Main text starts here
Each individual handicap is overcome through daily creativity and ingenuity.
Click the buttons below to display examples in each category
All
Improvement of inspection position aligned with the disability
Product and material microscope inspection operations
Expansion of occupational range productivity
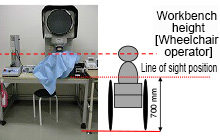
Work table used by non-handicapped person.
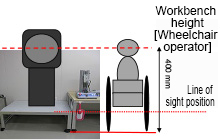
The line of sight position of wheelchair operators, and the working table height, were taken into consideration to enable wheelchair operations.
Introduction of new devices to the factory with issues
Thermal caulking operation of cases and foundations
Quality Productivity
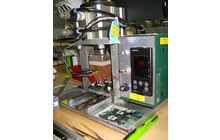
(1) It took a lot of time to adjust when changing procedures.
(2) Heater temperature management was difficult.
(3) Counter display was difficult to see.
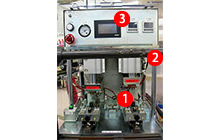
(1) Introduction of exclusive parts made adjustment when changing procedures unnecessary.
(2) Stabilized through increased heater installation.
(3) Installed easily visibility touch panel, enabling visualization of conditions.
Use of jigs for bracket mounting operation to workpiece
Bracket mounting
Quality Expansion of occupational range Productivity
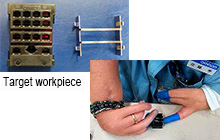
For persons with disability with little power in their fingertips, mounting operations were difficult.
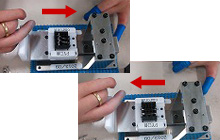
With a bracket-mounted jig, it is now possible for anyone to perform the operation, with the operation shortened from 8 seconds per item to just 3 seconds.
Improvement of inspection process
Operation to insert workpiece into inspection device after fitting operation
Productivity
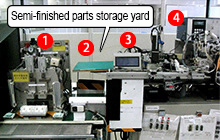
(1) Workpiece after fitting operation
(2) Shifter
(3) Belt conveyor
(4) Inspection device
Because of the existence of a shifter process, the number of workpieces inserted was limited.
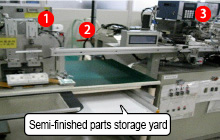
(1) Workpiece after fitting operation
(2) Belt conveyor
(3) Inspection device
The belt conveyor was extended, and the shifter process eliminated, increasing the number of workpieces that are inserted.
Stabilization of soldering operation with use of fixing jig
Lead wire soldering operation
Productivity
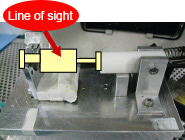
When performing the soldering operation, the act of looking into the operations area caused fatigue for the operator.
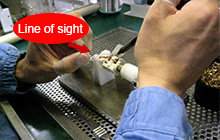
A fixing jig enabled alignment with the operator's line of sight position, achieving reduction of operator fatigue.
Use of jig for simplification of stamping operation
Lot number stamping operation
Quality Productivity
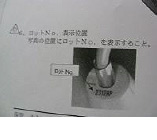
Because it is a manual operation, scattering of the stamp location occurred.
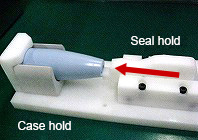
With a fixing jig, equalization of the stamp location shortened the operation from 10 seconds per item to just 4 seconds.
Utilization of jig for simplification of parts assembly method
Shaft assembly operation
Expansion of occupational range Productivity
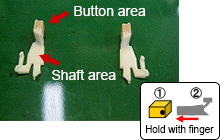
Operation for holding down a small part with the fingers required experience, and operators were limited.
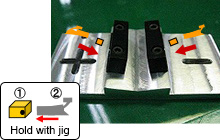
With a jig holding down the part, it became possible for anyone to perform the operation, with the operation shortened from 10 seconds per item to just 7-8 seconds.
Review of line for productivity improvement
Line integration
Productivity
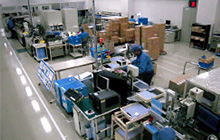
The previous line positioned persons at each process.
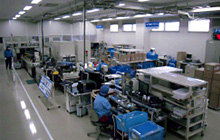
Multiple processes can now be performed in a single process.
Facility improvements for increased efficiency
Wiper height inspection
Expansion of occupational range Productivity
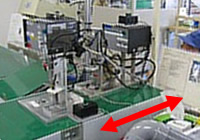
When changing procedures, the inspection facility needed to be moved, which was a difficult operation for wheelchair operators.
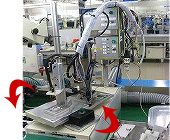
The inspection facility can now be rotated, making changing procedures simple even for wheelchair operators.
Streamlining of applying bonding agent to lead wires
Applying bonding agent to lead wires of switches
Work scope enlargementQualityProductivity
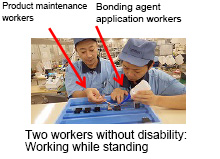
This used to be a difficult work process requiring two workers with experience in bonding agent application who must operate standing.
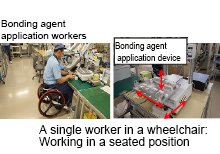
Introduction of bonding devices streamlined the work process by achieving semi-automation. This enabled work performance by a single wheel-chaired worker and achieved work scope enlargement. Execution of the work process was enabled also through workers not pre-determined for this process.
Improvement of the stamping process
Product type and lot number are stamped, followed by the combining of the products
Work scope enlargementQuality
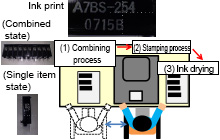
Combining the products used to be time consuming, the adjustment of the stamping machine's rubber stamp was difficult, and the work required pre-determined personnel. (45 seconds per combining process) The stamping ink required time for drying. (2 hours drying time)
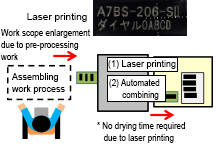
By introducing laser markers and combining automation devices, the time for printing stamp adjustments and ink drying time could be saved. This has allowed workers to incorporate the pre-processing work, thus achieving work scope enlargement. Execution of the work process was enabled also through workers not predetermined for this process.
Work process improvement for wheel-chaired workers
Work comprised of caulking the pins of components A and B to the products and assembling component C
Work scope enlargementProductivity
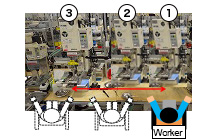
Sideway movements to execute the next work process used to be difficult for wheel-chaired workers. (5 seconds per sideway movement)
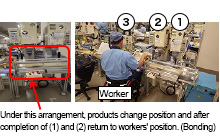
The introduction of jigs that move the positions of products obviates the need for wheel-chaired workers to move.
Improvement of inspection devices by adjustments consistent with the disability
Work process of assessing product conformity using inspection devices
Work scope enlargementQuality
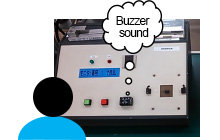
A buzzer used to sound when a product was found non-conforming during an inspection. Non-conforming products were collected in designated red containers but the process was left to workers discretion.
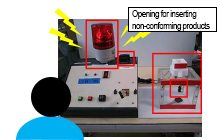
By additionally equipping inspection devices with rotating warning lamps, thus alerting inspection workers by sound and sight, the scope of work is enlarged to workers with a hearing disability. Causing inspection devices to stop operating if a non-conforming product is not placed into the designated red container helps prevent human error.
Reduced work load of press-fitting
Work process of press-fitting of switch cases
Work scope enlargementProductivity
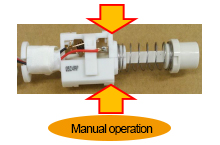
Press-fitting of products used to be done manually. This required physical strength and made this heavy work. (6 seconds per item by a trained worker)
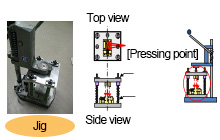
The adoption of press-fitting jigs enabled work execution also by workers not predetermined for this process and reduced the work load. (2 seconds per item).