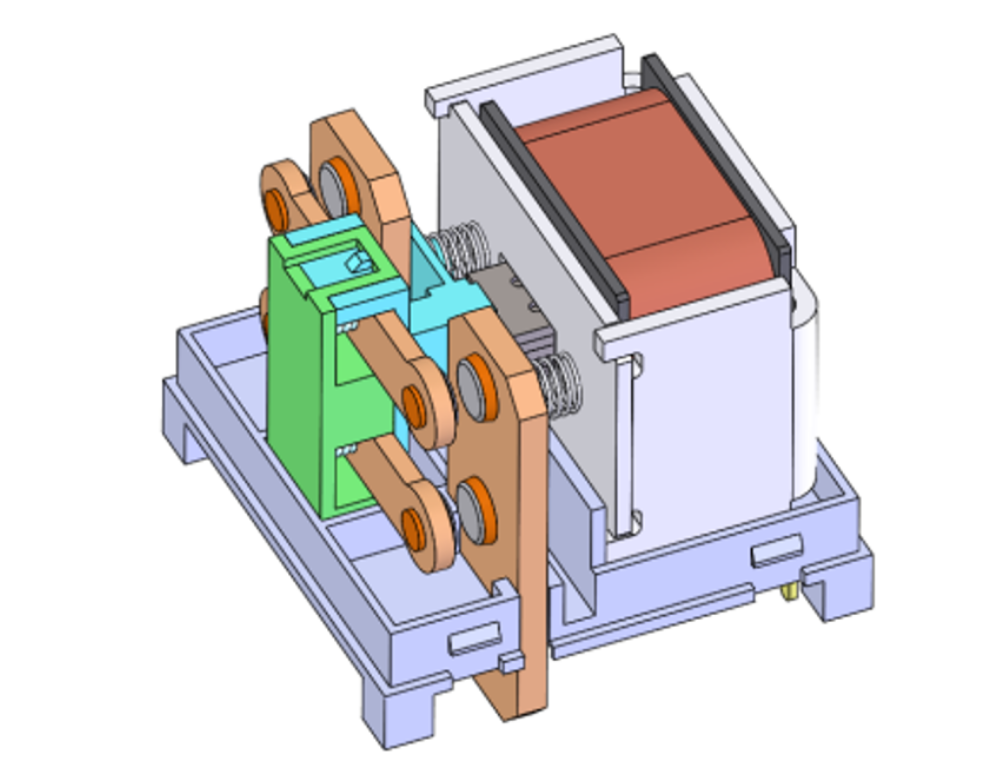
Conceptual model at the beginning of G9KA development
High-capacity (200A) & ultra-low contact resistance
Relays have a kind of general "framework", and even a new product is like a modification of the base "framework". However, this time it was necessary to come up with a completely new structure that did not fit into the "framework".
The G9KA uses a double-break twin contact structure to achieve two contradictory values: high current of 200A and ultra-low contact resistance of 0.2mΩ. In other words, it has four points of contact. The behavior of the four contacts when the relay turns on and off were unimaginable. However, the high current switching in a consumer-use relay requires a large insulation distance, which is not required for automotive relays. This must be understood with a small relay mounted on a PCB. We explored all possibilities to see if we could utilize the structure of various types of relays, such as DC power relays, relays for industrial equipment, and relays for automotive applications. Day in and day out, we were glued to the model and drew blueprints. Due to the lack of precedent, we conducted dozens or hundreds of steady analyses, performed experimental verifications, and reflected the technology in our construction and design.
We do not know how many times we hit a wall without finding a solution, how many times we almost canceled the theme, and how many times we thought, "We may not make it”. Nevertheless, giving it up was not an option because we had a strong sense of mission to "solve the social issue at any cost". OMRON has accumulated technologies since its foundation and has many relay experts and respected senior engineers. Believing that "We can definitely do it!", we continued to talk to a large number of members, and eventually we proceeded with "concurrent development" from the upstream stage of development with more than four times as many people as before.
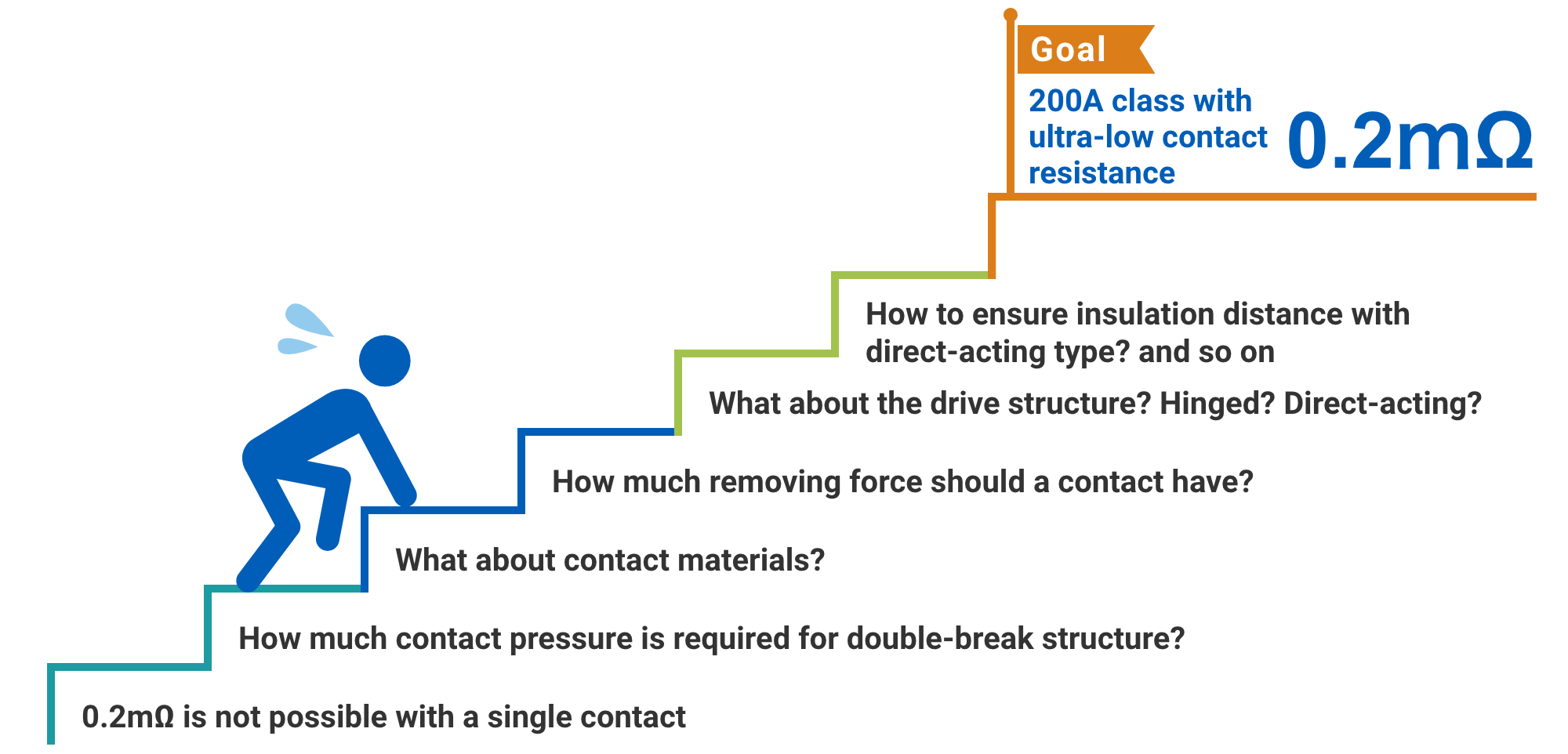
The 0.2mΩ cliff that we all faced in "concurrent development"
The goal of "taking on the challenge of unprecedented development" was achieved by reforming the development system. Until then, OMRON's style had been for the Product Development Department to take the lead in the design and review the prototype when it was nearly complete. With our many years of experience and know-how, and because the relay had a certain degree of "framework", we were still able to handle the situation. However, the same approach as before will never work for a product with an all-new structure, and development will have to be backtracked many times. As a result, we were unable to deliver the G9KA quickly to our customers who have been waiting for it. Therefore, we achieved a change from the traditional "review style" to a "collaborative development style" involving related departments from the early stages of development.
I believe that the establishment of this "concurrent development" system is the first step toward a strong organizational structure capable of accelerating OMRON's future product development and responding to highly challenging social needs.
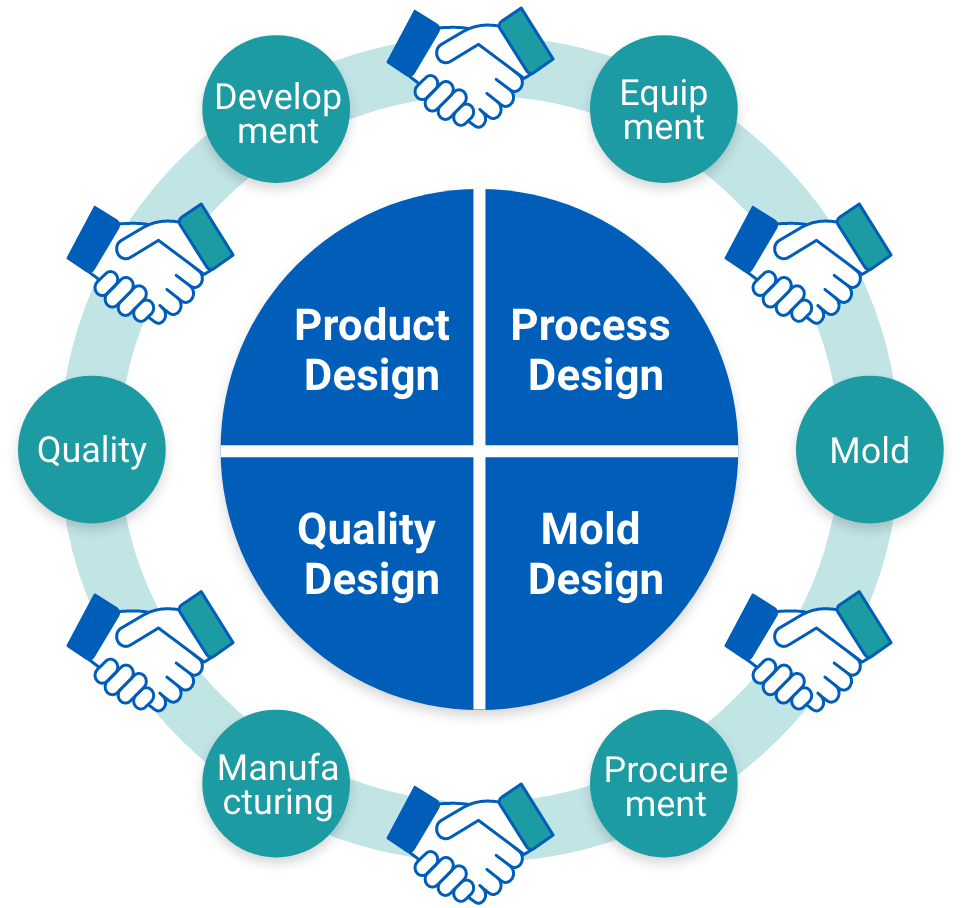
What we valued was "dialogue" and "unity"
However, just because a large number of human resources were gathered did not mean that development could move forward smoothly.
The excessive number of people in the group caused misunderstandings, and the gathering of experts in various fields frequently led to conflicts between various technical concerns.
"We can't keep going like this!" We decided to set up a project area in our laboratory to create an environment where members could gather quickly. In order to unify the goals and opinions of more than four times as many members as before, we decided to create a system to thoroughly discuss the specialization of each department. Then, through continuous "dialogue" with the team for an hour every day, sometimes for half a day or more, we worked out what was the "best for our customers" and, step by step, steadily cleared the challenging issues and incorporated them into the design.
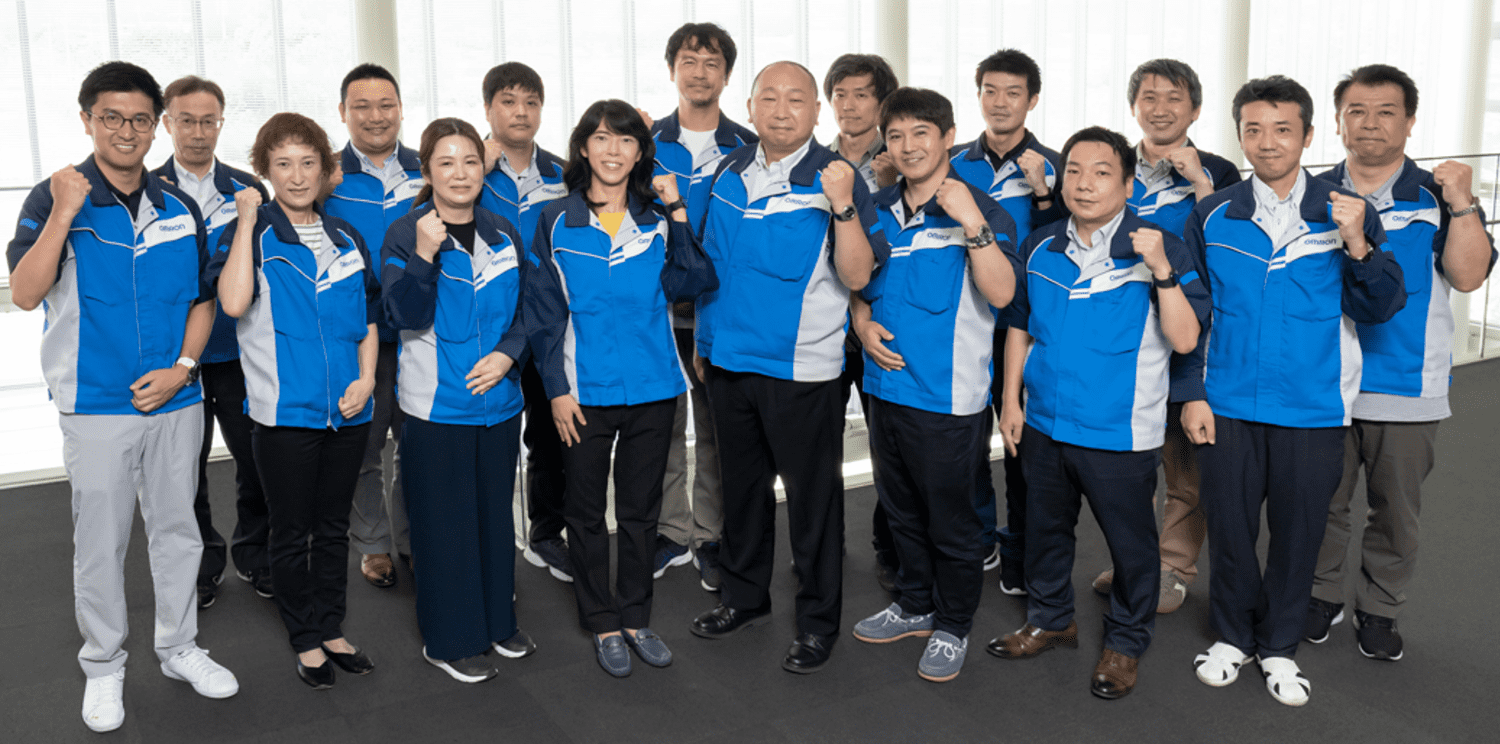
The actual production of the resulting structure was a series of even more unimaginable barriers. With an all-new structure, the components used and the assembly method are completely unprecedented. When it came time to mass-produce the product, problems occurred frequently every day during the prototype stage. It was really a trial-and-error process every day.
Ceaseless challenges led to great results
The number of analyses and experiments we conducted ultimately amounted to approximately 660, a vast number that is more than 10 times the number of previous studies.
Finally, we gave birth to G9KA. We created many firsts in OMRON's relay structures and construction methods and applied for 16 patents*.
* As of October 2022

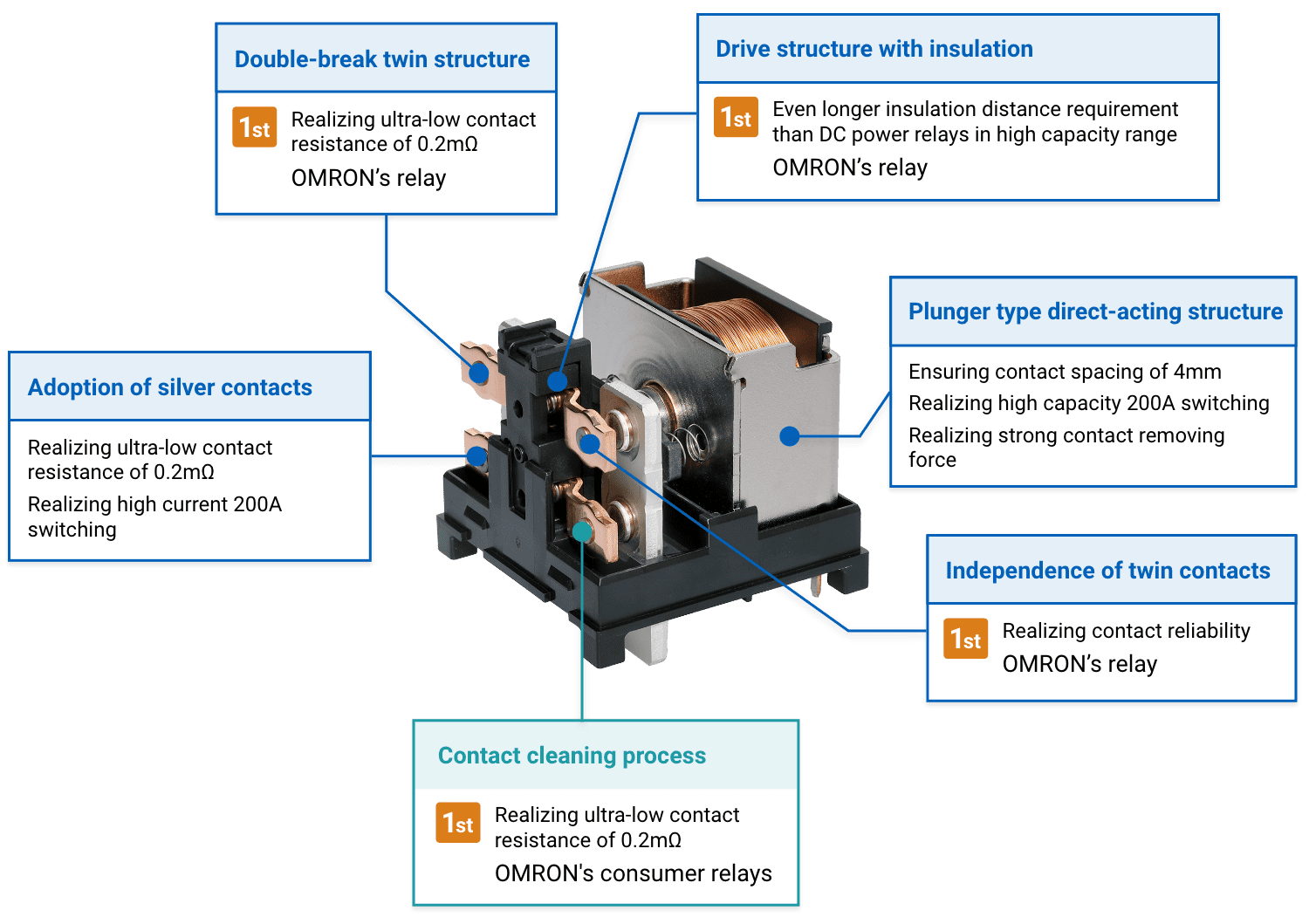
In 2021, we received the "Environment, Resources, and Energy Related Parts Award" of the Cho Monodzukuri Grand Award for Parts.
The recognition from society like this was a joyful moment for us to realize that our challenge had been recognized.
Dreaming of a carbon-neutral society created by G9KA like our own child developed by us
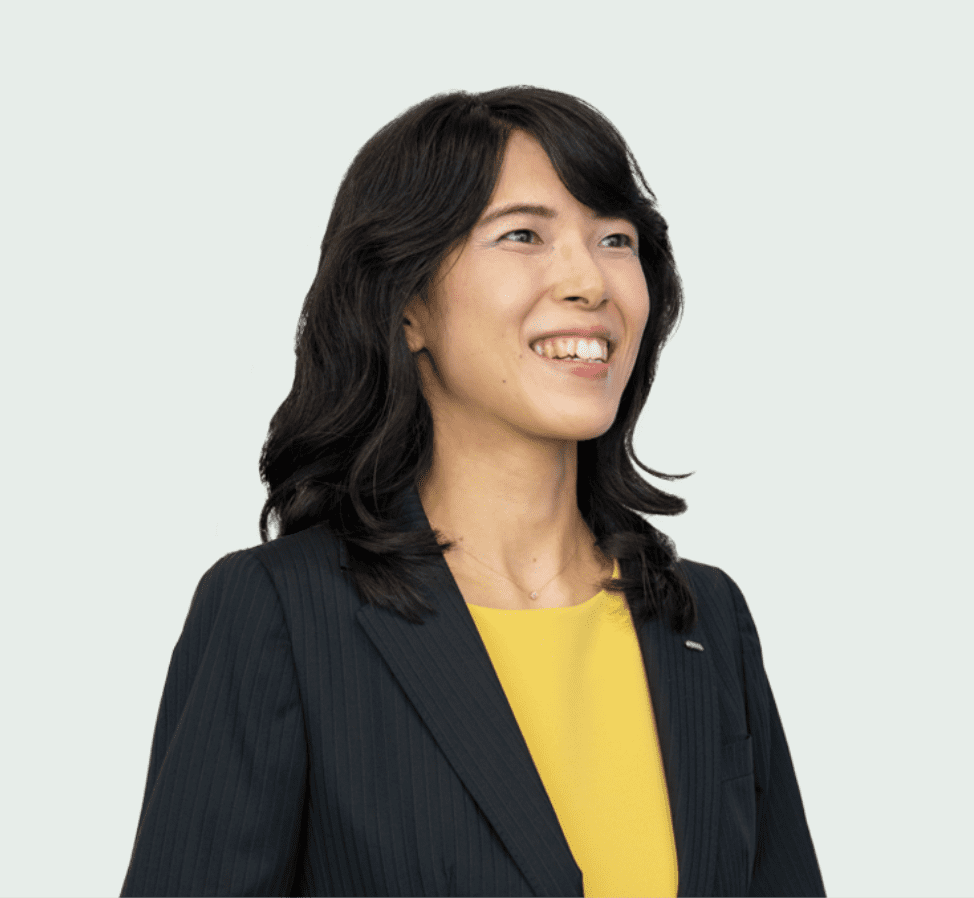
I have been involved in the development of new relay products ever since I joined OMRON, but this project was the most challenging for me and the project with the largest number of members involved. To be honest, the development of the G9KA was not very smooth and we almost gave up many times. However, we managed to launch the G9KA with a strong sense of mission and conviction to "contribute to solving the social issue at any cost" and "meet the expectations of our customers".
The G9KA was the most difficult product for me to work with, and it is like my own child in need of help. We hope to deliver our pride and joy to our customers around the world with the value that we can proudly introduce to them.

Aiming for even higher capacity and temperature suppression, we have begun designing products that take into account "high heat dissipation" in addition to "low heat generation".
I believe that in the future, society's needs will become even more complex and there will be a lot of challenging demands coming for relays. Efforts to achieve carbon neutrality will be strengthened around the world even more than before.
By leveraging our experience with the G9KA and responding flexibly and quickly to new social needs, I hope to expand into all types of clean energy, including EV chargers, in addition to the solar power generation we have targeted this time. Therefore, I believe it is necessary not only to improve our own technical skills, but also to strengthen our organizational capabilities.
In order to successfully complete this highly challenging project, we implemented a process called "concurrent development", which involves members of all fields from the upstream stages of development. I would like to make "concurrent development" more widespread and deployed throughout our organization to respond to increasingly complex needs, and to propose solutions to our customers with "devices and modules" that go beyond the framework of a single relay.
We have also started developing new relays for high-capacity applications by applying lots of technologies and knowledge we have accumulated through the development of the G9KA. Please look forward to OMRON's relays in the future.