Omron Taiyo has been conducting Turn Around Activities (nTA Activities) since 2007 with the intention to enhance productivity and promote personnel development.
In its nTA Activities, Omron Taiyo has continuously worked to promote productivity gains through man hour reductions, predetermined quality indicator arrangements and function enlargements, and appropriate inventory management through life cycle assessment-based analysis and measures such as the application of jigs and industrial engineering improvements. In personnel development, nTA Activities comprise strengthening the management capabilities of managers and supervisors and nurturing human resources to the level of the future leadership class.
Through these measures all employees aim to create lively and rewarding work environments for persons with severe occupational disabilities where every single employee takes the position of a central individual in an independent company that offers a wealth of rewarding work and purpose.


- Inventory reduction from 1.27 months to 1.0 month
- 20% reduction in actual man hours of product A
- 20% productivity gain in product B

- 17% reduction in actual man hours of product C
- 50% reduction in rejects and the non-conformity ratio of product D
- 13% productivity gain through implification and standardization of work activity A

- 10% reduction in shipment man hours
- 10% reduction in rejects ratio of product E
- 5% gain in the operating ratio of line A
- 10% reduction in in-house man hours

- 20% reduction in man hours of work activity B
- 10% reduction in planning and logistics man hours
- 50% reduction in clerical operations man hours
- Operating ratio of device A improved from 85.2% to 91%

- 13% improvement in the yield rate of product F
- 10% productivity gain in product G
- 10% reduction in man hours for manufacturing control operations
- 20% reduction in shipment inspection operations

- 10% productivity gain in line B
- 70% reduction in waste and defects
- 20% efficiency gain in indirect operations

- L/T for product H reduced from 8 days to 3 days
- 60% productivity gain through comprehensive improvements and work scope enlargement

- 8% reduction in operations man hours by introduction of BIEE into operations
- Work scope enlargement through productivity gain in product I (20% man hour reduction)
- Steps to wider hiring of employees with severe disabilities

- Acquisition and improvement of group companies' indirect operations (15% man hour reduction)
- Improved profitability of product J (105% improvement compared with the previous year)
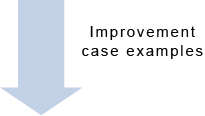
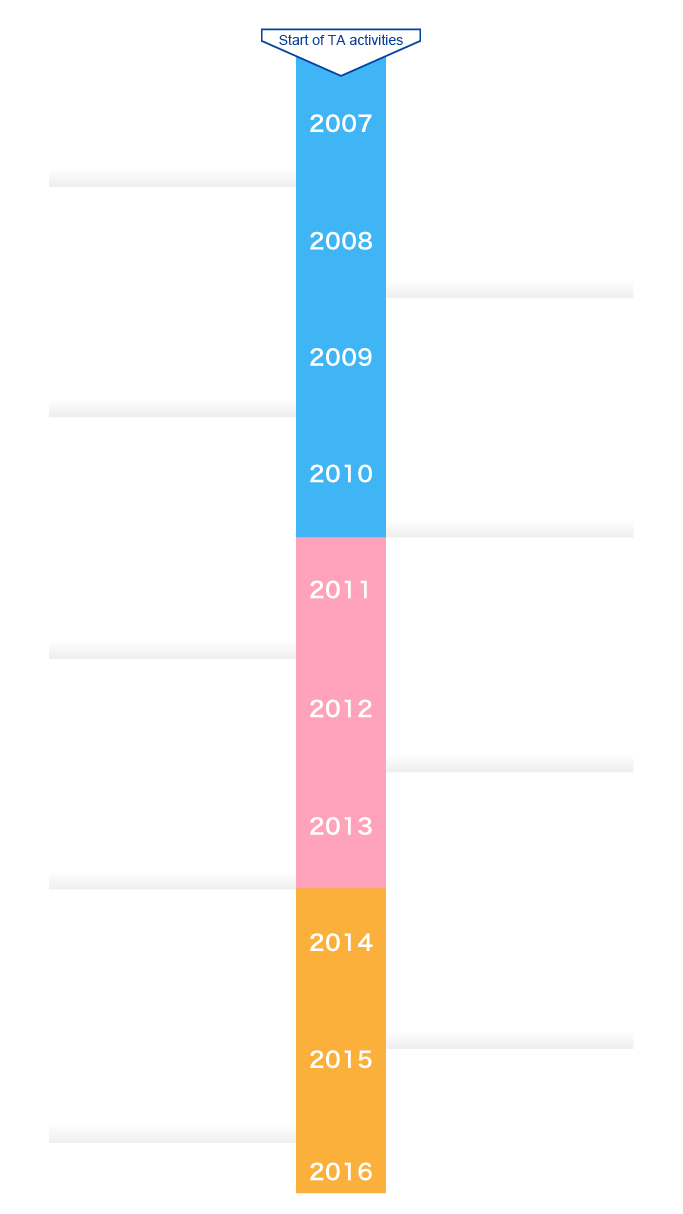
1. Introduction of equipment to assist in the work operations of wheelchair users
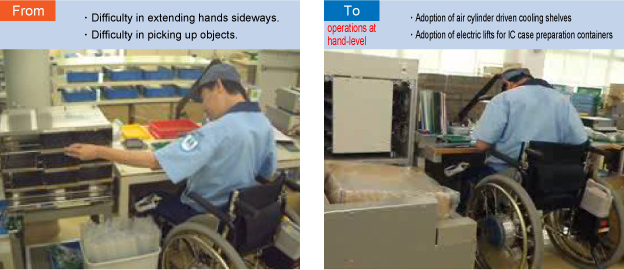
2. Adoption of jigs for the streamlining of installation work operations
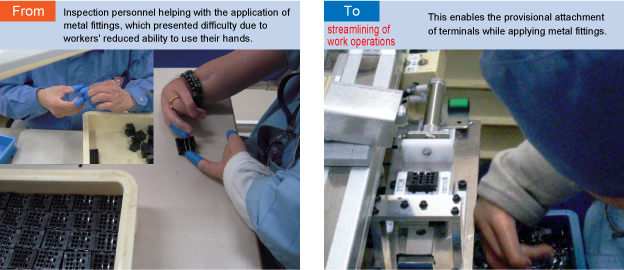
3. No more complicated work after the simplification of work procedures
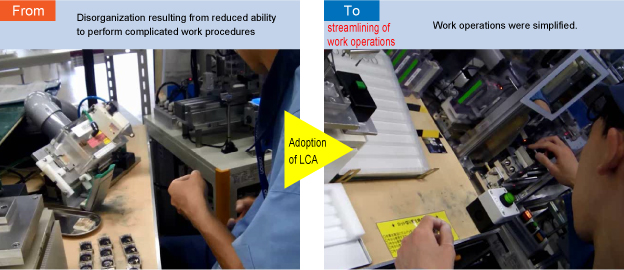
The range of work within the ability of workers with severe disabilities increased from three to eight work operations, thus achieving a broader scope of work.
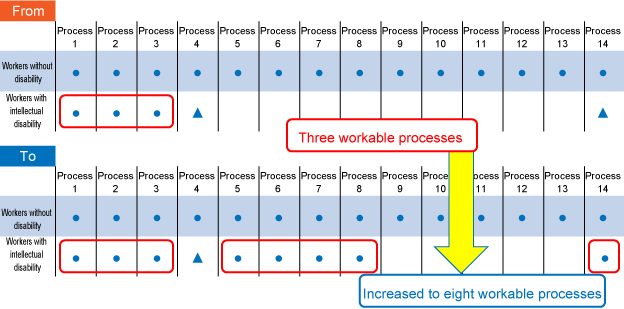
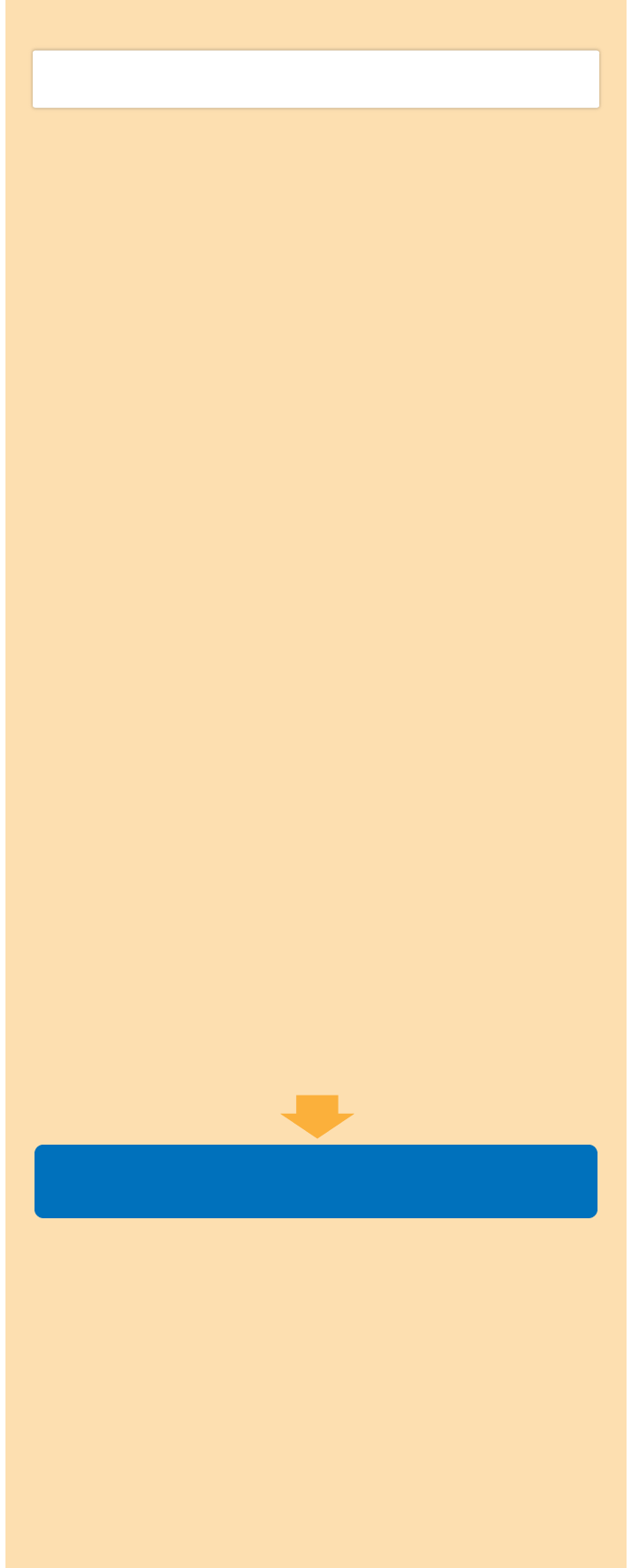